
OEE: Kennzahlen in Echtzeit verfügbar
Live OEE Maschinendaten für maximale Produktionsleistung
Die Ursachen für eine niedrige Produktivität sind vielfältig. Unerkannte Störungen führen zu langen Wartezeiten, einer reduzierten Geschwindigkeit oder Stillstandszeiten. Nicht selten ist zudem eine Nachbearbeitung verschiedener Werkteile nötig.
Mit den Lösungen der Promatix GmbH für eine maximale Gesamtanlageneffektivität (GAE) genannt auch (Overall Equipment Effectiveness=OEE) werden Probleme in der Produktion in Echtzeit erkannt und können somit schnell behoben werden. Der OEE Wert setzt sich aus drei verschiedenen Faktoren zusammen:
- Leistung (Ist-Leistung/Soll-Leistung)
- Verfügbarkeit der Maschinen (steht oder läuft)
- Qualität der produzierten Teile
Je nach Wunsch kann der OEE pro Auftrag, pro Schicht und für variabel definierte Zeiträume ermittelt werden. Der OEE Wert ergibt sich aus den Daten aller Anlagen der jeweiligen Produktionsstätte. Mit den Lösungen von Promatix kann eine niedrige Produktivität schnell ermittelt und Störungen oder Probleme rasch behoben werden. Promatix gibt dabei genau an, ob die Abweichungen aus der Qualität, der Leistung oder der Verfügbarkeit verursacht sind. Während andere noch die Schwachstelle suchen, implementieren Kunden von Promatix bereits die passende Lösung für eine maximale Produktionsleistung.
Promatix GmbH
Die Promatix GmbH hat sich auf die Optimierung der industriellen Produktion spezialisiert. Entlang der Wertschöpfungskette gibt es zahlreiche Punkte, an denen sich Produktivitätspotentiale verbergen können. Promatix entwickelt Tools und Lösungen um Unternehmenspotentiale aufzuspüren und auszuschöpfen.
Weitere Informationen über die Promatix GmbH finden Interessierte hier.
Promatix GmbH
Uhlmannstrasse 45
88471 Laupheim
Telefon: +49 (7392) 70916-38
http://www.promatix.de
Geschäftsführer
Telefon: +49 (7392) 709-1638
E-Mail: hubert.schoenle@promatix.de
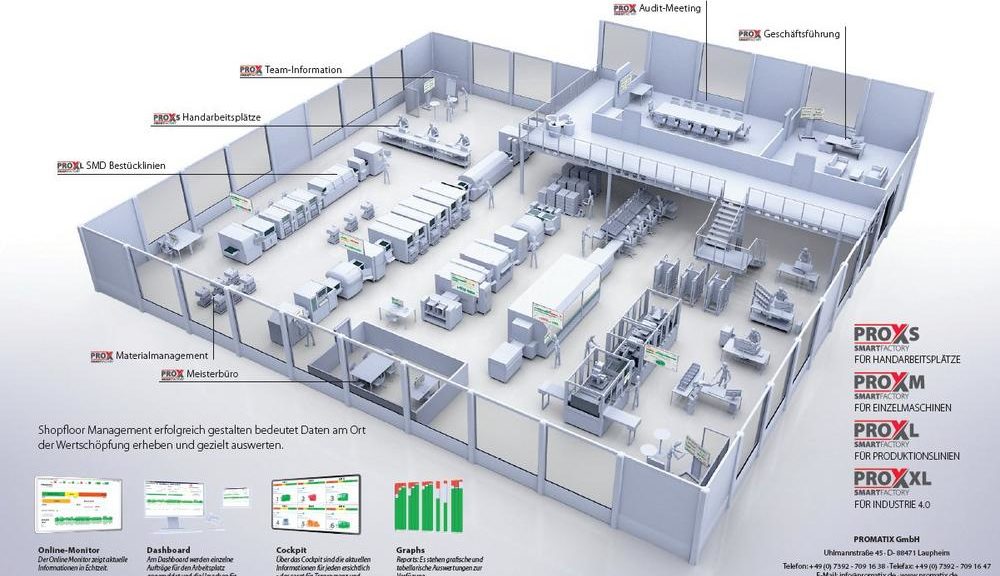
Effektives Shopfloor Management sorgt für Umsatzsteigerung und Entlastung der Belegschaft
Systematisches Shopfloor Management von Promatix
In den Werkshallen produzierender Unternehmen werden täglich eine Vielzahl unterschiedlicher Aufträge bearbeitet. Der Mehrschichtbetrieb, die vielen verschiedenen Prozesse sowie die häufig nur einmal täglich stattfindende BDE Buchung führen zu problematischen, teilweise chaotischen Workflows, die oftmals mit Fehlbeständen oder Mehrbeständen sowie extremen Abweichungen zwischen Planung und Realität einhergehen. Dabei leidet nicht nur die Effektivität des Unternehmens, sondern auch die betroffenen Mitarbeiter.
Mit dem Shopfloor Management der Promatix GmbH können für den Produktionsprozess relevante Daten direkt am Ort der Wertschöpfung erhoben und ausgewertet werden. Maschinen- und Betriebsdaten der Produktionsanlagen werden objektiv und dauerhaft überwacht und können in Echtzeit auf dem Online Monitor in der Cockpit-Darstellung betrachtet werden. Dies sorgt für maximale Transparenz bei der Produktion. Durch die Bereitstellung der erhobenen Informationen werden Mitarbeiter bestens bei ihrer Arbeit unterstützt, wodurch sie sich entlastet fühlen und produktiver arbeiten können. Nach Auswertung der erhobenen Daten können Potentiale bei den Arbeitsprozessen ermittelt und die Produktion optimiert werden.
Interessierte Unternehmen haben die Möglichkeit, sich durch eine kostengünstige, unverbindliche und risikofreie Probeinstallation vom innovativen System der Promatix GmbH überzeugen zu lassen.
Die Promatix GmbH ist ein professionelles Unternehmen für die Optimierung der industriellen Produktion. Das Unternehmen entwickelt Tools und Lösungen um Unternehmenspotentiale aufzuspüren und auszuschöpfen.
Weitere Informationen über die Promatix GmbH finden Interessierte [url=http://www.promatix.de/]hier[/url].
Promatix GmbH
Uhlmannstrasse 45
88471 Laupheim
Telefon: +49 (7392) 70916-38
http://www.promatix.de
Geschäftsführer
Telefon: +49 (7392) 709-1638
E-Mail: hubert.schoenle@promatix.de
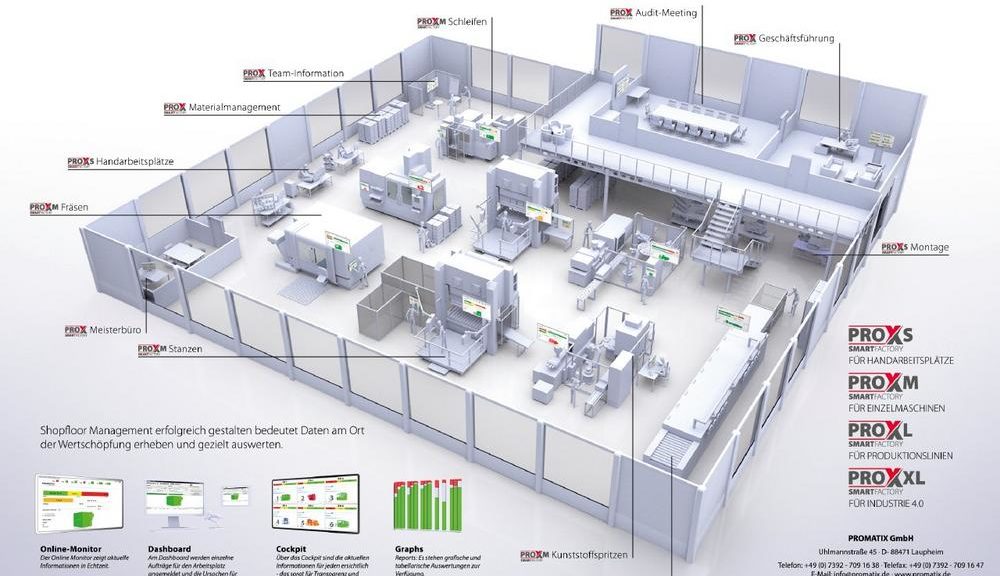
Innovatives Smart Factory System der Promatix GmbH ermöglicht Digitalisierung selbst alter Industriemaschinen und sorgt somit für höhere Umsätze
Smart Factory System der Promatrix GmbH
Produktionsunternehmen verfügen über eine Vielzahl an Anlagen und Maschinen. Teure Sonderanlagen erbringen oft erst nach mehreren Jahren ihre zugedachte Leistung. Ist der Reifegrad der Anlage endlich erreicht, scheuen sich die Verantwortlichen oft aus Angst die Funktion der Maschine zu gefährden, entsprechende Digitalisierungseingriffe durchführen zu lassen.
Viele Unternehmen halten es außerdem für unmöglich, einen heterogenen Maschinenpark, der aus einer Vielzahl an Maschinen von unterschiedlichen Herstellern besteht, erfolgreich zu digitalisieren.
Egal von welchem Hersteller und wie alt eine Maschine ist, mit ihrem innovativen Smart Factory System kann die Promatix GmbH jede Maschine und Anlage digitalisieren, ohne die bestehende Funktion der Anlage zu beeinträchtigen. Die relevanten Maschinendaten werden dabei automatisch digital erfasst. Anschließend folgt ein Abgleich mit den Plandaten, wodurch Abweichungen in Echtzeit erkannt, gemessen und dargestellt werden können.
Das Smart Factory System unterstützt den Operator durch vielfältige Funktionen wie zum Beispiel:
- automatische BDE Buchung
- Service Call
- online Monitor in Echtzeit
- Verschleißüberwachung
- komfortables Reporting der Unterbrechungsursachen
Durch die Cockpit Funktion wird zudem das Management unterstützt. Der Nutzer profitiert von einer gezielten Analyse der Optimierungsmöglichkeiten sowie von der Transparenz rund um die Produktionsprozesse.
Mit der Digitalisierung seiner Anlagen und Maschinen und den daraus abgeleiteten Maßnahmen kann ein Unternehmen eine Effektivitätssteigerung von bis zu 30% und mehr erreichen.
Die Promatix GmbH ist ein professionelles Unternehmen für die Produktivitätssteigerung in Produktionsbetrieben mit diskreter Fertigung. Das Unternehmen entwickelt Tools und Lösungen um Unternehmenspotentiale aufzuspüren und auszuschöpfen.
Weitere Informationen über die Promatix GmbH finden Interessierte [url=http://www.promatix.de/]hier[/url].
Promatix GmbH
Uhlmannstrasse 45
88471 Laupheim
Telefon: +49 (7392) 70916-38
http://www.promatix.de
Geschäftsführer
Telefon: +49 (7392) 709-1638
E-Mail: hubert.schoenle@promatix.de
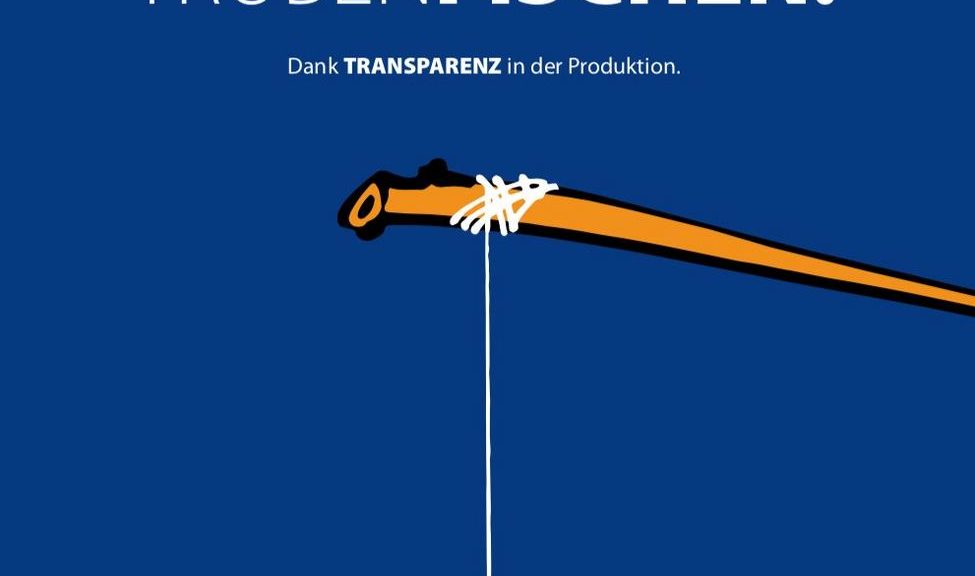
Wie Industrieunternehmen auch ohne teure Investitionen mehr Aufträge umsetzen können
Nicht immer sind fehlende Aufträge das Problem. Für die deutsche Industrie sind die Produktions- und Wachstumsaussichten nämlich sehr gut. Viele Unternehmen kommen hier jedoch an ihre Grenzen. Statt direkt in neue Maschinen zu investieren, lohnt es sich aber, die vorhandenen Fertigungsprozesse zunächst zu optimieren.
Schnelle Investitionen meist nicht möglich und sinnvoll
Volle Auftragsbücher wünscht sich eigentlich jedes Unternehmen. Spätestens wenn die Produktion an ihre Grenzen kommt und Ressourcen wie Maschinen oder Personal knapp werden, steigt jedoch die Anspannung in der Geschäftsführung: Fällt beispielsweise eine Maschine aus, können Deadlines oft nicht mehr eingehalten werden. Das führt wiederum zu verspäteten Lieferterminen und unzufriedenen Kunden.
Investitionen in neue Maschinen und mehr Personal sind daher häufig die erste Überlegung für Verantwortliche in Industrieunternehmen. Diese sind allerdings kurzfristig meist nicht umsetzbar und lohnen sich nur, wenn eine generelle Wachstumsstrategie angestrebt wird.
Optimieren statt investieren – mit der PRO X SMART FACTORY
Eine sinnvolle Alternative zu kostspieligen Investitionen sind Verbesserungen der bestehenden Produktionsabläufe. Optimierungspotenziale vorhandener Maschinen und Fertigungsstraßen werden nämlich oft nicht ausgeschöpft, da sie mit den herkömmlichen Methoden schlichtweg nicht erkannt werden.
Das trifft besonders auf komplexe Produktionsumgebungen mit einer Vielzahl von Fertigungsprozessen von manuellen Montagetätigkeiten bis hin zu vollautomatisierten Produktionslinien zu. In diesen ist echte Transparenz, mithilfe derer Prozesse optimiert werden können, ohne ein Shop-Floor-Management-System nicht möglich.
Hier kommt die PRO X SMART FACTORY mit den Lösungen S, M, L und XL ins Spiel. Diese erkennt, erfasst und analysiert selbst kleinste Schwachstellen objektiv, exakt und personalunabhängig – ohne dabei störend in den Produktionsprozess einzugreifen.
Industrieunternehmen gelingt es auf diese Weise, Transparenz zu schaffen und dadurch Optimierungspotenziale aufzudecken. Teure Investitionen in neue Maschinen und mehr Personal sind dadurch nicht notwendig. Stattdessen werden bereits bestehende Abläufe verbessert und die Fertigung so optimiert.
Weitere Informationen unter http://de.promatix.de.
Promatix GmbH
Uhlmannstrasse 45
88471 Laupheim
Telefon: +49 (7392) 70916-38
http://www.promatix.de
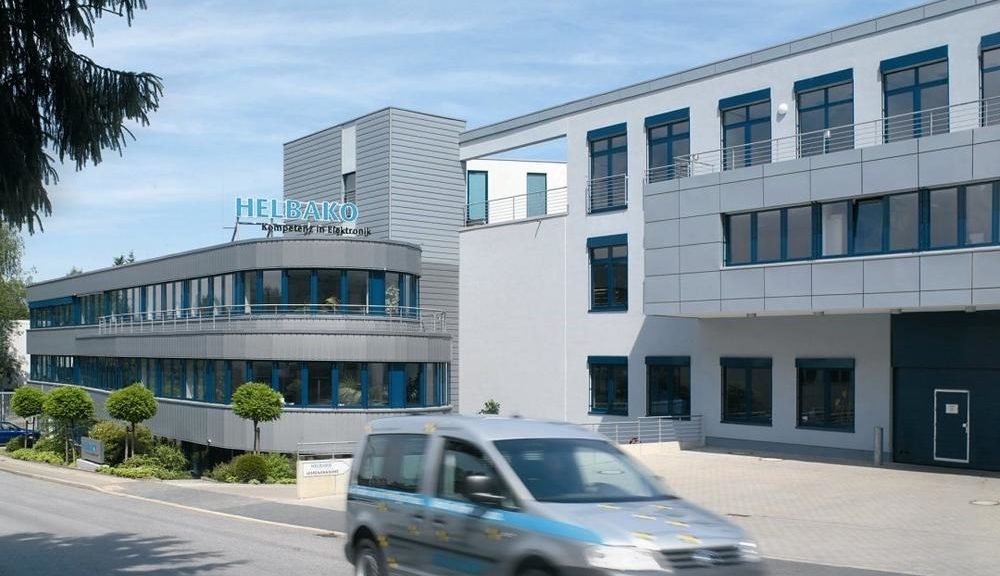
Interview mit Ralf Diepers (RD) und Andreas Schneider (AS)
Im eigenen Entwicklungszentrum mit über 60 Mitarbeitern werden Produkte für unterschiedliche Bereiche am PKW entwickelt. In Heiligenhaus werden die eigenen Produkte entwickelt und hergestellt. Als EMS Dienstleistung werden in kleinem Masse auch Produkte anderer Unternehmen hergestellt.
Die gesamte Organisation ist deshalb zwingend an den für Automobilzulieferer vorgegebenen strengen Erfordernissen (TS16949) ausgerichtet. Prozessorientiertes Denken und das Streben nach kontinuierlicher Verbesserung sind dabei prägend für die Unternehmenskultur geworden.
Eine durchdachte Planung und ein konsequentes Controlling sind dabei wesentliche Stützen des beachtlichen und kontinuierlichen Erfolg des Unternehmens. Die Anlagenproduktivität liegt dabei besonders im Fokus.
Verstecktes Potential
RC: Herr Diepers, was hat Sie auf die Idee gebracht, Produktionsdaten automatisiert zu ermitteln?
RD: Wir wussten, dass bei der Anlagenproduktivität ein noch ungenutztes Potential liegt, dies konnte unser Produktionscontrolling eindeutig nachweisen. Für mich als Leiter der Fertigung stellte sich die Frage, wie ich dieses Potential möglichst schnell identifizieren und heben konnte. Übliche Verbesserungsmöglichkeiten wie z.Bsp. Wartungs- oder Rüstoptimierungen wurden zwar durchgeführt, deren Nachhaltigkeit war jedoch nur über aufwändige Zeitstudien und Analysen nachzuweisen.
Da wir im Dreischichtbetrieb arbeiten war mir klar, dass wir nur dann weitere Produktivitätssteigerung erzielen können, wenn wir eine automatisierte Datenermittlung und Auswertung durchführen. Einzelne Anlagen in unserem SMD Bereich verfügten bereits über Möglichkeiten zur Datenanalyse, allerdings waren die Auswirkungen von Störungen oder Optimierungen einzelner Anlagen auf die Gesamtverfügbarkeit der SMT-Linie nicht immer nachvollziehbar.
Mit den bisherigen Auswertungen konnten wir die uns gesteckten Produktivitätsziele nicht erreichen.
Suche
RC: Wie kamen Sie denn in diesem Zusammenhang auf Promatix?
RD: Bei der Suche nach einer geeigneten Lösung schaute ich mir auf einer Messe das Promatix System „Linealyzer“ an. Dargestellt wurde die Auswertung eine SMD Linie die quasi unserer Linienkonfiguration entsprach. Interessant war, dass das System universell verwendbar ist – sowohl für SMD Linien als auch für andere Anlagen. Da wir sowohl SMD Linien als auch automatisierte Systeme im Backendbereich analysieren wollten, konnten wir diese mit einem einheitlichen System ausstatten. Konkret 3 SMD Linien und 2 Anlagen im Backendbereich.
Obwohl die Anforderungen an ein Produktionsdatenerfassungssystem je nach Anwender sehr unterschiedlich sind – von der „Managementübersicht“ bis hin zur „Detailanalyse einzelner Linienstörungen“- sollten diese in einem System realisierbar sein.
Während der Präsentation möglicher Systemauswertungen zeigte sich schnell, dass diese Anforderungen über Promatix realisierbar sind incl. der Anbindung an unser SAP System um die Sollwerte für die Linienleistung zu übernehmen. Auswertungen von Detaildaten wie Rüstzeiten, Störungsgründe und Ähnliches sind auf Knopfdruck verfügbar, so dass aufwendige Zeitstudien und Analysen der Vergangenheit angehören.
Das System bietet somit die Grundlage für schnelle zielgerichtete Analysen zur Produktionsoptimierung.
RC: Sie optimieren also ihre Produktion mit dem Linealyzer?
RD: Ja, das System hat alle Funktionen, die für systematische Analysen und ein Shopfloormanagement erforderlich sind.
Seit 2014 optimieren wir unsere Fertigung mit Lean Ansätzen. Wesentliche Punkte für ein erfolgreiches Lean Management sind die Verringerung von Durchlaufzeiten und die Erhöhungen von Anlagennutzungsgraden.
Das Reporting System von Promatix stellte uns im Lean Projekt die wesentlichen Informationen zur Verfügung um an der richtigen Stelle zu optimieren. Hierbei wurden sowohl technische Störungsgründe als auch organisatorische Themen durch gezielte Datenauswertung aufgezeigt. Nach der Umsetzung von Optimierungen sind die Auswirkungen über das System umgehend erkennbar und auch die Nachhaltigkeit kann kontinuierlich verfolgt werden.
Gerade in Bezug auf die Detailanalysen bei eventuell wieder auftretenden Abweichungen ist das System bei uns zu einem Standardwerkzeug für die Führungskräfte und Produktionsmitarbeiter geworden.
Ich persönlich werde einmal wöchentlich von Hr. Schneider –dem für den SMT Bereich verantwortlichen Gruppenleiter- über die aufgetretenen Probleme und geplanten Abstellmaßnahmen informiert.
RC: Herr Schneider, wie kam das System denn bei Ihren Mitarbeitern an?
AS: Für mich war es von Anfang an wichtig, dass die Mitarbeiter nicht mit zusätzlicher Arbeit belastet werden, die Fehlerkommentierung sollte schnell gehen, und einfach sein.
Dies war durch die Struktur der Bedienoberfläche und des Auswahlmenues gegeben.
Da die Kommentierung der Stillstandszeiten bisher händisch erfolgte, konnte ich an dieser Stelle sogar eine Arbeitserleichterung feststellen.
Durch den Online Monitor über den SMD Linien sind die Kolleginnen und Kollegen immer über den aktuellen Stand der Schicht informiert. Dies hatte bei uns zur Folge, dass das Team aktiv an dem Projekt mitarbeitete, und die Motivation für Verbesserungsvorschläge zugenommen hat.
RC: Herr Schneider, unterstütz Sie das System im Alltag?
AS: Mein Arbeitstag beginnt damit, dass ich mir eine Auswertung aus dem Promatix System über die vergangenen 3 Schichten erstelle. Ich überprüfe den Nutzungsgrad und halte nach Planabweichungen Ausschau. Es geht mir dabei um die 3 größten oder wiederholten ungeplanten Unterbrechungen pro Schicht und deren Ursachen. Auffälligkeiten bespreche ich dann mit meinen Teamleitern.
Bei unserer Shopfloor Managementrunde mit Fertigungs- und Gruppenleiter geht es überwiegend um Themen, welche die Linienausnutzungsgrade steigern sollen. Wir finden mit dem System Linealyzer auf einfache Weise Optimierungspotentiale und kontrollieren damit auch ob die angesetzten Verbesserungen zum Erfolg führten.
Gerade aber auch kleinere Produktionsunterbrechungen, welche in der Vergangenheit nicht dokumentiert wurden, ließen sich mit Hilfe des Linealysers ermitteln.
Uns ist zum Beispiel in den letzten Tagen aufgefallen, dass an einer unserer Linien sporadisch gegen 12.00 h nachts, eine Unterbrechung verursacht durch den Reflow Ofen, entstand. Produktionsunterbrechung < 5min.
Unsere Kollegen der Nachtschicht hatten kommentiert, die Ursache sei eine nicht ausreichende Stickstoffversorgung gewesen. Wir setzten umgehend ein Team zur Fehleranalyse an und konnten innerhalb weniger Tage die Ursache beheben. Wir kontrollieren mit dem Linealyzer nachfolgend, ob der Fehler wieder auftritt, bzw ob unsere durchgeführten Maßnahmen die gewünschte Wirkung zeigen. Ich bin mir sicher, ohne den Linealyzer wäre dieses Phänomen nicht aufgefallen. Dies ist nur 1 Beispiel von vielen.
RC: Sie arbeiten also täglich mit dem System?
Ja, absolut! Natürlich arbeite ich mit dem System täglich, und meine Mitarbeiter auch.
An meinem Arbeitsplatz, und am Arbeitsplatz meiner Teamleiter befindet sich ein Cockpit, das immer den Status der einzelnen Anlage aufzeigt, es sind die Informationen, die auch direkt an der Anlage auf dem Online Monitor den Mitarbeitern zur Verfügung stehen.
Am Anfang, als wir das System eingesetzt hatten, hatte ich die Mitarbeiter an der Anlage angerufen, oder bin direkt hingegangen, wenn eine Unterbrechung mir als zu lange erschien.
Heute ist dies nicht mehr erforderlich, ich bekommen einen Anruf, in dem erklärt wird, was geschehen ist, und was unternommen wird, diesen Zustand schnell zu ändern.
Wir brauchen heute nicht mehr zu diskutieren, ob ein Problem tatsächlich existiert, dies wird uns als Tatsache von dem System mitgeteilt. Wir verwenden unsere Energie dafür, die erforderlichen Dinge systematisch anzugehen und nachhaltig zu lösen.
Das Promatixsystem verhalf uns unbekannte Störgrößen aufzudecken und Verbesserungspotenziale zu ermitteln. Durch die Eliminierung dieser Stillstandzeiten, erreichten wir eine Steigerung der Liniennutzungrade um 26%.
Papierlos
RC: Wenn ich das richtig verstehe, unterstütz das System sowohl das Management als auch die Mitarbeiter in der Produktion?
AS: Das kann man so sagen. Es geht ja auch nur gemeinsam. Wenn die Mitarbeiter keine Mitgestaltungmöglichkeit und keine Vorteile hätten, wäre es ein reines Kontrollsystem. Es würde dann zwar die Leistung anzeigen, aber das wäre dann auch alles. Die Frage, wie diese verbessert werden kann, würde offen bleiben.
Seit unser Schichtbericht auf dem Linealyzer System läuft, arbeiten wir in unserem Bereich papierlos. Das hat den Vorteil, dass die Informationen digital abgelegt sind, mit schneller Zugriffsmöglichkeit. Für die Mitarbeiter bedeutet es eine zeitliche Entlastung, da nur noch Kommentare für außergewöhnliche Ereignisse zu berichten sind, die wesentlichen Angaben sind automatisch von dem System ermittelt.
Promatix hat den Bericht exakt nach unseren Angaben umgesetzt, es war im Grunde ein Gemeinschaftsprojekt.
Rüstprozess
RC: Was zeigt das System an, wenn Sie Umrüsten?
AS: Bedingt durch unsere Auftragsstruktur sind bei uns pro Schicht manchmal mehrere Rüstvorgänge erforderlich. Während des Rüstvorgangs zeigt der Online Monitor die Linie in gelber Farbe an, so dass der Status „Rüsten“ erkennbar ist. Ein Hauptansatz im Leanprojekt war, diese Rüstzeit drastisch zu reduzieren. Der Linealyzer zeigt die Rüstzeit an und zeichnet sie automatisch auf. Dies half uns bei der Ermittlung realer Rüstzeiten.
Außerdem können wir unmittelbar nachhalten, ob unsere Bemühungen um eine Rüstoptimierung erfolgreich sind. Wiederholte Rüstzeitanalysen zwischen der theoretisch ermittelten und realen Rüstzeit sind problemlos und ohne weiteres Personal durchführbar.
Überblick / Kennzahlen
RC: Das hört sich so an, dass Sie immer damit arbeiten, wenn etwas nicht klappt wie geplant?
AS: Wenn Sie das so sehen – ja, immer wenn eine Kennzahl vom Plan abweicht, wollen wir wissen warum, dafür haben wir das System. Es hilft uns, schnell besser zu werden, mit der notwendigen Transparenz.
Mit der Cockpitfunktion habe ich alle wesentlichen Informationen auf einem Bildschirm, und kann den jederzeit über mein Smartphone einsehen, egal wo ich bin (Empfang vorausgesetzt) und egal um welche Zeit. Diese Funktion nutze ich seit bereits 3 Jahren.
RC: Ich bedanke mich für Ihre Ausführungen!
Promatix GmbH
Uhlmannstrasse 45
88471 Laupheim
Telefon: +49 (7392) 70916-38
http://www.promatix.de
Geschäftsführer
Telefon: +49 (7392) 709-1638
E-Mail: hubert.schoenle@promatix.de

Anlagenproduktivität im Fokus
Helbako ist ein mittelständischer Automobilzulieferer mit Hauptsitz in Heiligenhaus. Mit etwa 260 Mitarbeitern produziert das Familienunternehmen hier jährlich 5 Mio. elektronische Steuerungsmodule. Seit 2015 wird auch am chinesischen Fertigungsstandort in Ningbo produziert und für den europäischen Markt befindet sich ein neuer Entwicklungs- und Fertigungsstandort in Osteuropa in der Umsetzung. Im eigenen Entwicklungszentrum mit über 60 Mitarbeitern entstehen Produkte für unterschiedliche Bereiche am Personenkraftfahrzeug. Als EMS-Dienstleistung werden in kleinem Maße auch Produkte anderer Unternehmen hergestellt. Die gesamte Organisation ist deshalb zwingend an den für Automobilzulieferer vorgegebenen strengen Erfordernissen (TS16949) ausgerichtet. Prozessorientiertes Denken und das Streben nach kontinuierlicher Verbesserung sind dabei prägend für die Unternehmenskultur geworden. "Unser Fokus liegt auf der Anlagenproduktivität, wir denken prozessorientiert und streben mit durchdachter Planung und konsequentem Controlling kontinuierlich nach Verbesserungen", erklärt der Fertigungsleiter, Ralf Diepers.
Verstecktes Potential
Als daher das Productcontrolling eindeutig ungenutztes Potential bei der Anlagenproduktivität nachweisen konnte, galt es, dieses möglichst schnell zu identifizieren und zu nutzen. Da das Unternehmen im Dreischichtbetrieb arbeitet, war schnell klar, dass nur eine automatisierte Datenermittlung und Auswertung zu einer weiteren Produktivitätssteigerung führen konnte. Zwar verfügten einzelne Anlagen im SMT-Bereich über Datenanalysefunktionen, die Auswirkungen von Störungen oder Optimierungen einzelner Anlagen auf die Gesamtverfügbarkeit der SMTLinie waren allerdings nicht immer nachvollziehbar und die gesteckten Produktivitätsziele ließen sich so nicht erreichen.
Auf der Suche
"Bei der Suche nach einer geeigneten Lösung stießen wir auf das Promatix-System Linealyzer. Dargestellt war die Auswertung einer SMT-Linie die quasi unserer Linienkonfiguration entsprach", erinnert sich Diepers. Zudem war das System für SMT-Linien ebenso wie für andere Anlagen ausgelegt. Helbako wollte drei SMT-Linien und zwei automatisierte Anlagen im Backendbereich analysieren und zwar mit einem einheitlichen System.
Der Linealyzer deckt von der Managementübersicht bis hin zur Detailanalyse einzelner Linienstörungen alle Anforderungen an ein Produktionsdatenerfassungssystem ab und ermöglicht auch die Anbindung an das SAP-System, um die Sollwerte für die Linienleistung zu übernehmen.
Auswertungen von Detaildaten wie Rüstzeiten, Störungsgründe und Ähnliches sind auf Knopfdruck verfügbar. Ausgestattet mit allen erforderlichen Funktionen für systematische Analysen und ein Shopfloormanagement bildet das System die Grundlage für schnelle zielgerichtete Analysen zur Produktionsoptimierung.
Lean-Management
Seit 2014 optimiert der Automobilzulieferer die Fertigung mit Lean-Ansätzen. Wesentliche Punkte sind die Verringerung von Durchlaufzeiten und die Erhöhungen von Anlagennutzungsgraden. Das Reportingsystem stellte dem Unternehmen im Lean-Projekt die wesentlichen Informationen zur Verfügung. Hierbei zeigte es sowohl technische Störungsgründe als auch organisatorische Themen durch gezielte Datenauswertung auf.
"Gerade in Bezug auf die Detailanalysen bei eventuell wieder auftretenden Abweichungen ist das System bei uns zu einem Standardwerkzeug für die Führungskräfte und Produktionsmitarbeiter geworden", berichtet Diepers.
"Mir war eswichtig, die Mitarbeiter nicht mit zusätzlicher Arbeit zu belasten.
Die Fehlerkommentierung sollte schnell gehen und einfach sein", übernimmt der für den SMT-Bereich Verantwortliche Andreas Schneider. Diese Anforderung erfüllt die Struktur der Bedienoberfläche.
Durch den Online-Monitor über den SMTLinien sind alle Mitarbeiter immer über den aktuellen Stand der Schicht informiert.
Das führte dazu, dass das Team aktiv an dem Projekt mitarbeitete und die Motivation für Verbesserungsvorschläge zugenommen hat.
System im Alltag
"Bei unserer Shopfloor-Managementrunde geht es überwiegend darum, wie sich die Linienausnutzungsgrade steigern lassen. Wir finden mit dem System auf einfache Weise Optimierungspotentiale und kontrollieren damit auch, ob die angesetzten Verbesserungen zum Erfolg führen" erklärt Schneider. Gerade aber auch kleinere Produktionsunterbrechungen, welche in der Vergangenheit nicht dokumentiert wurden, ließen sich mit Hilfe des Linealyzers ermitteln. So fiel zum Beispiel einmal auf, dass an einer der Linien sporadisch gegen Mitternacht eine durch die Reflow-Lötanlage verursachte Unterbrechung entstand. Die Produktionsunterbrechung dauerte bis zu fünf Minuten.
Als Ursache kommentierten die Kollegen der Nachtschicht eine nicht ausreichende Stickstoffversorgung. Ein umge-hend angesetztes ein Team zur Fehleranalyse konnte innerhalb weniger Tage die Ursache beheben. Mit dem Linealyzer ließ sich nachfolgend einfach dokumentieren, ob der Fehler wieder auftrat beziehungsweise, ob die durchgeführten Maßnahmen die gewünschte Wirkung zeigten.
Störgrößen aufdecken
An allen Arbeitsplätzen befindet sich ein Cockpit, das immer den Status der einzelnen Anlage aufzeigt. Dabei handelt es sich um die gleichen Informationen, die direkt an der Anlage den Mitarbeitern auf dem Online-Monitor zur Verfügung stehen. Damit unterstützt das System sowohl das Management als auch die Mitarbeiter in der Produktion. "Wir brauchen heute nicht mehr zu diskutieren, ob ein Problem tatsächlich existiert, das System teilt es uns als Tatsache mit", freut sich Schneider, "Wir verwenden unsere Energie darauf, die erforderlichen Dinge systematisch anzugehen und nachhaltig zu lösen." Das System hilft dabei, unbekannte Störgrößen aufzudecken und Verbesserungspotenziale zu ermitteln. Durch die Eliminierung der Stillstandzeiten, erreichte das Unternehmen bereits eine Steigerung der Liniennutzungsrade um 26 Prozent.
Seit der Schichtbericht auf dem Linealyzer läuft, arbeiten der ganze Bereich zudem papierlos. Die Informationen sind digital abgelegt, mit schneller Zugriffsmöglichkeit.
Für die Mitarbeiter bedeutet dies eine zeitliche Entlastung, da nur noch Kommentare für außergewöhnliche Ereignisse zu berichten sind. Dabei hat Promatix den Bericht exakt nach den Angaben des Automobilzulieferers umgesetzt.
Auch beim Umrüsten erweist sich das Reportingsystem als hilfreich. Bedingt durch die Auftragsstruktur sind bei Helkabo pro Schicht manchmal mehrere Rüstvorgänge erforderlich. Während des Rüstvorgangs zeigt der Online-Monitor die Linie in gelber Farbe an, so dass der Status "Rüsten" erkennbar ist. Ein Hauptansatz im Lean-Projekt war die drastisch Verkürzung dieser Rüstzeit. Linealyzer zeigt die Rüstzeit an und zeichnet sie automatisch auf, was die Ermittlung realer Rüstzeiten erlaubt. Außerdem lässt sich unmittelbar nachhalten, ob Bemühungen um eine Rüstoptimierung erfolgreich waren. Wiederholte Rüstzeitanalysen zwischen der theoretisch ermittelten und realen Rüstzeit sind problemlos durchführbar.
"Wenn etwas nicht wie geplant klappt und eine Kennzahl vom Plan abweicht, wollen wir wissen warum, dafür haben wir das System", erklärt Schneider. Um auch von unterwegs jederzeit den Überblick zu behalten, liefert ihm die Cockpitfunktion alle wesentlichen Informationen auf einem Bildschirm, den er über ein Smartphone einsehen kann.
Autor: Hubert Schönle
Geschäftsführer von Promatix
Promatix GmbH
Uhlmannstrasse 45
88471 Laupheim
Telefon: +49 (7392) 70916-38
http://www.promatix.de
Geschäftsführer
Telefon: +49 (7392) 709-1638
E-Mail: hubert.schoenle@promatix.de
Industrie 4.0
Dass sich diese Institutionen Gedanken um die Zukunft unseres Industriestandortes machen, ist sehr zu begrüßen, und die öffentliche Auseinandersetzung mit dem Thema Industrie 4.0 ebenso.
Was ist heute schon möglich?
Die Entwicklung der IK-Technologien hat mit immer kürzer werdenden Innovationszyklen rasant an Tempo zugenommen. Dabei wurde der Bedienkomfort der Systeme spürbar erhöht, so dass moderne Smartphones heute zum Standard von Jedermann gehören, privat und in der Freizeit.
Festzuhalten ist ebenso die Tatsache, dass in den meisten produzierenden Unternehmen die heute bereits verfügbaren Module aus dem Bereich Industrie 4.0 noch nicht oder nur teilweise eingesetzt werden. Da diese technischen Möglichkeiten nicht erst seit gestern existieren, sondern schon mehrere Jahre, scheinen die Gründe tiefer zu liegen und vielschichtiger zu sein.
Die technische Möglichkeit des Datentausches zwischen Produkt und Maschine und der Kommunikation von Maschine zu Maschine besteht schon seit vielen Jahren. Diese Möglichkeit wird auch partiell genutzt, an Stellen, wo es als „sinnvoll“ erachtet wird.
Da stellt sich nun die Frage nach dem Sinn?
Sinn in der Betriebswirtschaft machen nur solche Entscheidungen, die mittelbar oder unmittelbar einen Nutzen abbilden.
Im Produktionsumfeld heißt dies, die Investition bringt unmittelbar einen ROI innerhalb von 6 – 12 Monaten, oder einen Zugewinn in der Produktqualität oder in der Arbeitssicherheit.
Werden diese Bedingungen nicht erfüllt, erfolgt keine Investition!
Eine echte Hürde bei der Einführung von Industrie 4.0 Projekten wird also der Nachweis der Wirtschaftlichkeit sein. Selbst unter der Annahme, eine einheitliche Datenwelt sei durch die Entwicklung einheitlicher Schnittstellen wie Industrie 4.0 (im Werden) oder MTConnect gegeben, besteht immer noch die Problematik des existierenden und bewährten Anlagenparks, der noch nicht über neue Steuerungstechnik verfügt, dafür aber abgeschrieben ist, und ordentlich für Rendite sorgt.
Das Vorhandensein einheitlicher Datenschnittstellen und der erforderlichen Infrastruktur wird eine Einführung von Industrie 4.0 in den Fabriken sicher erleichtern, und auch auf der Kostenseite etwas für Entspannung sorgen. Ob damit auch die Motivation der Entscheidungsträger im Produktionsbereich steigt, bleibt abzuwarten.
Den Kollegen wurde in den vergangenen Jahren bei unzähligen „Lean Projekten“ vermittelt, die Dinge übersichtlich und einfach zu gestalten, KISS, und möglichst auf den Einsatz von IKT zu verzichten.
Im ganzheitlichen Einsatz von IKT auf der Shopfloor Ebene wird deshalb hier fälschlicherweise eher eine Gefahr als ein Nutzen gesehen, insbesondere, wenn es darum geht, funktionierende Produktionsanlagen in die Hände der „Informatik“ – hier der internen oder externen IT Abteilung zu legen!.
Nur kontinuierliche Überzeugungsarbeit kann hier Abhilfe schaffen.
Auch in der Kommunikation bezüglich des Themas Industrie 4.0 sollte stärker auf die Wirklichkeit eingegangen werden. Was in einem Labor wunderbar sich anwenden lässt, ist noch lange nicht für jeden Produktionsbetrieb sinnvoll, selbst bei extremen Wohlwollen.
Es gibt sicher viele Zwischenstufen, die heute schon einen ROI innerhalb 6 Monaten bringen, und die Rentabilität und die Wettbewerbsfähigkeit der Unternehmen stärkt.
Eine Herausforderung für die Einführung von Industrie 4.0 wird darin bestehen, den bereits existierenden Anlagenpark mit zu integrieren. Anlagen mit unterschiedlichem Baujahr und von verschiedenen Lieferanten gebaut, sollen steuerungstechnisch und datentechnisch so nachgerüstet werden, dass eine Produktion gemäß Industrie 4.0 möglich ist.
Ein solches Anliegen lässt sich allerdings wirtschaftlich nicht darstellen, und würde außerdem einen Anlagenausfall von mehreren Wochen nach sich ziehen.
Es bedarf also einer Lösung, die den erreichten Status an den Anlagen nicht gefährdet, sich wirtschaftlich darstellen lässt und schließlich die Vorteile aus Industrie 4.0 bietet, dies bei einem heterogenen Anlagenpark.
Moderne Produktionsmaschinen bieten heute schon eine unüberschaubare Menge an Daten, mit denen im Allgemeinen keiner etwas anzufangen weiß, mit Ausnahme dem Servicetechniker und der Programmierer des Herstellers.
Die Herausforderung heute besteht also darin, die Elemente aus Industrie 4.0 unmittelbar einzusetzen, die einen echten Kostenvorteil in Form von Produktivitätssteigerungen oder Flexibilitätssteigerung bringen.
Dieser Herausforderung entspricht zum Beispiel das Shop Floor Management System „Linealyzer“ von Promatix. Dieses System ist universell einsetzbar, da es keine Schnittstellen zu der Anlagensoftware benötigt, und ist schrittweise skalierbar bis zu einer Industrie 4.0 Funktionalität, immer mit dem Fokus auf den ROI der Kunden.
Dabei versteht sich das System als Unterstützung für den Mitarbeiter und das Management in der Produktion! Der Nutzen ist unmittelbar vorhanden, und für zukünftige Entwicklungen sind die Grundsteine gelegt.
Promatix GmbH
Uhlmannstrasse 45
88471 Laupheim
Telefon: +49 (7392) 70916-38
http://www.promatix.de
Geschäftsführer
Telefon: +49 (7392) 709-1638
E-Mail: hubert.schoenle@promatix.de