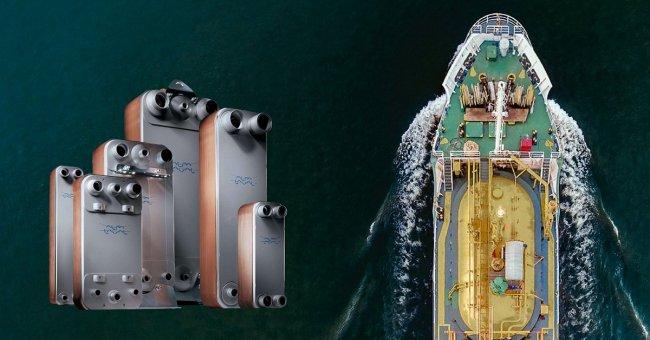
Critical Manufacturing MES zur Förderung des intelligenten Fertigungsprogramms von Alfa Laval
Alfa Laval ist ein hoch innovatives Unternehmen, das im Rahmen seines Smart-Manufacturing-Programms erhebliche Investitionen in Industrie 4.0-Projekte getätigt hat. Das Unternehmen hat sich für das moderne Critical Manufacturing MES (Manufacturing Execution Systems) entschieden, mit dem Ziel, Effizienz zu steigern, Qualität zu verbessern und große Datenmengen in den Bereichen IoT, Produkte und Produktionsprozesse effektiver zu erheben und zu analysieren, um so kontinuierliche Verbesserungen (CI) zu erreichen.
Die MES-Implementierung wird mit einer Hauptmodellinstallation eingeleitet, welche sämtliche Funktionen sowie Anforderungen aus verschiedenen Standorten der Alfa Laval Gruppe abdeckt. Das System wird zunächst an einem Pilot-Standort in Eskilstuna, Schweden, eingeführt, wobei der gesamte Anwendungsbereich der MES-Lösung jedoch Fabriken auf der ganzen Welt umfassen wird.
Augusto Vilarinho, Business Development Director bei Critical Manufacturing, sagt: „Alfa Laval verfolgt einen Ansatz zur intelligenten Fertigung, für dessen Begleitung die Critical Manufacturing MES-Lösung ursprünglich ausgelegt war. Unser modernes MES ist modular und erweiterbar aufgebaut. Es bietet eine Plattform, welche bereits bestehende sowie neue Maschinen integriert und sich an die aktuellen und zukünftigen Bedürfnisse der einzelnen Fabriken entsprechend anpasst."
So erreichen die Teammitglieder mithilfe von MES eine vollständige Transparenz der Arbeitsabläufe und einen einfachen Zugang zu Echtzeitdaten. Vilarinho fügt hinzu: „Alfa Laval ist ein echter Weltmarktführer. Dieses Projekt ist für uns ausgesprochen wichtig. Wir freuen uns darauf, gemeinsam mit ihnen an ihren Zielen für intelligente Fertigung zu arbeiten und sie dabei zu unterstützen, einen zukünftigen Fertigungsstand zu erreichen, der neue Standards hinsichtlich Qualität und Effizienz setzt."
Critical Manufacturing bietet innovative Softwaretechnologie und Dienstleistungen zum Betrieb der modernsten Fertigungen weltweit. Das Manufacturing Execution System (MES) der neuesten Generation steht im Zentrum von Industrie 4.0 durch die weitreichenden Möglichkeiten zur Integration, Mobile Anwendung, Konnektivität sowie logischer Dezentralisation. Das umfassende und durchgängige System erhöht die Performance, Kontrolle und Qualität in komplexen Fertigungsorganisationen.
Das Unternehmen ist Teil der Critical Group, einer 1998 gegründeten private Firmengruppe, die IT-Lösungen für geschäftskritische Anwendungen anbietet.
Für mehr Informationen besuchen Sie unsere Website www.criticalmanufacturing.de oder kontaktieren Sie uns unter kontakt@criticalmanufacturing.de.
Critical Manufacturing Deutschland GmbH
Maria-Reiche-Str. 1
01109 Dresden
Telefon: +49 (351) 4188-0639
Telefax: +49 (35205) 120020
http://www.criticalmanufacturing.de
Managing Director / Geschäftsführer
Telefon: +49 (351) 41880639
E-Mail: Tom.Bednarz@criticalmanufacturing.de
Media Contact
Telefon: +351 (229) 446-927
E-Mail: anna.zieba@criticalmanufacturing.com
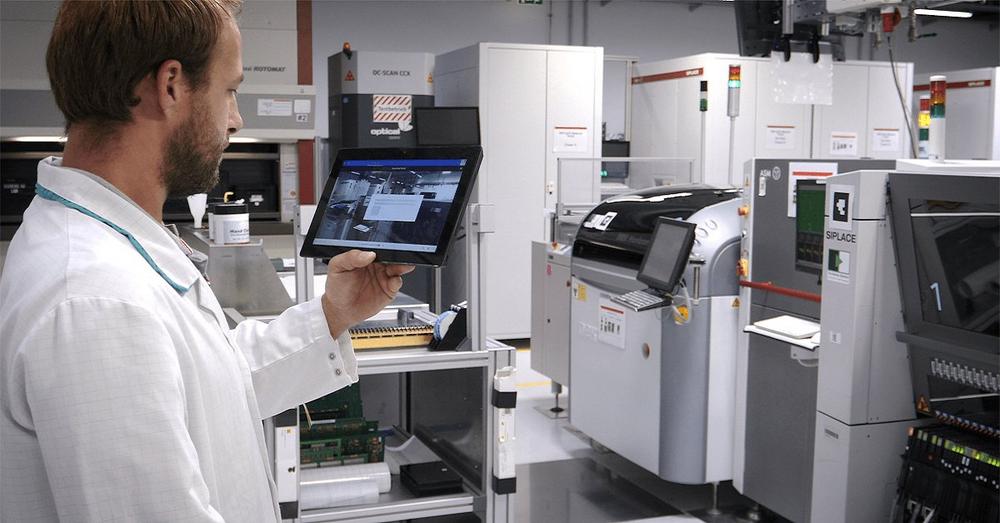
Digital Twin und Augmented Reality: Von der Idee zur Umsetzung mit MES
ZUNÄCHST EINMAL DIE GRUNDLAGEN: DIGITAL TWIN UND AUGMENTED REALITY
Digital Twin oder der digitale Zwilling ist eine digitale Nachbildung einer physischen Einheit, z.B. einer Fertigungslinie oder einer einzelnen Verarbeitungsanlage. In der Fertigung umfasst sie verschiedene Modelle und Daten über das Produkt, die Wirtschaftsgüter, die Produktionslinie oder die Fabrik. Anhand von IIoT-Daten ist es möglich, das virtuelle Modell auf der Grundlage der Ereignisse im realen (physischen) System in Echtzeit zu aktualisieren.
Augmented Reality (AR) bietet eine interaktive Darstellung einer realen Umgebung, in der Objekte, die sich in der realen Welt befinden, durch computergenerierte Informationen einschließlich der sensorischen, auditiven und olfaktorischen Eindrücke ergänzt werden. Ähnlich wie bei einem digitalen Zwilling und wie in der Abbildung unten zu sehen ist, bilden die physische und virtuelle Welten ein Kontinuum.
Schauen wir uns nun das Zusammenspiel dieser Technologien an. Augmented Reality schafft eine Verbindung zwischen der physischen Welt einer Fabrik und ihrem virtuellen Abbild – Digital Twin – indem es einen Einblick in die beiden Komponenten ermöglicht, die mit Daten aus den tatsächlichen Prozessen ergänzt werden, um so die Entscheidungsfindung und das Wissensmanagement zu optimieren.
Darüber hinaus muss eine weitere Komponente betrachtet werden: Digital Thread oder der digitale Faden. Ein Digital Thread beschreibt den Handlungsrahmen, der Datenflüsse verbindet und eine holistische Darstellung der Daten eines Assets / Betriebsmittels über seinen gesamten Produktlebenszyklus ermöglicht. Dieses Framework umfasst Protokolle, Sicherheitsaspekte und Normen. Digital Thread verknüpft digitale Zwillinge, digitale Modelle von physischen Objekten oder Gruppen von Objekten. Alle ausgehenden Datenströme, die den digitalen sowie den physischen Aspekt eines Prozesses betreffen, werden dabei zu einem digitalen Faden zusammengefasst. Dieser Digital Thread ist ein wichtiger Bestandteil der horizontalen und vertikalen Integration von Industrie 4.0 zwischen verschiedenen Systemen und Disziplinen.
DER MES-GESTÜTZTE DIGITALE ZWILLING
Die digitalen Zwillinge und MES (Manufacturing Execution Systems) sind aufgrund ihrer Struktur sehr eng miteinander verknüpft. Wir sind der Meinung, dass das MES den eigentlichen digitalen Zwilling der Fabrik darstellt. Betrachtet man solche MES-Funktionen wie die Bereitstellung eines Fabrikmodells, die Datendefinitionen, die Abbildung der Produktionsprozesse (physisch und virtuell) und die Nutzung der Daten für die Status- und Entscheidungsfindung, so entspricht das MES-Kernstück der Funktionalität eines digitalen Zwillings.
Schauen wir uns die zentralen MES-Funktionen an, um zu verstehen, was genau das MES zu einem Digital-Twin-Tool macht:
- Erfassung und Speicherung von Daten, um die vollständige Synchronisierung der virtuellen (Digital Twin) und der realen Welt einfach und inhärent zu realisieren
- Verarbeitung von Datenströmen, die von allen angeschlossenen Geräten, einschließlich IIoT, empfangen werden
- Abgleich der eingehenden Daten mit den im Modell gespeicherten Standards, sodass sichergestellt ist, dass Fehlerschutz, Warnungen und Alarme ggf. ausgegeben werden
Die neueren MES-Versionen – Augmented MES – verfügen über einen digitalen Zwilling zur Visualisierung der Statusinformationen. Darüber hinaus setzen sie moderne Sensoren (IIoT, RFID, Scanner) ein, um Aktualisierungen bezüglich Materialien, Maschinen, Werkzeugen, Personal und Transportsystemen vorzunehmen. Sie koordinieren und aktualisieren das Modell mit dem Ziel den aktuellen Stand abzubilden.
Dank moderner MES können Sie vorhandene Baupläne (Blueprints) und CAD-Modelle von Geräten sowie ortsgebundene Dienste nutzen. So können Daten schnell geladen, Elemente bzw. Maschinen in den virtuellen Räumen positioniert und Ergebnisse visualisiert werden, sodass sowohl Sie als auch Ihre Mitarbeiter davon profitieren können.
MES VERBESSERT AR
Das MES bietet bereits seit Jahren eine Anleitung für Anwender und Techniker in Form von Arbeitsanweisungen auf den Bildschirmen. Diese Funktion gilt als ein wichtiges Element der Bedienerschnittstelle. Mit dem Aufschwung der AR-Technologie liefert das MES eine optimierte Benutzerfreundlichkeit. So können Mitarbeiter, die AR- oder intelligente Brillen, Mobiltelefone, Tablets und andere digitale Geräte einsetzen, entscheidende Prozessinformationen einblenden lassen.
Beispielsweise kann ein Mitarbeiter die AR-Brille zur Visualisierung einer Verarbeitungsanlage verwenden. Das MES zeigt dabei Mengen, Prüfergebnisse, Arbeitsanweisungen, Genealogie oder historische Aufzeichnungen an. Auch der Maschinenstatus oder die Wartungsinformationen, wie MTBF oder MTTR, können eingeblendet werden. Dafür muss für jede Ressource im MES mithilfe von AR-Identifikatoren festgelegt werden, welche Daten in welcher Reihenfolge anzuzeigen sind.
Der Einsatz von AR ist in den meisten Arbeitsbereichen der Fabrik möglich. SOPs, Checklisten, WIP und KPIs zur Information über Qualität, Durchsatz und Verfügbarkeit können von Betriebs- und zur Wartungsteams abgerufen werden. Eine interaktive Arbeitsanleitung dient dem Fehlerschutz bei den durchgeführten Arbeiten. Die Nachverfolgung von Materialien je Behälter – Mengen, Seriennummern und Verfallsdaten – trägt zur Verbesserung der Abläufe im Betrieb, Versand und Kundendienst bei. Den Möglichkeiten sind keine Grenzen gesetzt!
AUGMENTED MES IST SCHON HEUTE REALITÄT!
Wir haben bereits darüber gesprochen, wie ein modernes MES anhand von Digital Twin und AR die Produktivität erhöhen und Verbesserungen vorantreiben kann. Hierbei handelt es sich nicht um theoretische Beispiele, denn bereits heute sind kommerzielle Versionen solcher MES-Suiten erhältlich. Diese Systeme — wir nennen sie Augmented MES — wurden speziell dafür entwickelt, um Industrie 4.0 und die damit einhergehenden digitalen Technologien umzusetzen.
Mit Augmented MES können Sie den digitalen Zwilling der Fabrik erkunden, weiterentwickeln und optimieren sowie den Einsatz von AR in Ihrer Fabrik fördern. Doch längst nicht alle MES bieten solche Möglichkeiten! Viele aktuelle MES-Produkte verfügen weder über die Breite der Anwendungen noch über die zusätzlichen Funktionalitäten zur Umsetzung von Industrie 4.0, IIoT, Digital Twin und AR.
Treffen Sie also eine sorgfältige Auswahl und genießen Sie alle gewonnenen Vorteile, sobald Sie sich für ein Augmented MES entschieden haben. Augmented MES treibt deutlich und zeitnah den Fortschritt eines Unternehmens auf dem Weg zur Industrie 4.0 voran. Es bietet Ihnen die Grundlage für den Einsatz von solchen Zukunftstechnologien wie Digital Twin, AR und IIoT. Außerdem stellt es eine Datenplattform für kontinuierliche Verbesserungen der betrieblichen Abläufe und der Leistungsfähigkeit bereit – die Eckpfeiler zur Umsetzung von Industrie 4.0.
Der vorliegende Beitrag ist ein Auszug aus unserem Whitepaper Digital Twin and Augmented Reality: From Ideal to Real with MES. Das vollständige Whitepaper lesen Sie hier.
Critical Manufacturing bietet innovative Softwaretechnologie und Dienstleistungen zum Betrieb der modernsten Fertigungen weltweit. Das Manufacturing Execution System (MES) der neuesten Generation steht im Zentrum von Industrie 4.0 durch die weitreichenden Möglichkeiten zur Integration, Mobile Anwendung, Konnektivität sowie logischer Dezentralisation. Das umfassende und durchgängige System erhöht die Performance, Kontrolle und Qualität in komplexen Fertigungsorganisationen.
Das Unternehmen ist Teil der Critical Group, einer 1998 gegründeten private Firmengruppe, die IT-Lösungen für geschäftskritische Anwendungen anbietet.
Für mehr Informationen besuchen Sie unsere Website www.criticalmanufacturing.de oder kontaktieren Sie uns unter kontakt@criticalmanufacturing.de.
Critical Manufacturing Deutschland GmbH
Maria-Reiche-Str. 1
01109 Dresden
Telefon: +49 (351) 4188-0639
Telefax: +49 (35205) 120020
http://www.criticalmanufacturing.de
Managing Director / Geschäftsführer
Telefon: +49 (351) 41880639
E-Mail: Tom.Bednarz@criticalmanufacturing.de
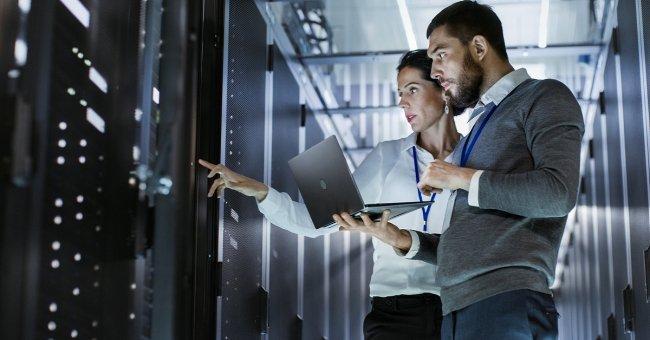
APS als native Komponente im MES für Industrie 4.0
DAS WICHTIGSTE ZUERST. WAS IST EIN APS?
Laut Gartner ist „Advanced Planning and Scheduling (APS) eine Teilkomponente der Supply-Chain-Planung und dient der kontextspezifischen Darstellung der Fertigungsplanung und -terminierung“.
Das APS ist aufgrund seiner Spezifität und der Ausrichtung auf das Ressourcen- und Materialmanagement üblicherweise eine Einzelanwendung. Sein Schwerpunkt liegt auf einem ausgewogenen Zusammenspiel von Produktivität, Kundenzufriedenheit und Wirtschaftlichkeit. Der Schwerpunkt im MES liegt auf der Umwandlung von Rohmaterialien in Fertigerzeugnisse. Beide Anwendungen weisen eine gewisse Ähnlichkeit auf, da sie das gleiche Ziel der Optimierung von Fabrikproduktivität und Material mithilfe von Fertigungsplanung und -ausführung verfolgen. So gehen die Vorteile einer synchronisierten, zentralen Übersicht über alle Informationen im MES durch den Einsatz eines isolierten, nicht integrierten APS verloren. Zum Ausschöpfen der vollen APS-Leistung ist eine einfache Integration nicht ausreichend, es muss vielmehr als ein natives MES-Modul eingesetzt werden.
NATIVE APS-FUNKTIONALITÄT IM MES
Was bedeutet das konkret? Im Prinzip bedeutet das, dass das APS auf dem gleichen Framework wie das MES basiert. Es verwendet, wie alle anderen MES-Module auch, die gleichen Stammdaten und Benutzeroberflächen (GUI), ohne zusätzlichen Arbeitsaufwand seitens der IT- oder Fertigungsteams im Unternehmen.
Ein Blick auf den Datenfluss im Diagramm oben zeigt, welche Daten für das APS aus dem MES und vice versa idealerweise benötigt werden. Die Automatisierung und Integration dieser Datenströme sorgt für schnellere Arbeitsabläufe und ermöglicht somit einen reaktionsschnelleren Betrieb. Und das ist der entscheidende Vorteil der zusätzlichen nativen APS-Funktionalität im MES.
WAS GESCHIEHT, WENN EINE VERBINDUNG ZWISCHEN APS UND MES NICHT NATIV IST?
Die native APS-Funktionalität im MES ist in der Praxis eher selten. Die meisten Terminierungs-Tools sind in diesen Varianten verfügbar:
1. Die bestmögliche Lösung (engl. Best-in-breed): Ein unabhängiges System.
2. Enthalten im ERP: Zu den Schwachpunkten gehören die Abwicklung komplexer Vorgänge und eine zusätzliche Integration, da die meisten ERP-Systemanbieter ihre APS dazugekauft und nicht selbst entwickelt haben.
3. Erweiterung durch Lösungen externer Anbieter: Ähnlich wie beim ersten Punkt schließen sich mehrere MES-Unternehmen mit einem APS-Partner zusammen, um eine breitere Funktionalität zu erreichen. Die Integration erfolgt nur oberflächlich, da keine Stammdaten geteilt werden und das System für eine unabhängige Anwendung vorgesehen ist.
4. Ein Unternehmen, unterschiedliche Systeme: Wie beim Zusatzprodukt unter Punkt 3 bietet diese Variante eine zentrale Quelle für das MES und APS, in der Praxis handelt es sich dabei jedoch um unabhängige Anwendungen mit geringer bis gar keiner Integration.
Den kompletten Artikel zu diesem Thema lesen Sie hier.
Critical Manufacturing bietet innovative Softwaretechnologie und Dienstleistungen zum Betrieb der modernsten Fertigungen weltweit. Das Manufacturing Execution System (MES) der neuesten Generation steht im Zentrum von Industrie 4.0 durch die weitreichenden Möglichkeiten zur Integration, Mobile Anwendung, Konnektivität sowie logischer Dezentralisation. Das umfassende und durchgängige System erhöht die Performance, Kontrolle und Qualität in komplexen Fertigungsorganisationen.
Das Unternehmen ist Teil der Critical Group, einer 1998 gegründeten private Firmengruppe, die IT-Lösungen für geschäftskritische Anwendungen anbietet.
Für mehr Informationen besuchen Sie unsere Website www.criticalmanufacturing.de oder kontaktieren Sie uns unter kontakt@criticalmanufacturing.de.
Critical Manufacturing Deutschland GmbH
Maria-Reiche-Str. 1
01109 Dresden
Telefon: +49 (351) 4188-0639
Telefax: +49 (35205) 120020
http://www.criticalmanufacturing.de
Managing Director / Geschäftsführer
Telefon: +49 (351) 41880639
E-Mail: Tom.Bednarz@criticalmanufacturing.de
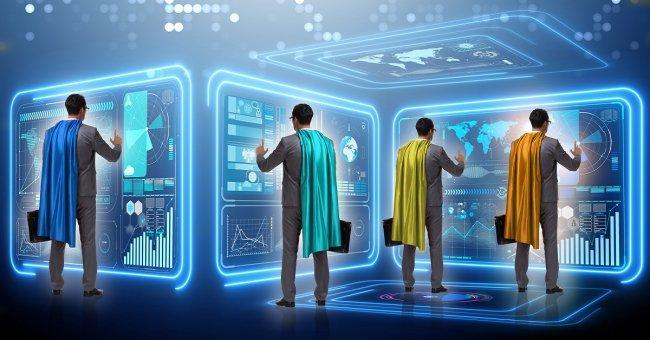
Die vier analytischen Helden im Kampf um Effizienz
Advanced Analytics umfasst dabei Descriptive, Diagnostic, Predictive und Prescriptive Analytics.
So kann man verstehen, was geschehen ist (deskriptiv), warum es geschehen ist (diagnostisch), was geschehen wird (prädiktiv) und welche Maßnahmen ergriffen werden sollten (präskriptiv). Dank diesen vier Informationshelden kann die Effizienz der Fertigung deutlich verbessert, die Verarbeitungsfehler vermieden, der Ausschuss und die Nacharbeit reduziert und die Qualität erhöht werden.
Diese Analysewerkzeuge können so eingerichtet werden, dass sie praktisch alle Aufgaben in einem Fertigungsbetrieb übernehmen können. So können Muster identifiziert, Zusammenhänge zwischen Ursachen und Folgen ermittelt und komplexe Vorgänge simuliert werden. Bei ausreichender Datenmenge können Lernalgorithmen verwendet werden, um eine Annäherung an eine beliebige Funktion in der Fertigung zu ermöglichen. Moderne Manufacturing Execution Systems (MES) sammeln, verknüpfen, kontextualisieren und analysieren Daten in der gesamten Lieferkette. Die leistungsstarken Analysemöglichkeiten dieser Systeme, die als „Single Source of Truth“ fungieren, ermöglichen eine schnelle Datenanalyse, um neue Wege zur Effizienzsteigerung im Produktionsprozess zu finden. Je schneller die Daten verstanden werden, desto agiler ist ein Prozess – so kann mit jeder eingesparten Sekunde im Endeffekt Geld gespart werden.
DIE ANALYSE-ARTEN VERSTEHEN
Die deskriptive Analyse ist im Allgemeinen die Vorstufe von Analytics. Dabei werden Daten aggregiert und zusammengefasst, um Aufschluss über die Vorgänge im Fertigungsprozess zu erhalten. Anhand historischer Daten werden Vergleiche durchgeführt und ein Überblick über die aufgetretenen Änderungen verschafft. Die Ergebnisse dieser deskriptiven Analyse können in Berichten und Dashboards zusammengefasst werden, um ein klares Bild von Trends und Anomalien zu vermitteln.
Erfahren Sie mehr zu diesem Thema hier.
Critical Manufacturing bietet innovative Softwaretechnologie und Dienstleistungen zum Betrieb der modernsten Fertigungen weltweit. Das Manufacturing Execution System (MES) der neuesten Generation steht im Zentrum von Industrie 4.0 durch die weitreichenden Möglichkeiten zur Integration, Mobile Anwendung, Konnektivität sowie logischer Dezentralisation. Das umfassende und durchgängige System erhöht die Performance, Kontrolle und Qualität in komplexen Fertigungsorganisationen.
Das Unternehmen ist Teil der Critical Group, einer 1998 gegründeten private Firmengruppe, die IT-Lösungen für geschäftskritische Anwendungen anbietet.
Für mehr Informationen besuchen Sie unsere Website www.criticalmanufacturing.de oder kontaktieren Sie uns unter kontakt@criticalmanufacturing.de.
Critical Manufacturing Deutschland GmbH
Maria-Reiche-Str. 1
01109 Dresden
Telefon: +49 (351) 4188-0639
Telefax: +49 (35205) 120020
http://www.criticalmanufacturing.de
Managing Director / Geschäftsführer
Telefon: +49 (351) 41880639
E-Mail: Tom.Bednarz@criticalmanufacturing.de
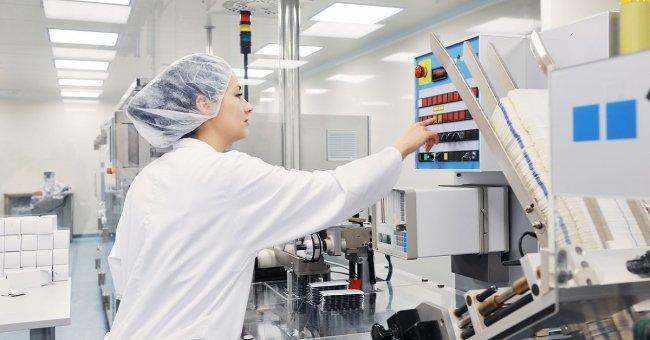
10 Gründe, warum ein MES für Ihr Qualitätsmanagement unverzichtbar ist
– Dr. W. Edwards Deming
Dr. Deming gilt als Vater des PDCA-Zyklus (Plan, Do Check, Act), der im Rahmen der Qualitätssicherungsprozesse in der alltäglichen Fertigungspraxis verwendet wird. Die holistische Betrachtung des gesamten Fertigungsprozesses inkl. der Anwendung des genannten PDCA-Zyklus ist der Schlüssel zum Aufbau einer widerstandsfähigen Fertigung.
HINTERGRUND
Die Medizinproduktebranche war bis vor kurzem „unantastbar“ hinsichtlich des Konjunkturrückgangs, denn mit dem zunehmenden Alter der Bevölkerung sind mehr Behandlungsmethoden und -verfahren erforderlich, um eine gute Allgemeingesundheit zu erhalten. Die Wachstumsraten dieser Branche liegen traditionell im Bereich zwischen 5% (reine Geräte) und 30% (Internet der medizinischen Dinge). Die Auswirkungen von COVID-19 sind nun spürbar: Verfügen Unternehmen nicht über Technologien zur Erkennung, Behandlung oder Überwachung der Erkrankung, so schwanken ihre Einnahmen stark. Diese Unterbrechung im „business as usual“ aufgrund der Pandemie kann im Nachhinein von Vorteil sein. In einem Artikel von McKinsey – Unternehmens- und Strategieberatungsunternehmen – heißt es: „Der Schlüssel zum Wachstum nach der Krise liegt darin, der Innovation schon heute Priorität einzuräumen.“ Und obwohl insgesamt 90% der befragten Führungskräfte dieser Aussage zustimmen, glauben nur 21%, dass sie bereit sind, sich dieser Herausforderung anzunehmen.
Was bedeutet dies für das Qualitätsmanagement? Das Qualitätsmanagement ist ein wesentlicher Bestandteil der Good Manufacturing Practice (GMP), insbesondere für solche Branchen, die einer gesetzlichen, regulatorischen Aufsicht unterliegen. So wird sichergestellt, dass die Verfahren zur Herstellung gesetzeskonformer Produkte befolgt, dokumentiert werden und nachvollziehbar sind.
Die Qualitätsmanagementsysteme (QMS) sind Standard für die meisten Unternehmen in diesen so regulierten Branchen. Die größte Herausforderung eines QMS liegt in der Tatsache, dass es häufig ein unabhängiges System mit einer reaktiven Herangehensweise an Qualitätsprobleme ist, während der Fertigungsprozess eine proaktive Herangehensweise erfordert. Wir sind der Ansicht, dass ein Manufacturing Execution System (MES) oder eine Manufacturing Operations Management (MOM)-Lösung für einen holistischen Qualitätsansatz unverzichtbar sind. Im Folgenden nennen wir zehn Gründe, warum ein MES die Grundlage Ihrer Qualitätssicherung bilden sollte.
1. QUALITÄT GEHÖRT ZUM TAGESGESCHÄFT ALLER MITARBEITER
Laut W. Edward Deming „Qualität ist die Verantwortung jedes Einzelnen“. Das bedeutet, dass jeder Mitarbeiter im Unternehmen bei der Ausführung seiner Arbeit auf Qualität bedacht sein muss. Sie muss in die allgemeine Unternehmenskultur sowie in die Fertigungsprozesse gleichsam eingebettet sein.
Ein proaktiver Ansatz im Hinblick auf die Qualitätssicherung der Betriebsprozesse ist die Zukunft der Medizinprodukteherstellung. Es wird Zeit, Probleme zu verhindern, bevor sie auftreten.
Menschliche Fehler in der Produktion werden durch automatisierte Bedienerführung auf der Basis von regelbasierten Vorgaben ausgeschlossen. Das MES erkennt Abweichungen und kann im Rahmen des CAPA-Verfahrens (Corrective Action Preventive Action) einen Nichtkonformitätsbericht (NCR) erstellen und/oder automatisch ein Qualitätsprüfprotokoll initiieren.
Der Einsatz des MES/MOM – des weitreichenden Fertigungssystems – als Hauptplattform ermöglicht eine holistische Darstellung und Erfassung der Tätigkeiten, um die Qualitätsmanagementprozesse im Fertigungsbereich abzudecken
2. INFORMATIONSFLUSS
Die Umsetzung von Qualitätsstandards ist ein komplexer Prozess. Mit der zunehmenden Komplexität und Variantenvielfalt der Produkte müssen auch die Prozesse dahinter flexibel und robust bleiben, um einen agilen Arbeitsablauf zu gewährleisten. Dieser Prozess ist naturgemäß multidisziplinär, sodass eine bereichsübergreifende Zusammenarbeit zur Aufrechterhaltung des Qualitätsniveaus erforderlich ist. So entstehen zahlreiche funktionale Teilsysteme, die jedoch oftmals noch nicht bereichsübergreifend sind.
Das ist zum Beispiel der Fall, wenn ein Produktionsmitarbeiter ein Produkt aus einem Arbeitsvorgang herausbewegt. Die erfassten Informationen umfassen technische Informationen aus den Maschinen, die daraus Echtzeit-Parameter berechnen; diese Parameter werden einem Lot in der elektronischen Datenbank zugeordnet und in einem SPC-Diagramm abgebildet. Im Falle einer festgestellten Abweichung hält das System das Lot zurück und löst einen CAPA-Prozess aus.
Diese Teilsysteme der Fertigung und des Qualitätsmanagements erfordern eine nahtlose Integration, um allen Beteiligten einen uneingeschränkten Einblick in den Prozess bieten zu können. Laut einem Bericht von Cambashi nutzen die führenden Unternehmen der Branche die MES/MOMs als eine Plattform zur Vereinheitlichung von Informationen.
Lesen Sie unseren kompletten Artikel und erfahren Sie mehr.
Critical Manufacturing bietet innovative Softwaretechnologie und Dienstleistungen zum Betrieb der modernsten Fertigungen weltweit. Das Manufacturing Execution System (MES) der neuesten Generation steht im Zentrum von Industrie 4.0 durch die weitreichenden Möglichkeiten zur Integration, Mobile Anwendung, Konnektivität sowie logischer Dezentralisation. Das umfassende und durchgängige System erhöht die Performance, Kontrolle und Qualität in komplexen Fertigungsorganisationen.
Das Unternehmen ist Teil der Critical Group, einer 1998 gegründeten private Firmengruppe, die IT-Lösungen für geschäftskritische Anwendungen anbietet.
Für mehr Informationen besuchen Sie unsere Website www.criticalmanufacturing.de oder kontaktieren Sie uns unter kontakt@criticalmanufacturing.de.
Critical Manufacturing Deutschland GmbH
Maria-Reiche-Str. 1
01109 Dresden
Telefon: +49 (351) 4188-0639
Telefax: +49 (35205) 120020
http://www.criticalmanufacturing.de
Managing Director / Geschäftsführer
Telefon: +49 (351) 41880639
E-Mail: Tom.Bednarz@criticalmanufacturing.de
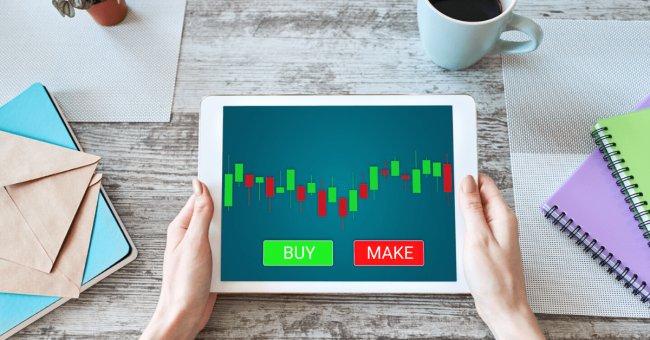
Do-It-Yourself vs. kommerzielle Lösung: 6 Gründe, warum Sie keine eigene Software entwickeln sollten
Dieses Argument ist nicht neu. Ende der 90er Jahre war ich Mitglied eines komplexen Software-Auswahlausschusses und habe damals schon vor ähnlichen Entscheidungen gestanden. Wie könnte ein kommerzielles, eher generisches Paket unseren Bedarf zu 100 Prozent mit einer Anwendung decken, die bereits zahlreiche Aktualisierungen, Entwicklungen und Verbesserungen erfahren hat? Am Ende des Auswahlprozesses wurde eine Lösung ausgewählt, die am besten „passte“ und gleichzeitig eine Plattform bot, die mit uns gemeinsam wachsen und expandieren konnte. So konnten wichtige IT-Ressourcen freigegeben werden, die für andere Geschäftszwecke effizienter eingesetzt werden konnten.
Das Gleiche gilt für Automatisierungssoftware für industrielle Anwendungen – ein Manufacturing Execution System (MES), ein Batch-Rezeptmanagementsystem oder ein Enterprise Manufacturing Intelligence (EMI)-Portal. All diese Anwendungen sind dem Abwägungsprozess „Do-It-Yourself vs. kommerzielle Lösung“ oder manchmal der „Umgestaltung“ existierender Anwendungen unterworfen. Lassen Sie uns die häufigen Überlegungen in diesem Prozess genauer betrachten und auch auf die 6 Gründe schauen, warum eine kommerzielle Lösung (Commercial Off The Shelf, COTS) langfristig betrachtet sinnvoller ist:
- „Wir verstehen unser Geschäft am besten.“ Es mag stimmen, Ihr Business und die Welt darum bleibt allerdings nicht ewig beständig – es werden neue Technologien eingesetzt, es entstehen neue Marktdynamiken oder es kommt zum Führungswechsel in einem Unternehmen. Möglicherweise sind Methoden, die vor 2 Jahren angewandt wurden, heute nicht mehr relevant. Ihre selbst entwickelte Software ist jedoch nicht geeignet, die neuen Plattformen optimal zu nutzen, um Ihre individuellen Geschäftsanforderungen umzusetzen.
- „Wir verwenden diese Software bereits seit X Jahren. Wir haben in sie investiert und sind der Meinung, dass sie zukunftsfähig ist.“ Allein die Kenntnis über das Produkt bedeutet nicht, dass es auf lange Sicht für gewisse Aufgaben geeignet ist. Wie lässt es sich mit anderen Anwendungen integrieren? Ist ihre Architektur offen für neue Technologien wie Cloud Hosting oder Mobilität? Haben Sie genügend Personal, das ausreichend qualifiziert und ausgebildet ist, um Änderungen zu integrieren? Die großen Anbieter von Unternehmenssoftware haben mehrere Millionen Dollar in die Entwicklung, Verbesserung und Wartung ihrer Anwendungen investiert. Wie erreichen Sie als Auftragsverarbeiter oder Hersteller das gleiche Maß an Engagement für eine Aufgabe, die nicht zum strategischen Bestandteil Ihres Gesamtgeschäfts gehört?
- „Wir verfügen über notwendige Branchenerfahrung.“ Sicherlich kennen Sie sich z.B. mit der Elektronikfertigung, der Herstellung medizinischer Geräte oder anderen Herstellungsverfahren aus. Dennoch gibt es immer Anbieter, welche umfangreiche Erfahrungen in Ihrem Segment haben, die aus der Zusammenarbeit mit einer Vielzahl ähnlicher Unternehmen resultieren. Die Herstellungsverfahren oder -stile können zudem auf einer bestimmten Abstraktionsebene in verschiedene Kategorien eingeteilt werden, sodass die zugehörigen Lösungsanbieter eine große Bandbreite und/oder Spezialkenntnisse für bestimmte Kategorien abdecken. So wurden Prozesse im Gartner-Bericht Critical Capabilities for MES in Continuous, Batch/Repetitive Flow und Complex Discrete sowie in Make to Order, Engineering to Order oder Make to Stock unterteilt. Im Anschluss wurde die Fähigkeit der einzelnen Softwareanbieter bewertet, die Anforderungen der einzelnen Prozesse abzudecken. Die entstandene Matrix ermöglicht es den Unternehmen, die einzelnen Anbieter hinsichtlich ihrer wichtigsten Anwendungsfälle unter gleichwertigen Rahmenbedingungen einfach zu bewerten.
- „Es ist viel billiger, es intern zu bauen.“ Dieses Argument, das interne Kosten nicht als Kosten einstuft, ist ein großer Irrtum. Das stimmt nicht. Selbst wenn genügend interne Kapazitäten vorhanden sind, sind die Opportunitätskosten zu berücksichtigen – wo könnten diese Ressourcen eingesetzt werden, um den größtmöglichen Ertrag zu erzielen? Da die Größenvorteile, die sich aus der Zusammenarbeit mit verschiedenen Kunden und Projekten ergeben, für Ihr Unternehmen entfallen, müssen Sie folgendes bedenken: Interne Entwicklungen sind am Ende 2- bis 20-mal teurer als der Erwerb einer bereits existierenden Lösung auf dem Markt.
- Sie sind keine Software-Firma! Die meisten Unternehmen, die über ältere Systeme verfügen, verspüren ein starkes Gemeinschafts- und Erfolgsgefühl, wenn eine Anwendung, die ihren Anforderungen entspricht, entwickelt und aufrechterhalten wird. Das ändert sich allerdings. Ihre Bedürfnisse sind heute möglicherweise ganz andere als zum Zeitpunkt des Entwicklungsprozesses. Kann man es sich leisten, weiterhin in eine Anwendung zu investieren, die zu einem gegebenen Zeitpunkt zu 100 Prozent ausgereicht hat, die aber angesichts der Entwicklungen des Marktes, der Technologien oder der veränderten Anforderungen im Unternehmen inzwischen unzureichend ist? Keine Softwarefirma zu sein bedeutet schlicht, dass man nicht den Fokus, die Investitionen, die Technologie und die Fachkompetenz mitbringt, um die Partnerschaften, die Vision und vor allem die Ressourcen für die Produktentwicklung, welche für die Nachhaltigkeit erforderlich sind, bestmöglich zu nutzen. Die klassischen Softwareunternehmen kooperieren mit ihren Kunden, sodass die Kundenbedürfnisse auch längerfristig erfüllt werden und so eine nachhaltige Zukunftsplattform entsteht.
- Vision und Strategie. Wo bewegt sich der Softwaremarkt hin? Von welchen neuen Technologien profitieren Sie als Hersteller? Wie können große Datenmengen, Analysen, IoT und KI (Künstliche Intelligenz) innerhalb Ihres Unternehmens effizient eingesetzt werden? Ein Unternehmen, das sich ausschließlich auf Fertigungssoftware und die aktuellen und zukünftigen Anforderungen dieser Branche spezialisiert hat, kann diese Technologien organisch in Ihr Unternehmen integrieren. Auch ein Netzwerk von externen Partnern für Beratung, Konzeption, Implementierung und Support ist somit gegeben. Diese Unternehmen übernehmen für Sie die Qualifizierung und das Training dieser externen Partner, sodass sie ergänzend zum jeweiligen Software-Anbieter agieren können.
LETZTER DISKUSSIONSPUNKT
Wir setzen unsere Lösung in Fabriken ein, die über kein MES verfügen oder in welchen das bestehende MES ersetzt werden soll. Unsere Erfahrung zeigt, die Mehrheit derjenigen, die solche MES-Projekte durchführen, versucht die selbst entwickelten Lösungen zu ersetzen, weil sie den aktuellen Geschäftsanforderungen nicht mehr gerecht werden oder nie gerecht waren.
Es scheint verlockend, eigene Fachleute heranzuziehen und ihr Wissen in maßgeschneiderten Tools und Anwendungen abzubilden. Dennoch bindet man sich langfristig an Anwendungen, die nur für einen bestimmten Zeitraum in Ihrem Unternehmen anwendbar sind. Der Erwerb eines kommerziellen Softwareprodukts stellt sicher, dass die „Best Practices“ des Marktes in einem Produkt vereint sind, welches mit Ihnen mitwachsen kann, die neuesten Technologien nutzt und die bewährten Methoden Ihrer Branche abbildet.
Die englische Originalversion dieses Artikels von Augusto Vilarinho (veröffentlicht am 2. Juni 2020) finden Sie hier.
Critical Manufacturing bietet innovative Softwaretechnologie und Dienstleistungen zum Betrieb der modernsten Fertigungen weltweit. Das Manufacturing Execution System (MES) der neuesten Generation steht im Zentrum von Industrie 4.0 durch die weitreichenden Möglichkeiten zur Integration, Mobile Anwendung, Konnektivität sowie logischer Dezentralisation. Das umfassende und durchgängige System erhöht die Performance, Kontrolle und Qualität in komplexen Fertigungsorganisationen.
Das Unternehmen ist Teil der Critical Group, einer 1998 gegründeten private Firmengruppe, die IT-Lösungen für geschäftskritische Anwendungen anbietet.
Für mehr Informationen besuchen Sie unsere Website www.criticalmanufacturing.de oder kontaktieren Sie uns unter kontakt@criticalmanufacturing.de.
Critical Manufacturing Deutschland GmbH
Maria-Reiche-Str. 1
01109 Dresden
Telefon: +49 (351) 4188-0639
Telefax: +49 (35205) 120020
http://www.criticalmanufacturing.de
Managing Director / Geschäftsführer
Telefon: +49 (351) 41880639
E-Mail: Tom.Bednarz@criticalmanufacturing.de
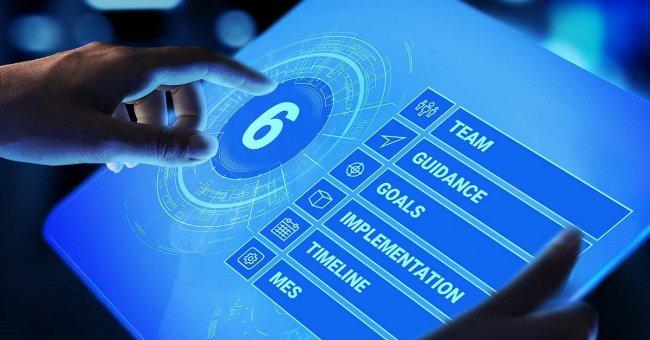
Die sechs Schritte zum erfolgreichen MES-Projekt
Die MES-Anwendungen (Manufacturing Execution Systems) sind in der modernen Fertigungslandschaft zu nachgefragten Lösungen geworden. Die Fertigung baut heute zunehmend auf der Verfügbarkeit und erfolgreichen Nutzung von Informationen auf, die den Kern der aktuellen industriellen Revolution – Industrie 4.0 – bilden.
Eine Manufacturing Operations Platform erfordert eine herausgehobene Positionierung der Fertigung. Nur so ist der Aufbau einer starken und flexiblen Lieferkette möglich, welche die geforderte Rentabilität sowie strategische Flexibilität gewährleistet. Dies setzt ein MES voraus, welches den Anforderungen der jeweiligen Branche optimal gerecht wird und so die treibende Kraft des Gesamtprozesses ist.
Die Ermittlung des Bedarfs an einer MES-Anwendung für die globale Fertigungsinfrastruktur wie z.B., um die Wertschöpfungskette zu integrieren, Fertigungsabläufe zu koordinieren, regelkonforme und effiziente Prozesse zu etablieren und handlungsrelevante Informationen in Echtzeit zu liefern, die an die entsprechende Hierarchieebene angepasst sind, wäre nur die Spitze des MES-Eisbergs. Das MES-Projekt entsteht erst, wenn die Führungsspitze die Notwendigkeit der MES-Implementierung oder der Updates des bestehenden Systems erkennt. Dazu kommen noch die Komplexität und Angst vor dem Scheitern. In diesem Beitrag werden Methoden untersucht, mit denen der Erfolg Ihres MES-Projekts sichergestellt und so Ihre Bedenken zerstreut werden können.
KOMPLEXITÄT BEWÄLTIGEN
IT-Projekte, insbesondere MES-Implementierungsprojekte, sind äußerst komplex, allein aufgrund einer Vielzahl von Variablen und Ergebnissen, Millionen von Transaktionen, die gleichzeitig stattfinden, sowie einer großen Zahl der Projektteilnehmer, die unterschiedliche Prioritäten haben. Es ist zwingend notwendig, eine einheitliche Ausgangsbasis in und zwischen den Fertigungsstätten zu schaffen, die manchmal nicht nur geografisch voneinander getrennt sind, sondern möglicherweise auch komplexere und unterschiedliche Fertigungsprozesse aufweisen.
Zu Beginn eines MES-Projektes muss eine klare Zielsetzung definiert werden. Was ist erforderlich? Wie soll es umgesetzt werden (z.B. durch Partner oder ein internes Team)? Und wie soll das Endergebnis aussehen? Diese Fragen ohne entsprechende Beratung zu beantworten, ist eine Herausforderung.
Für eine MES-Implementierung ist es entscheidend, bestimmte Grundlagen zu beachten, denn nur so ist eine gelungene Implementierung möglich. Was sind also die Voraussetzungen, die ein MES-Projekt zu einem Erfolg machen?
Bleiben Sie dran und lesen Sie den kompletten Artikel hier.
Critical Manufacturing bietet innovative Softwaretechnologie und Dienstleistungen zum Betrieb der modernsten Fertigungen weltweit. Das Manufacturing Execution System (MES) der neuesten Generation steht im Zentrum von Industrie 4.0 durch die weitreichenden Möglichkeiten zur Integration, Mobile Anwendung, Konnektivität sowie logischer Dezentralisation. Das umfassende und durchgängige System erhöht die Performance, Kontrolle und Qualität in komplexen Fertigungsorganisationen.
Das Unternehmen ist Teil der Critical Group, einer 1998 gegründeten private Firmengruppe, die IT-Lösungen für geschäftskritische Anwendungen anbietet.
Für mehr Informationen besuchen Sie unsere Website www.criticalmanufacturing.de oder kontaktieren Sie uns unter kontakt@criticalmanufacturing.de.
Critical Manufacturing Deutschland GmbH
Maria-Reiche-Str. 1
01109 Dresden
Telefon: +49 (351) 4188-0639
Telefax: +49 (35205) 120020
http://www.criticalmanufacturing.de
Managing Director / Geschäftsführer
Telefon: +49 (351) 41880639
E-Mail: Tom.Bednarz@criticalmanufacturing.de
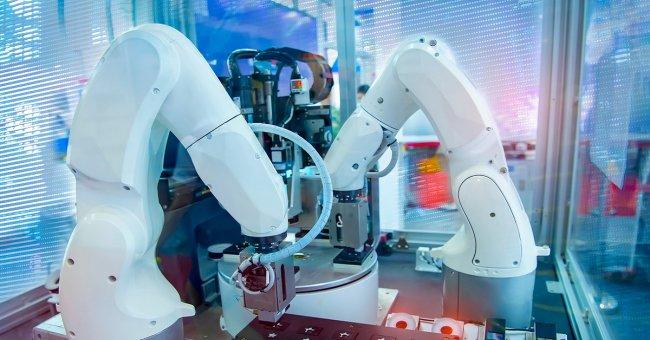
So bereiten Sie den Weg zu Ihrer autonomen Fabrik
Autonomie im Betrieb bedeutet die Möglichkeit ohne menschliches Eingreifen in den Fertigungsprozess zu agieren, um so Verlusten vorzubeugen. Der völlig autonome Prozess passt sich in iterativer Abfolge automatisch an die vorgegebenen Prozess-KPIs an und stellt sicher, dass es keine Verluste, Verzögerungen und Unterbrechungen gibt. So interagiert die Fabrik ständig mit der Prozessausrüstung, dem Material, das sich durch die Fertigung bewegt, und erfasst alle Prozessparameter. Darüber hinaus ist sie mit Anwendungen auf Unternehmensebene, wie beispielsweise ERP, verbunden und übermittelt Informationen an und von diesen Anwendungen, sodass die Produktion ohne Unterbrechung erfolgen kann.
Die Rolle des Personals besteht in solchen Fabriken darin, die Gesamtausführung zu überwachen und entsprechend den Anweisungen der intelligenten Anwendungen, die die Fabrik steuern und den Prozess orchestrieren, auszuführen/anzuwenden/einzustellen, wodurch die „menschliche“ Prozesskomponente ihre Haupttätigkeiten ausüben kann – jedenfalls aus der Perspektive der Prozessausführung.
Eine vollständig autonome Anlage erreicht den höchsten Digitalisierungsgrad, wenn alle modernen Technologien, wie Augmented Reality, Virtual Reality, Robotik, Machine Learning und Künstliche Intelligenz usw., zum Einsatz kommen. Das Ziel einer vollständig digitalisierten und autonomen Infrastruktur für den Fertigungsbetrieb besteht darin, in allen Fabriken innerhalb der Konzern-/Unternehmensgruppe einen homogenen Digitalisierungsgrad zu erreichen. Auf diese Weise können die Vorteile von Industrie 4.0 konzernweit in ähnlicher Weise umgesetzt und die Wirksamkeit der Implementierung anhand des geteilten/erworbenen Wissens und der Erfahrungen greifbar gemacht werden.
Wie fängt man an?
Bleiben Sie dran und lesen Sie den kompletten Artikel hier.
Critical Manufacturing bietet innovative Softwaretechnologie und Dienstleistungen zum Betrieb der modernsten Fertigungen weltweit. Das Manufacturing Execution System (MES) der neuesten Generation steht im Zentrum von Industrie 4.0 durch die weitreichenden Möglichkeiten zur Integration, Mobile Anwendung, Konnektivität sowie logischer Dezentralisation. Das umfassende und durchgängige System erhöht die Performance, Kontrolle und Qualität in komplexen Fertigungsorganisationen.
Das Unternehmen ist Teil der Critical Group, einer 1998 gegründeten private Firmengruppe, die IT-Lösungen für geschäftskritische Anwendungen anbietet.
Für mehr Informationen besuchen Sie unsere Website www.criticalmanufacturing.de oder kontaktieren Sie uns unter kontakt@criticalmanufacturing.de.
Critical Manufacturing Deutschland GmbH
Maria-Reiche-Str. 1
01109 Dresden
Telefon: +49 (351) 4188-0639
Telefax: +49 (35205) 120020
http://www.criticalmanufacturing.de
Managing Director / Geschäftsführer
Telefon: +49 (351) 41880639
E-Mail: Tom.Bednarz@criticalmanufacturing.de
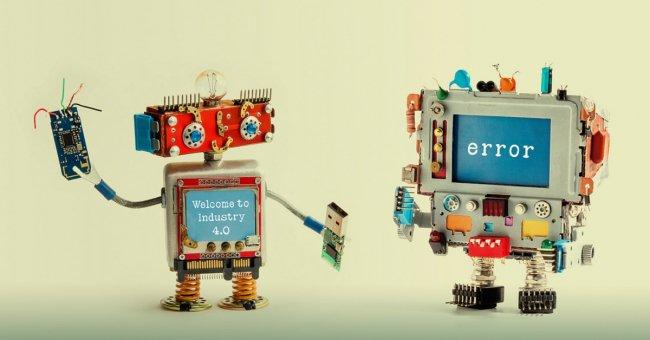
Die Zukunft der Fertigung und die Rolle des MES
INDUSTRIE 4.0 UND HERAUSFORDERUNGEN DER DIGITALEN TRANSFORMATION
Die neue industrielle Revolution (üblicherweise als Industrie 4.0 bezeichnet) fing am Anfang des vergangenen Jahrzehnts an und eröffnete damit das Zeitalter der Hyper-Konnektivität in Unternehmen und anderen Bereichen, wo sofort verfügbare, vielfältige, handlungsrelevante Informationen und deren Nutzung die Grundlage der geschäftlichen und strategischen Entscheidungen bildeten. Der Einsatz neuer und komplexer Technologien und ihre Integration in bestehende Arbeitsabläufe, ob durch Anpassung oder Umgestaltung von Prozessen, wurde zum wichtigen Diskussionsthema in den Führungsetagen. So begannen Fertigungsunternehmen, wie auch der Rest der Welt, über Technologien wie z.B. Augmented Reality, Virtual Reality, künstliche Intelligenz und 3D-Druck sowie über das industrielle Internet der Dinge und die Cloud nachzudenken, um ihren Wandel zu einem modernen, digitalen Unternehmen zu vollziehen.
Das zentrale Thema dieser digitalen Transformation war die Notwendigkeit, weitgehend integrierte, offene, wertschöpfungsorientierte Ökosysteme zu entwickeln. Diese Ökosysteme sind im Wesentlichen datengestützt und über verschiedene Organisationsebenen sowie Standortgrenzen hinaus durch IT-Anwendungen – wie MES – miteinander vernetzt, sodass moderne Technologien integriert und zugänglich gemacht werden. Die relevanten Stakeholder werden gleichzeitig dabei unterstützt, die bereitgestellten Informationen und Technologien zu nutzen. Die MES-Systeme setzen diese moderne Technologie ein, orchestrieren/verbinden Prozesse entlang der gesamten Wertschöpfungskette, liefern handlungsrelevante Echtzeit-Informationen und verknüpfen diese mit Anwendungen auf Unternehmensebene. So werden die MES-Lösungen zum wichtigsten Katalysator für die digitale Transformation der Fertigungslieferketten.
Mehr zu diesem Thema erfahren Sie hier.
Critical Manufacturing bietet innovative Softwaretechnologie und Dienstleistungen zum Betrieb der modernsten Fertigungen weltweit. Das Manufacturing Execution System (MES) der neuesten Generation steht im Zentrum von Industrie 4.0 durch die weitreichenden Möglichkeiten zur Integration, Mobile Anwendung, Konnektivität sowie logischer Dezentralisation. Das umfassende und durchgängige System erhöht die Performance, Kontrolle und Qualität in komplexen Fertigungsorganisationen.
Das Unternehmen ist Teil der Critical Group, einer 1998 gegründeten private Firmengruppe, die IT-Lösungen für geschäftskritische Anwendungen anbietet.
Für mehr Informationen besuchen Sie unsere Website www.criticalmanufacturing.de oder kontaktieren Sie uns unter kontakt@criticalmanufacturing.de.
Critical Manufacturing Deutschland GmbH
Maria-Reiche-Str. 1
01109 Dresden
Telefon: +49 (351) 4188-0639
Telefax: +49 (35205) 120020
http://www.criticalmanufacturing.de
Managing Director / Geschäftsführer
Telefon: +49 (351) 41880639
E-Mail: Tom.Bednarz@criticalmanufacturing.de
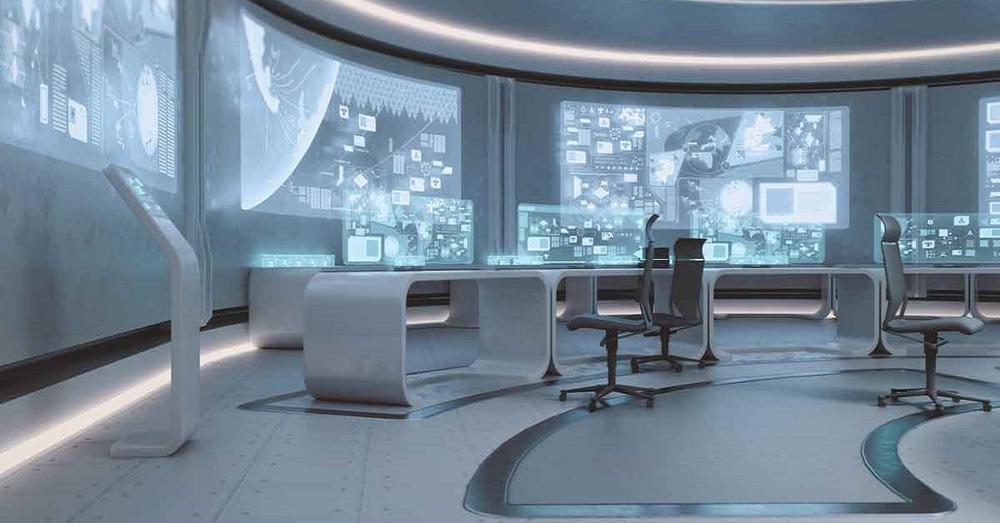
Fabrik der Zukunft
Es handelt sich dabei um die Verknüpfung der Produktionsprozesse und -abläufe mit Unternehmenssystemen, um mehr Produktivität, Effizienz und neue Kapazitäten aufgrund der Technologie-Nutzung und mit weniger Personaleinsatz zu sichern:
- Ausführung aller manuellen Tätigkeiten mit Hilfe von Robotern, SPS, Fördersystemen, Sensoren, FTS und Maschinen im Allgemeinen. Der Automatisierungsgrad dieser physischen Tätigkeiten hängt von der finanziellen Durchführbarkeit, den Mitarbeiter-Kompetenzen, der technologischen Ambition des Unternehmens, der Risikobereitschaft, der Prozesskomplexität und dergleichen ab.
- Systematische Datenerfassung: automatisch, papierlos, lückenlos.
- Dashboards und handlungsrelevante Berichte, die auf allen Betriebsebenen in Echtzeit zugänglich sind.
- Verwendung von Daten zur Generierung von Informationen/Wissen, um Prozesse, ihre Qualität und ihren Ablauf sowie die Integration innerhalb unterschiedlicher Prozesse besser, einfacher, schneller und kostengünstiger zu gestalten.
Welche Bereiche betrifft also Automatisierung und Digitalisierung in der Fertigung?
FERTIGUNGSBEREICH
Hier wird das Produkt hergestellt. Die SPS/PC/PAC bildet dabei den zentralen Punkt (SPS = speicherprogrammierbare Steuerung (engl. PAC); PC = Personalcomputer; PAC = programmierbare Automatisierungssteuerung). All diese Begriffe werden im Folgenden allgemein als SPS bezeichnet.
Die SPS ermöglicht die Steuerung der physischen Welt – beispielsweise Prozessabläufe, Prozesssteuerung im geschlossenen Regelkreis (einschließlich einzelner Prozessschritte: Handling, Inspektion, Formen, Schneiden, Verpacken, Stanzen usw.) – durch logische Steuerung unterschiedlicher Betriebsmitteln/Technologien wie Förderanlagen, Sensoren, Roboter, RFID, optischer Prüfsysteme, mechanischer Systeme, Maschinen etc.
Die SPS stellt außerdem eine Verbindung zum HMI/SCADA-System her, um visuelle Informationen in Echtzeit anzuzeigen – KPIs, Alarmmeldungen, Diagramme, Visualisierungen der Maschinen, Shopfloor-Status, Produktinformationen usw. aus der SPS oder aus den Datenbanken. (HMI/SCADA ist ein äußerst wichtiges Instrument zur Unterstützung von Aufsichtspersonal, Technikern und Maschinenführern in der Produktion. Wie eine Art Fenster bietet dieses Visualisierungstool alle digitalen Informationen, die für die Produktion erforderlich sind.)
Die SPS kann außerdem so programmiert werden, dass Informationen in eine Datenbank geschrieben und Informationen aus einer Datenbank abgerufen werden können. Nicht alle Daten aus der SPS müssen im SCADA angezeigt werden, sie können in einer Datenbank für zukünftige Nutzung gespeichert oder verworfen werden. Sie kann zudem Daten aus verschiedenen Quellen wie Software von Drittanbietern, MES, ERP oder Analytics-Tools beziehen.
FERTIGUNGSDATENBANKEN
Die Fertigungsdatenbanken erfassen anhand von SPS Informationen aus dem Fertigungsbereich, die unter anderem Prozessparameter, Alarme, Maschinenstatus, Sensordaten betreffen. Sie können zudem Informationen sammeln, die durch Bediener in HMI/SCADA-Systeme eingegeben werden. Die meisten dieser Backend-Daten können als ein Informations-Feed für das Frontend, also MES, verwendet werden.
Ferner können Informationen aus den MES- und ERP-Systemen übernommen und in die Produktionsdatenbanksysteme eingegeben werden, die entweder als logische Grundlage für einen Prozess dienen oder im SCADA angezeigt werden.
Diese Datenbanken für die Produktion enthalten alle:
- Prozess- und Produktinformationen – Sensordaten, Bildmaterial, Parameter, Rohstoffe, Rezepte, Routing-Informationen zum Produkt sowie Richtlinien
- Mitarbeiterinformationen bezüglich der ausgeführten Tätigkeit, des Trainingsniveaus, der Login-Berechtigung – Inspektoren, Techniker, Gruppenleiter und Vorgesetzte
- Maschinen- und Systeminformationen – Durchlaufzeiten, Ausfallzeiten, Alarme, Vorfälle, Kapazitätsengpässe, Störungen, Blockierungen, Wartungsverlauf.
Den kompletten Artikel zu diesem Thema finden Sie hier.
Critical Manufacturing bietet innovative Softwaretechnologie und Dienstleistungen zum Betrieb der modernsten Fertigungen weltweit. Das Manufacturing Execution System (MES) der neuesten Generation steht im Zentrum von Industrie 4.0 durch die weitreichenden Möglichkeiten zur Integration, Mobile Anwendung, Konnektivität sowie logischer Dezentralisation. Das umfassende und durchgängige System erhöht die Performance, Kontrolle und Qualität in komplexen Fertigungsorganisationen.
Das Unternehmen ist Teil der Critical Group, einer 1998 gegründeten private Firmengruppe, die IT-Lösungen für geschäftskritische Anwendungen anbietet.
Für mehr Informationen besuchen Sie unsere Website www.criticalmanufacturing.de oder kontaktieren Sie uns unter kontakt@criticalmanufacturing.de.
Critical Manufacturing Deutschland GmbH
Maria-Reiche-Str. 1
01109 Dresden
Telefon: +49 (351) 4188-0639
Telefax: +49 (35205) 120020
http://www.criticalmanufacturing.de
Managing Director / Geschäftsführer
Telefon: +49 (351) 41880639
E-Mail: Tom.Bednarz@criticalmanufacturing.de