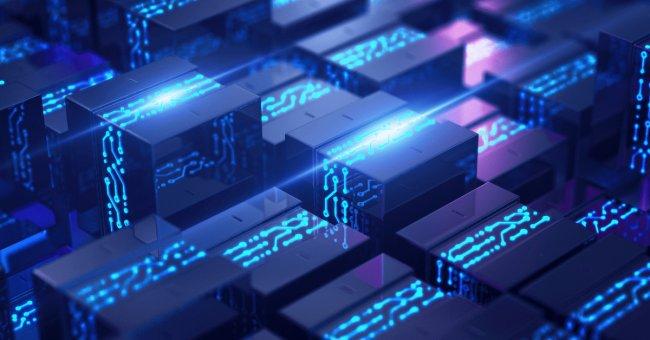
Container-Technologie in modernen MES – der richtige Ansatz?
"Once a new technology rolls over you, if you’re not part of the steamroller, you’re part of the road" – Stewart Brand, Autor
Die groß angelegte und schnelle Digitalisierung von Wertschöpfungsketten wird weltweit von vielen Unternehmen angestrebt, um moderne Technologien sowie Vorteile von Industrie 4.0 nutzen zu können. Diese drängende Notwendigkeit, die Arbeitsprozesse von Unternehmen und ihren Partnern zu ändern, hat sich durch die aktuelle globale COVID-Pandemie weiter verstärkt. Unternehmen müssen heute Nachfrageentwicklungen vorhersagen und so darauf reagieren können, dass es für die komplette Wertschöpfungskette am rentabelsten ist. Zugleich müssen Wertschöpfungsketten in unerwarteten Krisensituationen (nicht anders als in einer globalen Pandemie) agil und jederzeit skalierbar bleiben, um eventuelle Verluste und Beeinträchtigungen zu begrenzen. Die Forderung nach mehr Widerstandsfähigkeit, Agilität und Effizienz existierte schon immer; die Notwendigkeit, diese schneller und in einem großen Rahmen zu erreichen, wurde erst in den letzten Jahren, insbesondere aber im vergangenen Jahr, laut. Eine empfehlenswerte Publikation von McKinsey über diese beschleunigte Umstellung, die durch die Pandemie verstärkt oder vielmehr in Gang gesetzt wurde, finden Sie hier.
Es ist jedoch von entscheidender Bedeutung, dass das Top-Management sowie Experten im Unternehmen und der entsprechenden Wertschöpfungskette Technologietrends kennen oder zumindest ein grundlegendes Verständnis davon haben, wie moderne Digitalisierungslösungen funktionieren, bevor eine Entscheidung für eine bestimmte Technologie, ein Tool, eine Plattform oder einen Anbieter getroffen wird.
Die Umsetzung von Industrie 4.0 beginnt für Fertigungsunternehmen und ihre Wertschöpfung grundsätzlich dann, wenn sie über eine MES-Anwendung verfügen, die nicht nur innerhalb des Unternehmens und der entsprechenden Werke für die Prozessausführung eingesetzt werden kann, sondern auch mit anderen übergeordneten Unternehmensanwendungen in der gesamten Wertschöpfungskette integrierbar ist, um die Konnektivität zu gewährleisten, die IIoT und Industrie 4.0 vorgeben.
Auch in Unternehmen, die ein altes MES oder eine MES-ähnliche Anwendung in der Fertigung einsetzen, ist das System wahrscheinlich nicht ausreichend dafür gerüstet, die Digitalisierungsziele einer eigentlichen Transformation im Sinne von Industrie 4.0 zu erreichen. Ein modernes MES löst in der Regel ein Altsystem entweder schrittweise oder in einem einzigen Schritt anhand eines sog. Urknall-Ansatzes (en. Big Bang) ab, bei dem der gesamte Betrieb auf die neue Anwendung umgestellt wird, unabhängig davon, welche Methode zur Implementierung genutzt wird. Es wird jedoch offensichtlich, dass die Implementierung einer modernen, Industrie-4.0-fähigen MES-Anwendung ein großes Unterfangen ist und Beteiligte aus der Geschäftsleitung, der IT, dem operativen Geschäft und sogar externe Berater und Zulieferer einbinden muss, was für jede vorgenommene unternehmensweite IT-Umstellung typisch ist. Doch was ändert sich mit dem Einsatz des modernen MES, wenn der erforderliche Aufwand und die Zeit für die Umstellung äußerst hoch sind? Wie profitiert das Unternehmen, welches die Anwendung einführt, unmittelbar von den positiven Effekten und Verbesserungen, die in einem Industrie-4.0-Szenario erwünscht sind?
Grundlagen der Container-basierten Virtualisierung
Zunächst einmal ein paar Grundlagen zu Containern. Container sind eine Erweiterung oder Weiterentwicklung von virtuellen Maschinen, ersetzen diese jedoch nicht. Virtuelle Maschinen emulieren virtuelle Hardware und führen unterschiedliche Betriebssysteme aus, was höhere Ressourcenanforderungen für einen einzelnen Server bedeutet.
Unseren kompletten Blog-Beitrag zu diesem Thema lesen Sie hier.
Critical Manufacturing bietet innovative Softwaretechnologie und Dienstleistungen zum Betrieb der modernsten Fertigungen weltweit. Das Manufacturing Execution System (MES) der neuesten Generation steht im Zentrum von Industrie 4.0 durch die weitreichenden Möglichkeiten zur Integration, Mobile Anwendung, Konnektivität sowie logischer Dezentralisation. Das umfassende und durchgängige System erhöht die Performance, Kontrolle und Qualität in komplexen Fertigungsorganisationen.
Das Unternehmen ist Teil der Critical Group, einer 1998 gegründeten private Firmengruppe, die IT-Lösungen für geschäftskritische Anwendungen anbietet.
Für mehr Informationen besuchen Sie unsere Website www.criticalmanufacturing.de oder kontaktieren Sie uns unter kontakt@criticalmanufacturing.de.
Critical Manufacturing Deutschland GmbH
Maria-Reiche-Str. 1
01109 Dresden
Telefon: +49 (351) 4188-0639
Telefax: +49 (35205) 120020
http://www.criticalmanufacturing.de
Managing Director / Geschäftsführer
Telefon: +49 (351) 41880639
E-Mail: Tom.Bednarz@criticalmanufacturing.de
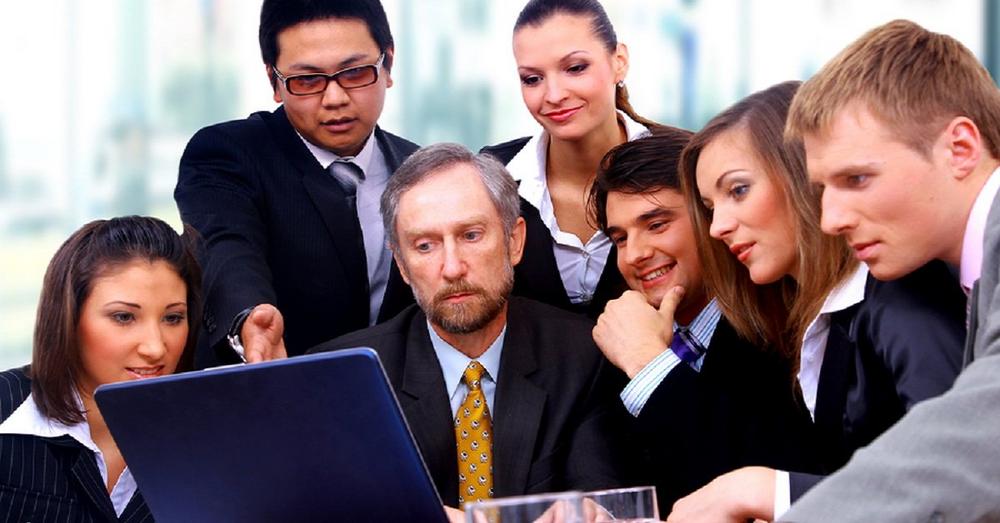
Anleitung zum erfolgreichen MES-Austausch
Die Migration von Daten und Prozessen aus einem Legacy-System in ein neues MES ist mit Risiken verbunden, denn in einem MES werden umsatzrelevante Prozesse verwaltet. Es ist für den Erfolg des Migrationsprojektes entscheidend, alle betroffenen Abteilungen einzubinden und zu aktivieren. Dabei ist eine Strategie wichtig, die das Unternehmensprofil abbildet.
Überblick über Migrationsstrategien
Migrationsstrategien werden hauptsächlich von drei Faktoren bestimmt:
- Zeit: die Zeit, die vom Projektstart bis zum Abschluss benötigt wird, einschließlich der Phasen vor der Migration, der eigentlichen Migration und nach der Migration.
- Risiko: die Risikoeinschätzung und das Gefährdungspotential (Wahrscheinlichkeit X Kosten).
- Kosten: die Kosten, die mit der Planung und der Ausführung der festgelegten Strategie einhergehen, inklusive der Opportunitätskosten (Ausfallzeiten, Abwesenheit eines Teammitglieds zur Ausführung einer bestimmten Aufgabe usw.).
Diese Faktoren müssen bewertet und hinsichtlich der möglichen Alternativen zur gewählten Migration-Strategie analysiert werden. Die Gewichtung hängt von der Wechselwirkung der Anwendungen untereinander ab (Schnittstellen-Anzahl, die zwischen Anwendungen selbst und anderen Systemen bestehen), dem durch das MES erreichbare Automatisierungsgrad sowie den zu erwartenden Auswirkungen aufgrund der einzelnen MES-Ausfallzeiten, während das MES nicht verfügbar ist.
Migrationsstrategie: Arten der Implementierung
Es gibt drei grundlegende Möglichkeiten zur MES-Implementierung, die zu berücksichtigen sind:
- Big Bang. Dies ist eine Strategie, bei der das alte MES abgelöst und durch ein neues MES ersetzt wird. Diese Strategie ist die disruptivste, aber auch die wirkungsvollste. Es gibt dabei keine Legacy-Systeme und keine doppelten Anwendungen, die gehandhabt werden müssen. Viele digitale Transformationsprojekte verwenden diesen sogenannten Urknall-Ansatz.
- Schrittweise MES-Einführung. Dabei wird das neue MES schrittweise eingeführt, aufgeteilt entweder nach funktionalen Geschäftsbereichen (Verpackung, Produktion, Qualitätskontrolle), nach Fertigungseinheiten (Bereich, Schritt oder Maschine), nach MES-Funktion (Betriebsmittel, Personal, Maschinenmanagement, Rezeptmanagement) oder nach Charge.
- Parallelsysteme. Das alte und neue MES werden so lange nebeneinander eingesetzt, bis das neue MES verlässlich und leistungsfähig funktioniert, sodass die Abschaltung des Altsystems möglich wird.
Mehr Informationen zu diesem Thema finden Sie auf unserer Webseite.
Dieser Blog-Beitrag ist ein Auszug aus unserem Whitepaper "Guide to Successful MES Replacement, Migration Strategies Explained". Klicken Sie bitte hier, um das vollständige Whitepaper zu lesen.
Critical Manufacturing bietet innovative Softwaretechnologie und Dienstleistungen zum Betrieb der modernsten Fertigungen weltweit. Das Manufacturing Execution System (MES) der neuesten Generation steht im Zentrum von Industrie 4.0 durch die weitreichenden Möglichkeiten zur Integration, Mobile Anwendung, Konnektivität sowie logischer Dezentralisation. Das umfassende und durchgängige System erhöht die Performance, Kontrolle und Qualität in komplexen Fertigungsorganisationen.
Das Unternehmen ist Teil der Critical Group, einer 1998 gegründeten private Firmengruppe, die IT-Lösungen für geschäftskritische Anwendungen anbietet.
Für mehr Informationen besuchen Sie unsere Website www.criticalmanufacturing.de oder kontaktieren Sie uns unter kontakt@criticalmanufacturing.de.
Critical Manufacturing Deutschland GmbH
Maria-Reiche-Str. 1
01109 Dresden
Telefon: +49 (351) 4188-0639
Telefax: +49 (35205) 120020
http://www.criticalmanufacturing.de
Managing Director / Geschäftsführer
Telefon: +49 (351) 41880639
E-Mail: Tom.Bednarz@criticalmanufacturing.de
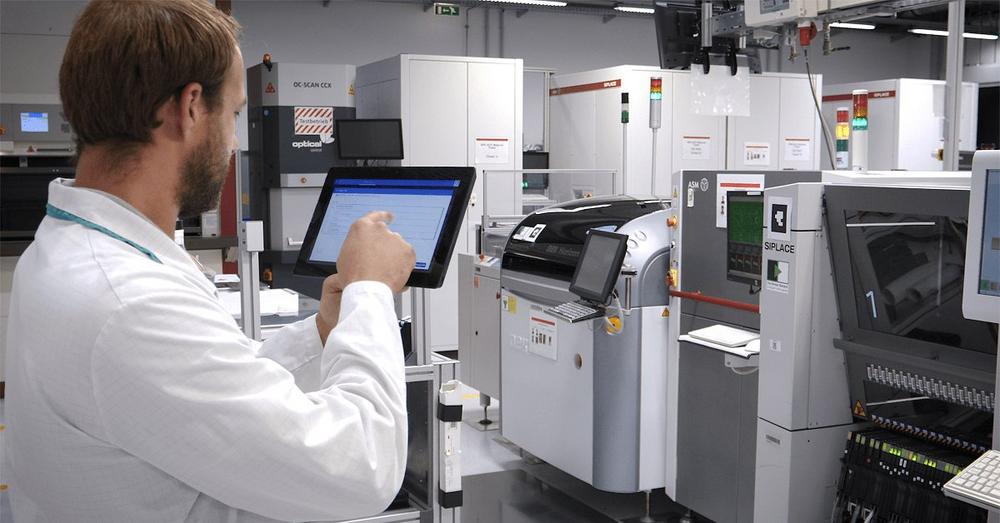
Anleitung für den erfolgreichen Wechsel zur papierlosen Fertigung
Zu Beginn sind die drei wichtigsten Infos zusammengefasst:
- Papierbasierte Systeme sind anfällig für menschliche Fehler, ineffizient, unflexibel und verursachen Verzögerungen bei der Entscheidungsfindung – dies ist auch der Grund für höhere Kosten der papierbasierten Systeme im Vergleich zu digitalen.
- Es gilt Integrationsfähigkeit und Konfigurierbarkeit, Benutzerfreundlichkeit und Mobilität bei der Auswahl des richtigen Tools zur Umstellung auf eine papierlose Fertigung zu berücksichtigen.
- Der Weg ist das Ziel. Erfassen Sie zunächst Ihre Daten mit Hilfe einer anwenderfreundlichen Benutzeroberfläche und schon bald sind tiefere Einblicke verfügbar, sodass Ihre Fertigungsprozesse neugestaltet werden können.
Zur Digitalisierung gehören unter anderem Automatisierung und Ablösung der händischen Datenerfassung, Aufzeichnung, Analyse und Übermittlung von Daten sowie Verbesserung automatisierter Prozessschritte. Dies bedeutet die Ablösung der existierenden Systeme, bei denen Daten auf Papierformularen aufgezeichnet und anschließend entweder abgetippt oder eingescannt werden, um so eine digitale Kopie zu erstellen. Eine der wichtigsten Forderungen der Digitalisierung ist eine papierlose Arbeitsumgebung.
Papiergestützte Datenerfassungssysteme sind fehleranfällig, außerdem verursacht die Pflege solcher Systeme zusätzliche Kosten. Man denke dabei an einen Aktenschrank mit vier Schubladen:
- Fassungsvermögen von 15.000-20.000 Papierseiten
- 25.000 US-Dollar Kosten der Befüllung
- 2.000 US-Dollar Instandhaltung pro Jahr
Die Vorteile der papierlosen Fertigung erkennen und nutzen
Der erste Schritt zum papierlosen Betrieb besteht darin, die Kosten eines papierbasierten Systems einschließlich der Datenerfassung und -speicherung zu verstehen. Neben den Kosten einer herkömmlichen papiergestützten Aktenablage gibt es weitere greifbare Vorteile, die für einen papierlosen Betrieb sprechen:
- Verdreifachung der Bearbeitungskapazität (Gartner)
- Steigerung der Produktivität um bis zu 50 % (IDC)
- Sofortiger Zugriff auf entscheidungskritische Daten (was das eigentliche Ziel ist)
- Reduzierung der Speicherplatzkosten um bis zu 80 %
- Rückverfolgbarkeit und Einhaltung von gesetzlichen Auflagen (21CFR Part 11, Sarbanes-Oxley, FSMA usw.)
- Genauigkeit: Die automatische Dateneingabe ergibt eine Genauigkeit von 99,959 bis 99,99 %
Einen nachhaltigeren Ansatz anstreben
Zu etwas schwächeren, aber durchaus wichtigen Argumenten gehört die Umweltbelastung. Auch reine Kosten des Papiermanagements und eine sofortige Übersicht über Ereignisse gehören dazu. Mit der Digitalisierung Ihrer Arbeitsabläufe können alle Daten sofort für andere Anwendungen zur Verbesserung des Produktions-/Betriebsmanagements zugänglich gemacht werden, darunter Visualisierung, Datenspeicherung und MES-Anwendungen.
Verbesserte Arbeitsabläufe wirken sich unmittelbar auf das Endergebnis aus: Unternehmen, die eine papierlose Fertigung eingeführt haben, verzeichnen bis zu 75% weniger Überstunden, 90% weniger Kennzeichnungsfehler und eine Einsparung von bis zu 7.500 US-Dollar an Arbeitskosten pro Anwender.
Kürzere Latenzzeit bei Ihren Entscheidungen
Kürzere Entscheidungslatenzzeiten stellen einen der wichtigsten Vorteile der Digitalisierung hinsichtlich der versteckten Kosten, die aktuell alle papierbasierten Vorgänge betreffen. So werden Daten aufgrund der Digitalisierung nahezu ohne Verzögerung erfasst und dokumentiert; Entscheidungsprozesse laufen wesentlich schneller ab, sodass keine Verluste entstehen, die infolge von Verzögerungen aufgrund der manuellen Dokumentation möglich sind.
Verringerung von ineffizienten manuellen Datenerfassungsvorgängen und Fehlerquellen
Die Verwendung von Papier in der Fertigung bedeutet auch, dass die Mitarbeiter die redundante Tätigkeit der Datenerfassung zu bestimmten Zeiten und Phasen eines bestimmten Vorgangs durchführen müssen, was möglicherweise zu Fehlern bei der Datenaufzeichnung führt. Eine papierbasierte Dokumentation und die daraus resultierenden Fehler sind kostspielig für ein Unternehmen, das äußerst komplexe oder gesetzlich geregelte Erzeugnisse herstellt. Ein banaler Aufzeichnungsfehler führt in stark regulierten Branchen zu Produktrückrufen und kann in seiner schlimmsten Konsequenz finanzielle Verluste und eine Rufschädigung verursachen, sollte eine nicht-konforme Produkt-Charge auf den Markt gelangen.
Den vollständigen Blog-Beitrag zu diesem Thema finden Sie hier.
Critical Manufacturing bietet innovative Softwaretechnologie und Dienstleistungen zum Betrieb der modernsten Fertigungen weltweit. Das Manufacturing Execution System (MES) der neuesten Generation steht im Zentrum von Industrie 4.0 durch die weitreichenden Möglichkeiten zur Integration, Mobile Anwendung, Konnektivität sowie logischer Dezentralisation. Das umfassende und durchgängige System erhöht die Performance, Kontrolle und Qualität in komplexen Fertigungsorganisationen.
Das Unternehmen ist Teil der Critical Group, einer 1998 gegründeten private Firmengruppe, die IT-Lösungen für geschäftskritische Anwendungen anbietet.
Für mehr Informationen besuchen Sie unsere Website www.criticalmanufacturing.de oder kontaktieren Sie uns unter kontakt@criticalmanufacturing.de.
Critical Manufacturing Deutschland GmbH
Maria-Reiche-Str. 1
01109 Dresden
Telefon: +49 (351) 4188-0639
Telefax: +49 (35205) 120020
http://www.criticalmanufacturing.de
Managing Director / Geschäftsführer
Telefon: +49 (351) 41880639
E-Mail: Tom.Bednarz@criticalmanufacturing.de
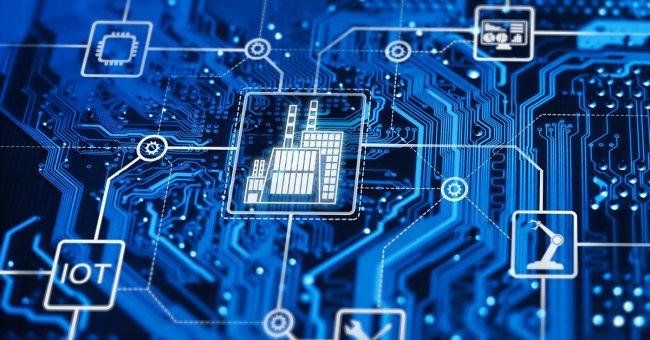
MES: Maschinenkommunikation und die Rolle von Standards
Industrie 4.0 bedeutet Veränderung und treibt diese auch voran, ähnlich wie es schon bei drei vorangegangenen industriellen Revolutionen der Fall war. Sie erfordert Anpassungen von Unternehmensstrategie, Unternehmensführung, Prozesstechnologie, IT, unternehmensweite Einbindung in die Wertschöpfungskette, Engagement der Mitarbeiter und vor allem Kommunikation.
Die neue industrielle Revolution ist im Kern globaler und setzt Anpassungen hinsichtlich zahlreicher Aspekte der Geschäftsabläufe voraus. Der Schwerpunkt liegt dabei auf der Entwicklung von Möglichkeiten zur Generierung, Nutzung und Handhabung großer Datenmengen, die folglich einen geschäftlichen Mehrwert in Form von einem verbesserten operativen Kenntnisstand bieten, um strategische Entscheidungen kurzfristig und langfristig zu unterstützen.
Der vielleicht wichtigste Aspekt dieser vierten industriellen Revolution ist, dass die Informationsinfrastruktur bis zum "Edge" erweitert wurde. So können intelligente Geräte und Anwendungen, miteinander kommunizieren und autonome Entscheidungen in Echtzeit treffen. Die Genauigkeit und Geschwindigkeit der Kommunikation ist dabei entscheidend und muss permanent, automatisch, sicher und präzise erfolgen.
In Fertigungsunternehmen, die bereit sind in diese neue industrielle Revolution zu investieren, ist daher eine Integration der Fertigung mit der gesamten Unternehmensstruktur notwendig, um die Effizienz der Edge-Technologie auszuschöpfen. Prozess- und Maschinendaten müssen zum Erreichen dieser Effizienz aus jeder Transaktion in der Fertigung erfasst und mit übergeordneten Anwendungen wie MES verknüpft werden. Das Ergebnis dessen sind Prozess- und Betriebsinformationen, die als Grundlage für sofortige, mittelfristige und langfristige Maßnahmen und Entscheidungen eingesetzt werden können, und zwar in Abhängigkeit vom Schweregrad des Ereignisses, den Zeiträumen für die Datenanalyse und dem Geschäftsablauf.
Doch die Integration zwischen MES und Prozesskomponenten gestaltet sich oft nicht einfach. Eine Kombination aus veralteten, kundenspezifischen und modernen Systemen, Software und Dateninfrastrukturen bedeutet eine extrem hohe Komplexität. Häufig fehlen auch Standard-Integrationsmethoden.
Es existieren zwar Standards und Protokolle für die Kommunikation auf Maschinenebene und den Datentransfer. Diese machen Verknüpfung zu Steuerung und übergeordneten Anwendungen sicherer und unkomplizierter. Dennoch, je nach Maschinenalter, Bedarf an mehreren Schnittstellen und Kombination an modernen und Legacy-Geräten und -anwendungen, kann der Komplexitätsgrad selbst innerhalb einer Fabrik ziemlich hoch sein. Die Gesamtkomplexität steigt exponentiell mit der zunehmenden Anzahl der geografisch und technologisch abgegrenzten Standorte an.
Kontinuierliche Kommunikation ist ein Muss
Diese Notwendigkeit der kontinuierlichen Kommunikation bedeutet zahlreiche Herausforderungen für Fertigungsunternehmen. Eine typische Fertigungseinheit verfügt in der Regel über Maschinen unterschiedlicher Anbieter, wobei die Typen und die Komplexität je nach Branche und Fertigungsprozess variieren. Diese Komplexität reicht von geringen Variationen von Maschinen und Herstellern bis zu vielen unterschiedlichen Maschinen von sehr vielen unterschiedlichen Herstellern innerhalb einer Produktion.
Eine weitere Komplexitätsebene kommt hinzu, wenn die einzelnen Komponenten mit eigener Software (und Protokollen) arbeiten. Dies trifft insbesondere dann zu, wenn die Maschinen alt sind oder in Anwendungsbereichen eingesetzt werden, in denen Interoperabilität nicht gefordert oder im Prozess integriert ist, wie etwa bei älteren Verpackungslinien oder kundenspezifischen Prozesseinrichtungen, die für einen einzelnen, spezifischen Arbeitsschritt ausgelegt sind.
Lesen Sie den kompletten Blog-Beitrag zu diesem Thema hier.
Critical Manufacturing bietet innovative Softwaretechnologie und Dienstleistungen zum Betrieb der modernsten Fertigungen weltweit. Das Manufacturing Execution System (MES) der neuesten Generation steht im Zentrum von Industrie 4.0 durch die weitreichenden Möglichkeiten zur Integration, Mobile Anwendung, Konnektivität sowie logischer Dezentralisation. Das umfassende und durchgängige System erhöht die Performance, Kontrolle und Qualität in komplexen Fertigungsorganisationen.
Das Unternehmen ist Teil der Critical Group, einer 1998 gegründeten private Firmengruppe, die IT-Lösungen für geschäftskritische Anwendungen anbietet.
Für mehr Informationen besuchen Sie unsere Website [url=http://www.criticalmanufacturing.de]www.criticalmanufacturing.de[/url] oder kontaktieren Sie uns unter kontakt@criticalmanufacturing.de.
Critical Manufacturing Deutschland GmbH
Maria-Reiche-Str. 1
01109 Dresden
Telefon: +49 (351) 4188-0639
Telefax: +49 (35205) 120020
http://www.criticalmanufacturing.de
Managing Director / Geschäftsführer
Telefon: +49 (351) 41880639
E-Mail: Tom.Bednarz@criticalmanufacturing.de
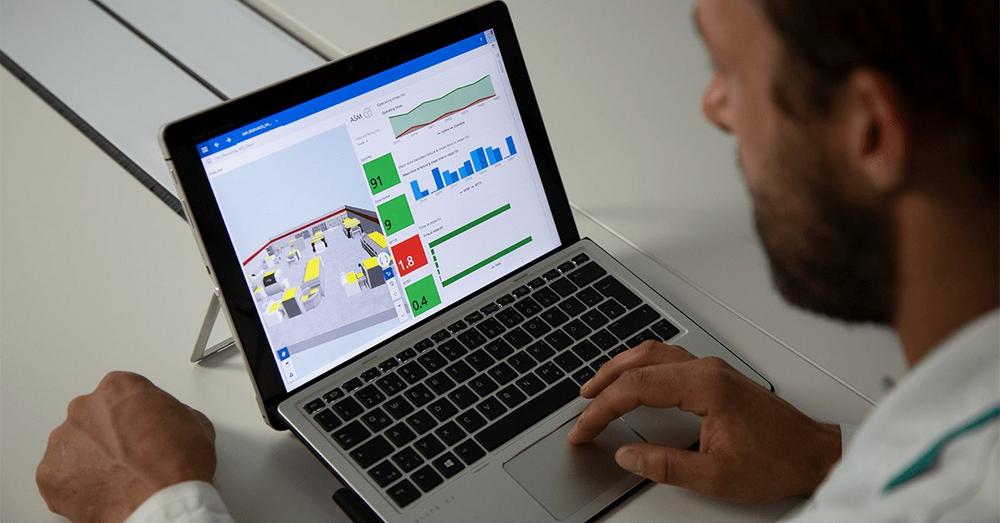
MES in einem Brownfield-Projekt
Die Weichen für eine rasche Transformation der gesamten Wertschöpfungskette sind gestellt, und sie ist wichtiger denn je. Die Fähigkeit einer Wertschöpfungskette, Risiken frühzeitig zu erkennen und diesen mit automatisierten und intelligenten Maßnahmen entgegenzuwirken, welche über die gesamte Versorgungskette gestaffelt sind, kann den entscheidenden Unterschied bedeuten, ob ein Unternehmen erfolgreich bleibt oder scheitert. Gleichzeitig wird es dadurch widerstandsfähig gemacht, sodass mögliche neue Krisen ohne Schaden bewältigt werden können.
Industrie 4.0 zeigte bereits vor der Pandemie erste Erfolge für Early Adopters: Umfassende Digitalisierung von Betriebsabläufen und autonome, selbststeuernde Fertigungsmaschinen zählen zu den Ergebnissen einer erfolgreichen Industrie-4.0-Implementierung. Die Pandemie hat das Erreichen dieser Digitalisierung und Autonomie nur noch beschleunigt. Während jedoch die Notwendigkeit, eine digitale Transformation des bestehenden Betriebs zu verfolgen, äußerst klar ist, ist der Weg dahin mit Herausforderungen und Komplexität verbunden.
Eine der Voraussetzungen für die Durchführung eines Industrie-4.0-Projekts ist die Verfügbarkeit einer skalierbaren IT-Infrastruktur, welche die Nutzung moderner Technologien erlaubt. Für Wertschöpfungsketten in der Fertigung gilt, dass die Fabriken die Verbindung und die Kommunikation mit dem Unternehmen herstellen und zugleich durch die Automatisierung des Produktionsprozesses die Möglichkeit zur Selbststeuerung erhalten. Die notwendigen Kommunikations- und Integrationsfähigkeiten, um die Automatisierungsgrade der Selbstanpassung zu erreichen, setzen ein modernes MES im Mittelpunkt der IT-Infrastruktur sämtlicher Fertigungsstandorte voraus. Ein modernes MES macht den Fertigungsbereich in der gesamten Wertschöpfungskette zugänglich, denn es ermöglicht Anbindung an Anwendungen auf Unternehmensebene, schafft eine Dateninfrastruktur, unterstützt Automatisierung der Arbeitsabläufe und liefert einen digitalen Zwilling der Fertigung für eine bessere, effizientere Steuerung der Ressourcen.
Die sogenannten Brownfield-Projekte oder bestehende Fabriken bedeuten eine besondere Herausforderung bei der Einführung von Industrie 4.0. Diese Unternehmen, unabhängig davon, ob es sich hierbei um mehrere Standorte oder Fabriken handelt, unterscheiden sich möglicherweise erheblich zwischen den einzelnen Standorten oder Fabriken. Auch innerhalb eines Unternehmens können sie unterschiedliche Reifegrade hinsichtlich des operativen Betriebs und der IT-Infrastruktur aufweisen.
In jeder Fabrik sind möglicherweise unterschiedliche Maschinen, Produktionslinien und Prozesssteuerungen im Einsatz. Das bedeutet, dass die entsprechenden IT-Anwendungen ebenfalls unterschiedlich sind, wobei die Lösungen entweder von mehreren Anbietern stammen oder selbst entwickelt wurden.
Bei der Implementierung von Industrie 4.0 oder einem modernen MES im Rahmen eines Brownfield-Projekts muss man mit der Basisstruktur der jeweiligen Fabrik arbeiten, unabhängig davon, ob es sich um eine einzelne Fabrik oder eine Gruppe von Werken, eine komplexe oder einfache IT-Infrastruktur und vielfältige oder homogene Automatisierungs- und Informationsmanagementlösungen handelt. Sie haben also nicht die Freiheit, wie bei einem Greenfield-Projekt bei null anzufangen.
Bei einem Greenfield-Projekt beginnt Ihr Industrie-4.0-Projekt mit der entsprechenden Strategie, der Definition des angestrebten Endprodukts und dem Aufbau einer Infrastruktur/Lösung, die mit den Anforderungen an die Lieferkette und der Auswahl der Zulieferer übereinstimmt und so den Erfolg gewissermaßen garantiert.
Neuste Technologien wie IIoT, Machine Learning, Augmented Reality und andere Technologien rund um Industrie 4.0 sind bereits von Anfang an Bestandteil Ihrer Prozesse, sodass keine zusätzlichen Integrationen, kundenspezifische Programmierung und kostenintensive Einzellösungen erforderlich sind. Ihr MES kann zum zentralen Element Ihrer Strategie werden und mit anderen Anwendungen auf Unternehmens- und Betriebsebene zusammenwirken, um eine einheitliche Infrastruktur herzustellen, die Ihre Anforderungen an das Informationsmanagement und die Steuerung erfüllt.
Lesen Sie den kompletten Blog-Beitrag zu diesem Thema hier.
Critical Manufacturing bietet innovative Softwaretechnologie und Dienstleistungen zum Betrieb der modernsten Fertigungen weltweit. Das Manufacturing Execution System (MES) der neuesten Generation steht im Zentrum von Industrie 4.0 durch die weitreichenden Möglichkeiten zur Integration, Mobile Anwendung, Konnektivität sowie logischer Dezentralisation. Das umfassende und durchgängige System erhöht die Performance, Kontrolle und Qualität in komplexen Fertigungsorganisationen.
Das Unternehmen ist Teil der Critical Group, einer 1998 gegründeten private Firmengruppe, die IT-Lösungen für geschäftskritische Anwendungen anbietet.
Für mehr Informationen besuchen Sie unsere Website www.criticalmanufacturing.de oder kontaktieren Sie uns unter kontakt@criticalmanufacturing.de.
Critical Manufacturing Deutschland GmbH
Maria-Reiche-Str. 1
01109 Dresden
Telefon: +49 (351) 4188-0639
Telefax: +49 (35205) 120020
http://www.criticalmanufacturing.de
Managing Director / Geschäftsführer
Telefon: +49 (351) 41880639
E-Mail: Tom.Bednarz@criticalmanufacturing.de
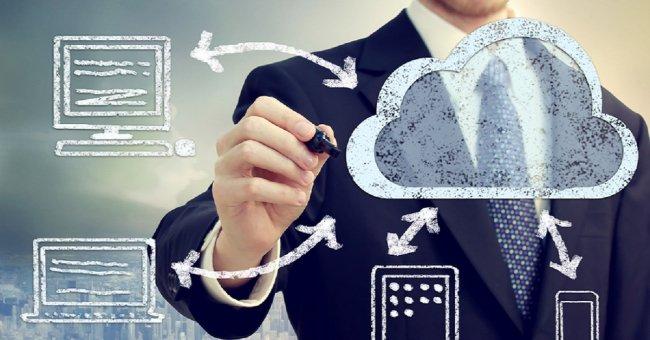
Das MES und die Cloud – Synergien schaffen
Das Cloud Computing gilt aus der Industrie-4.0-Perspektive neben weiteren fundamentalen IT-Technologien, wie etwa Simulation, Analytik, IoT und Mobilität, als eine entscheidende treibende Kraft der neuen Fertigungsdaten-Revolution. Es wird erwartet, dass die Cloud-Branche von 371 Milliarden US-Dollar im Jahr 2020 auf 832 Milliarden US-Dollar im Jahr 2025 wachsen wird, was eine beeindruckende jährliche Wachstumsrate (Compound Annual Growth Rate) von 17,5% bedeutet.
Im Hinblick auf die Rolle der Cloud in der Fertigung und die Art und Weise, wie eine MES-Anwendung die Cloud-Technologie nutzt und sich an diese anpasst, steckt die Praxis noch ziemlich in den Kinderschuhen –es fehlen zu befolgende Standardmethoden oder etablierte Best Practices. Der Cloud-Framework ist dagegen fest etabliert und bietet verschiedene Hosting-Optionen mit unterschiedlichen Einstiegspunkten von dort aus. Zunächst einmal betrachten wir die grundlegenden Elemente des MES und der Cloud, um zu verstehen, welche Vorteile das Cloud Computing bietet, warum sein Einsatz in der Fertigung für Unternehmen auf der ganzen Welt so vielversprechend ist und wie das MES mit der Cloud zusammenarbeitet und diese nutzt.
Wir untersuchen verschiedene Möglichkeiten ohne konkrete Festlegungen, denn die Rolle des Cloud Computing in einer bestimmten Wertschöpfungskette erfordert eine detaillierte Analyse der IT- und Fertigungsvorgänge sowie die Berücksichtigung der jeweiligen Unternehmensanforderungen und der Erwartungen der betroffenen Prozesseigentümer. Es ist außerdem sinnvoll, die Einsatzmöglichkeiten der vorhandenen Anwendungen und der Infrastruktur zu berücksichtigen, die entweder angepasst oder durch native Cloud-basierte Anwendungen ersetzt werden können.
BASISWISSEN: WAS IST DIE CLOUD?
Zunächst aber soll das Cloud Computing etwas besser beleuchtet werden, und zwar mit einer grundlegenden Definition des Begriffs "Cloud". Die Cloud ist eine sichere, flexible, kombinierte Plattform mit drei möglichen Services oder Hosting-Diensten: Infrastructure as a Service; Plattform as a Service und Software as a Service.
Diese Produkte unterscheiden sich, wie aus dem Bild oben ersichtlich ist, je nach Datenmenge, die in der Cloud gehostet werden, im Vergleich zu solchen Anwendungen, die außerhalb der Cloud-Architektur gehostet werden: vor Ort zu 100% physisch, während SaaS (Software as a Service) zu 100% virtuell ist (d.h. zu 100% in der Cloud).
Drei unterschiedliche Einsatzarten existieren darüber hinaus neben den genannten Varianten der Cloud-Lösungen (oben): Privat, hybrid und öffentlich.
Betrachten wir jedes einzelne Produkt genauer:
- Cloud-Bereitstellung/Anwendungs-Hosting vor Ort. Man spricht hier von einer "privaten" Cloud. Es gibt einen Einzelbenutzer (Mandant oder en. tenant), wobei die Cloud ausschließlich intern genutzt wird. Diese Option eignet sich für Unternehmen, die auf Sicherheit, IP-Schutz oder Anwendungs-Performanz (d.h. Echtzeit-Analyse und Entscheidungsfindung) bedacht sind.
- Hybrid-Cloud-Bereitstellung. Die Hybrid-Cloud stellt eine Kombination aus der privaten und öffentlichen Cloud dar. Diese Kombination ist dann sinnvoll, wenn sensible IP- und Applikationsfunktionen lokal benötigt werden, die Sicherung und die Speicherung der Primärdaten selbst jedoch in einer öffentlichen (Multi-Mandanten-)Cloud erfolgt.
- Öffentliche Cloud. Diese Cloud nutzt externe Cloud- und Hosting-Dienste. Die Anwendung selbst sowie ihre Datenbank und sämtliche Funktionen (wie Backup und Replikation) werden vollständig in einem öffentlichen Cloud-Netzwerk ausgeführt. Diese werden als Multi Tenant Deployments oder Multi-Mandanten-Bereitstellung bezeichnet – Unternehmen teilen sich den Cloud-Speicher, sodass ihre Daten in der Cloud neben den Daten anderer Unternehmen gespeichert werden. Eine öffentliche Cloud ist normalerweise die günstigste Option und wird aufgrund ihrer Skalierbarkeit und Erreichbarkeit eingesetzt. Eine Kombination aus privaten und hybriden Clouds ist in den meisten Fertigungsunternehmen zu finden, da die betrieblichen Anforderungen (Schutz der Fertigungsdaten/IP, Reaktionszeiten, Skalierbarkeit und Zuverlässigkeit/Verfügbarkeit) eher eine risikoarme, besser kontrollierbare Lösung erfordern.
Die Auswahl einer bestimmten Architektur ist sowohl eine Frage der Präferenz als auch der Leistung – die unternehmensinternen Anforderungen an Datensicherheit, Ausfallsicherheit, Verfügbarkeit und Skalierbarkeit beeinflussen die Wahl. Für ein MES wird in der Regel eine Kombination aus unterschiedlichen Cloud-Architekturen für das Anwendungshosting und die Datenverwaltung verwendet, da es sowohl die Echtzeitkomponenten (Datenerfassung) als auch echtzeitnahe Komponenten (Berichterstattung und Analyse) umfasst.
Mehr zu diesem Thema erfahren Sie hier.
Critical Manufacturing bietet innovative Softwaretechnologie und Dienstleistungen zum Betrieb der modernsten Fertigungen weltweit. Das Manufacturing Execution System (MES) der neuesten Generation steht im Zentrum von Industrie 4.0 durch die weitreichenden Möglichkeiten zur Integration, Mobile Anwendung, Konnektivität sowie logischer Dezentralisation. Das umfassende und durchgängige System erhöht die Performance, Kontrolle und Qualität in komplexen Fertigungsorganisationen.
Das Unternehmen ist Teil der Critical Group, einer 1998 gegründeten private Firmengruppe, die IT-Lösungen für geschäftskritische Anwendungen anbietet.
Für mehr Informationen besuchen Sie unsere Website www.criticalmanufacturing.de oder kontaktieren Sie uns unter kontakt@criticalmanufacturing.de.
Critical Manufacturing Deutschland GmbH
Maria-Reiche-Str. 1
01109 Dresden
Telefon: +49 (351) 4188-0639
Telefax: +49 (35205) 120020
http://www.criticalmanufacturing.de
Managing Director / Geschäftsführer
Telefon: +49 (351) 41880639
E-Mail: Tom.Bednarz@criticalmanufacturing.de
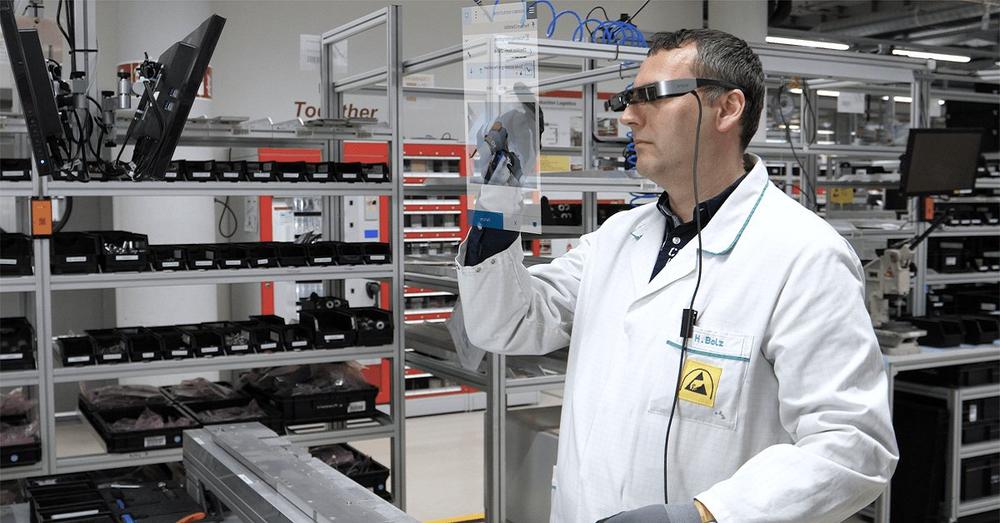
Wie begeistert man Unternehmen für Industrie 4.0?
Die Vorreiter aus unterschiedlichen Branchen, darunter Klein-, Mittelstand- und Großunternehmen, haben die Führung übernommen und sich die Vorteile dieser neuen Revolution zu eigen gemacht, um der Welt aufzuzeigen, welche Erfolge damit möglich sind. Die Hauptvorteile der Industrie 4.0 bieten unter anderem:
- Eine unternehmenskulturelle Neuausrichtung: die Zusammenarbeit der Mitarbeiter, ihre Arbeitsweise und Kundenbetreuung
- Verbesserte Produktionsmetriken: Qualität, Durchsatz, verringerter Ausschuss, verbesserte Maschinenverfügbarkeit sowie Rückverfolgbarkeit
- Vereinheitlichte Datenaggregation für einen Single Point of Truth für Fertigungsabläufe.
Unternehmen, welche die digitale Transformation strategisch angehen und die für diese neue Revolution notwendigen Veränderungsschritte vollziehen, stärken ihre Wertschöpfungskette und haben so die Möglichkeit, beispiellose Ergebnisse im Rahmen ihrer operativen Geschäftstätigkeit und der erweiterten Lieferkette zu erreichen.
Was genau ist Industrie 4.0?
Es gibt immer noch viele Vorbehalte und Unsicherheiten seitens Industrieunternehmen auf der ganzen Welt hinsichtlich der Frage, ob der Industrie-4.0-Ansatz tatsächlich umgesetzt werden sollte oder nicht. Manche Unternehmen sind der Meinung, man sollte abwarten und sich erst einmal selbst ein Bild davon machen, welche Vorteile für andere Unternehmen durch ihre Initiativen zur digitalen Transformation erzielt werden. Andere sind der Meinung, es sei besser, einen einzelnen Teilaspekt des gesamten Technologiespektrums von Industrie 4.0 zu verfolgen, als zu versuchen, alle wesentlichen Anwendungsfälle einzubeziehen, sodass die Implementierung fragmentarisch erfolgt.
Gehen wir nun einen Schritt zurück. Heute sprechen wir über das allgemeine Industrie-4.0-Konzept und die Methoden zu seiner Umsetzung. Wir werden außerdem herausfinden, warum die digitale Transformation der Wertschöpfungskette JETZT beginnen muss, also nicht erst dann, wenn es möglicherweise schon zu spät ist.
Zunächst einmal sprechen wir über den berühmten Elefanten im Raum: Was genau ist die Industrie 4.0? In unserem Whitepaper "Manufacturing Software for Industry 4.0, Embracing Change and Decentralization for Success" ist eine gute Definition zu finden. Mit einfachen Worten: die Industrie 4.0 ist die vierte Etappe der industriellen Revolution.
Sogenannte cyber-physische Systeme – also die Verknüpfung der realen und der virtuellen Welt – dienen als Grundlage dieser vierten industriellen Revolution. Diese cyber-physischen Systeme beruhen auf Basistechnologien wie eingebettete Elektronik, Kommunikation, Datenverarbeitung, mobile Systeme, Cloud Computing, moderne Analyseverfahren, 3D-Druck und kollaborative Community-Plattformen.
Das Industrie-4.0-Potenzial für Fertigungsunternehmen beschränkt sich nicht nur auf eine Kostenreduzierung, eine Qualitätsverbesserung und einen höheren Durchsatz/eine schnellere Verarbeitung, vielmehr geht es um einen Personalisierungs-Faktor bei kleineren Losgrößen, im Prinzip um die Losgröße „Eins“. Die größte Zukunftsvision von Industrie 4.0 beschreibt einen Marktplatz, wo intelligente Produkte und smarte Geräte autonom miteinander kommunizieren und so eine dynamische Online-Optimierung ermöglichen.
Erfahren Sie mehr zu diesem Thema hier.
Critical Manufacturing bietet innovative Softwaretechnologie und Dienstleistungen zum Betrieb der modernsten Fertigungen weltweit. Das Manufacturing Execution System (MES) der neuesten Generation steht im Zentrum von Industrie 4.0 durch die weitreichenden Möglichkeiten zur Integration, Mobile Anwendung, Konnektivität sowie logischer Dezentralisation. Das umfassende und durchgängige System erhöht die Performance, Kontrolle und Qualität in komplexen Fertigungsorganisationen.
Das Unternehmen ist Teil der Critical Group, einer 1998 gegründeten private Firmengruppe, die IT-Lösungen für geschäftskritische Anwendungen anbietet.
Für mehr Informationen besuchen Sie unsere Website www.criticalmanufacturing.de oder kontaktieren Sie uns unter kontakt@criticalmanufacturing.de.
Critical Manufacturing Deutschland GmbH
Maria-Reiche-Str. 1
01109 Dresden
Telefon: +49 (351) 4188-0639
Telefax: +49 (35205) 120020
http://www.criticalmanufacturing.de
Managing Director / Geschäftsführer
Telefon: +49 (351) 41880639
E-Mail: Tom.Bednarz@criticalmanufacturing.de
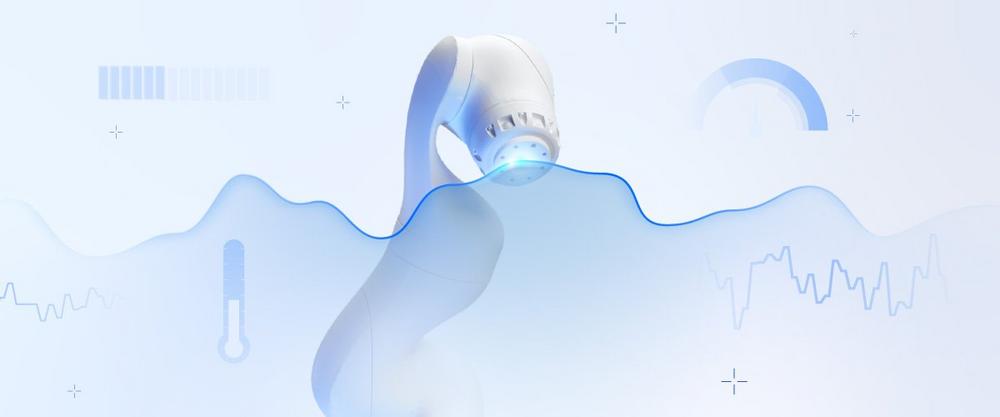
Revolutionäre IoT-Datenplattform in Kombination mit MES bietet Einblicke in die Zukunft der Fertigung
Die Industrie verfolgt mit atemberaubender Geschwindigkeit Projekte im Bereich des industriellen Internet der Dinge (Industrial Internet of Things, IIoT). Die Fertigungsindustrie ist allerdings – trotz der höchsten Anzahl eingesetzter IoT-Geräte im Vergleich zu anderen Branchen – nach wie vor kaum dazu in der Lage, den maximalen Wert der Daten auszuschöpfen. Der Grund dafür sind fehlende spezifische Lösungen für die Fertigung.
Die neue IoT-Datenplattform von Critical Manufacturing wurde dazu entwickelt, die Herausforderung hinsichtlich der Fertigungsdaten anhand eines neuen Ansatzes zu bewältigen, bei dem IIoT-, MES-, Anlagenintegrations- und Datenplattformelemente zur Datenverarbeitung und Analyse eingesetzt werden. So wird die Gewinnung zuverlässiger Informationen und echter Erkenntnisse aus der Fertigung für bessere Geschäftsergebnisse beschleunigt.
Francisco Almada Lobo, Critical Manufacturing CEO, sagt: „Wir sind Augenzeugen einer wahren Revolution, ob es sich nun um das IIoT, Big Data, künstliche Intelligenz oder Industrie 4.0 handelt. Die Daten stehen bei all diesen Ansätzen im Mittelpunkt. Wir sind überzeugt, durch die Kombination des IoT mit unserem modernen MES eine bahnbrechende Lösung geschaffen zu haben. Unsere neue IoT-Datenplattform wurde speziell für Fertigungsunternehmen entwickelt, um wertvolle Informationen in kürzester Zeit aus bisher unmöglichen Einblicken zu gewinnen und diese in praktische Maßnahmen umzusetzen, und somit einen schnellen ROI im Rahmen des Fertigungsbetriebs zu erreichen.“
Eine End-to-End-Datenlösung für tiefere Einblicke in Fertigungsprozesse
Die Critical Manufacturing IoT-Datenplattform ist eine umfassende, hochskalierbare Lösung, die alle erforderlichen Funktionen für eine ganzheitliche Datenverwaltung und -analyse mit Edge Processing, Data Ingestion, Data Brokering, Datenverarbeitung sowie Datenbereitstellung und Ausgabe umfasst. Die IoT-Datenplattform unterscheidet sich von anderen Lösungen durch den speziellen MES-Datenanreicherungsprozess, die Kontextualisierung und die Rückführung der MES-Daten in einen geschlossenen Regelkreis, sodass sichergestellt ist, dass Probleme holistisch gelöst werden.
Die Plattform ermöglicht die Aufnahme großer, strukturierter und unstrukturierter Datenmengen aus IoT-Geräten, aus dem MES sowie aus weiteren Datenquellen wie etwa ERP und PLM. Diese Lösung bietet außerdem ein allgemeines Datenmodell, ein einzigartiges MES-Anreicherungsverfahren und ermöglicht die Integration von Fremdlösungen mit der Datenplattform, um so einige der häufigsten Fehlerursachen bei der Umsetzung von IIoT-Projekten abzuschwächen. Die IoT-Datenplattform baut auf zwei allgemein bekannten und bewährten universellen Technologien auf und nutzt die Streaming-Datenplattform Apache Kafka™ sowie die integrierte Analyse-Engine Apache Spark™, die u.a. hohe Datenspeicherungs- und IT-Kosten in Unternehmen reduzieren.
Mit diesen Technologien können alle Daten sofort gespeichert und verarbeitet werden, ebenso können Ereignisse nach Bedarf später wiedergegeben werden. Data Scientists und Ingenieure erhalten Zugang zu den Daten, um besser zu verstehen, was derzeit und möglicherweise in der Zukunft geschehen wird. Die Fertigungsunternehmen profitieren von einer verkürzten Entscheidungsphase und einer termingerechten Problemlösung, da die Daten im jeweiligen Kontext analysiert werden. Die Kosten der Datenspeicherung werden gesenkt und die Datensicherheit gewährleistet, da die Lösung entweder direkt vor Ort oder in einer Cloud-basierten Umgebung eingesetzt werden kann.
Francisco Almada Lobo setzt fort: „Die neue Critical Manufacturing IoT-Datenplattform verfügt über alle wichtigen Komponenten, um die Konnektivität zu transformieren und Daten mit ausreichender Detailgenauigkeit für die Erstellung maschineller Lernmodelle sowie prädiktiver und präskriptiver Analysen zu liefern. Die Fertigungsunternehmen können mit den neuen leistungsstarken Erkenntnissen einen schnellen ROI mit Use Cases erreichen, die solche Maßnahmen wie vorausschauende Wartung und Ertragssteigerung vorantreiben und die Trennung zwischen IT und OT überbrücken, um alle wichtigen Daten zu verbinden. Das allgemeine IoT- und MES-Datenmodell ist für die IoT-Datenplattform von wesentlicher Bedeutung, denn es liefert kontextspezifische Informationen und ermöglicht so die Generierung von zuverlässigen Erkenntnissen.“
Weitere Module des neuen Critical Manufacturing MES V8 mit IoT-Plattform
Das neue Critical Manufacturing MES V8 bietet außerdem die neuen Module Fabrikautomatisierung und Materiallogistik. Das Modul Fabrikautomatisierung ist eine Workflow-Engine auf Fabrikebene, die zur Koordinierung unterschiedlicher Systeme und Anwendungen zum Erreichen eines höheren Automatisierungsgrades entwickelt wurde. Dieses neue Modul ist ein weiterer Schritt zum vollautomatisierten "Lights-Out"-Produktionsprozess. Die High-Tech-Unternehmen können damit eine höhere Widerstandsfähigkeit und Reaktionsfähigkeit erreichen, indem mögliche Störungen abgewendet und die Abhängigkeit von menschlichen Arbeitskräften reduziert werden.
Mit dem Modul Fabrikautomatisierung ist eine Verbesserung der Betriebseffizienz, Produktivität, Produktqualität und Maschinenauslastung, eine Verkürzung der Zykluszeiten bei gleichzeitiger Reduzierung der Arbeitskosten möglich. Alle Ereignisse in der Fabrik können überwacht und die richtigen Gegenmaßnahmen aus unterschiedlichen Systemen und Anwendungen koordiniert werden. Anwender können spezifische Arbeitsabläufe anlegen und ausführen, darunter die Berechnung von Prozessschritten für die nächste Maschine für fertiggestellte oder im Prozess befindliche Lose, sowie die Steuerung automatisierter Transportfahrzeuge oder Materialtransportsysteme. Die uneingeschränkte Flexibilität dieses Moduls erlaubt die schrittweise Erweiterung der Fähigkeiten zur automatisierten Fertigung und die Kombination von automatisierten und manuellen Szenarien entsprechend den Anforderungen der betreffenden Fertigungsprozesse.
Mit dem neuen Modul Materiallogistik werden alle Geschäftsprozesse rund um die Materialflüsse verwaltet. Dieses Modul bietet ein integriertes Lagermanagement für die Just-in-Time-Fertigung und unterstützt den gesamten Materiallogistik-Lebenszyklus bei optimaler Materialverfügbarkeit und -fluss. Fertigungsunternehmen erhalten mit dieser Funktionalität eine höhere Transparenz und eine genauere Rückverfolgbarkeit der Materialien, darüber hinaus werden Materialengpässe reduziert, Materialanfragen schneller abgewickelt, die Lagerverwaltung verbessert, der Ausschuss minimiert und die Gesamtkosten für die Materialverwaltung verringert.
Das neue Critical Manufacturing MES V8 ist eine der vollständigsten und modernsten Fertigungslösungen auf dem Markt. Unsere Lösung wurde entwickelt, um die Zukunft der Fertigung neu zu definieren und den Unternehmen die notwendige Flexibilität zu bieten, schnell und in einem Maße zu wachsen und sich anzupassen, sodass sich ändernde Geschäftsanforderungen optimal erfüllt werden.
Francisco Almada Lobo weiter: „Diese neue Softwareversion bedeutet für produzierende Unternehmen eine wichtige Etappe auf dem Weg zu einer integrierten intelligenten Fertigungsumgebung, mit der sie heute und auch zukünftig wettbewerbsfähig bleiben können. Die vollständig integrierten IOT- und MES-Funktionalitäten schließen dabei eine Lücke, die mit herkömmlichen IoT-Plattformen nicht überbrückt werden konnte, und werden, meiner Meinung nach, die zukünftige Nutzung der Fertigungsdaten, welche das Fundament für die optimale Ausschöpfung der Industrie-4.0-Vorteile bilden, deutlich verbessern. Die Industrie muss sich nicht länger zwischen der Investition in eine IoT-Plattform oder in ein MES entscheiden – beide Technologien können nun in einer Gesamtlösung genutzt werden. Und das ist eine echte Revolution.“
Critical Manufacturing bietet innovative Softwaretechnologie und Dienstleistungen zum Betrieb der modernsten Fertigungen weltweit. Das Manufacturing Execution System (MES) der neuesten Generation steht im Zentrum von Industrie 4.0 durch die weitreichenden Möglichkeiten zur Integration, Mobile Anwendung, Konnektivität sowie logischer Dezentralisation. Das umfassende und durchgängige System erhöht die Performance, Kontrolle und Qualität in komplexen Fertigungsorganisationen.
Das Unternehmen ist Teil der Critical Group, einer 1998 gegründeten private Firmengruppe, die IT-Lösungen für geschäftskritische Anwendungen anbietet.
Für mehr Informationen besuchen Sie unsere Website www.criticalmanufacturing.de oder kontaktieren Sie uns unter kontakt@criticalmanufacturing.de.
Critical Manufacturing Deutschland GmbH
Maria-Reiche-Str. 1
01109 Dresden
Telefon: +49 (351) 4188-0639
Telefax: +49 (35205) 120020
http://www.criticalmanufacturing.de
Managing Director / Geschäftsführer
Telefon: +49 (351) 41880639
E-Mail: Tom.Bednarz@criticalmanufacturing.de
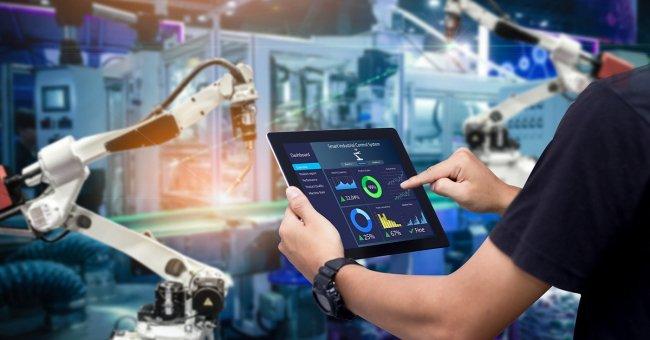
Vishay wählt Critical Manufacturing MES als globale Standardanwendung für die Fertigung von passiven elektronischen Bauteilen
Dr. Thomas Amrein, VP Planning & Systems Passive Components / Business Process Owner Planning & Manufacturing bei Vishay, sagt: „In unserem Geschäftsbereich, der Fertigung passiver elektronischer Bauelemente, setzen wir unterschiedliche und teils veraltete Legacy-Systeme ein. Dieses Projekt räumt die Risiken und Kosten aus dem Weg, die mit deren Instandhaltung einhergehen, und schafft eine effizientere, benutzerfreundliche Alternative, die uns in die digitale Zukunft bringen wird.“
In Vishay‘s Fabriken für die Herstellung passiver elektronischer Bauelemente wird oftmals eine Kombination aus Legacy- und herkömmlichen kommerziellen Systemen genutzt. Aufgrund zahlreicher Übernahmen der letzten Jahrzehnte werden viele unterschiedliche Tools und Anwendungen mit jeweils spezifischer Hardware, Software und Infrastruktur eingesetzt. Angesichts der Vielzahl unterschiedlicher Systeme ist es schwierig, diese zu supporten und zugleich die Wechselwirkungen zwischen den einzelnen Bereichen der Fabrik genau zu verstehen.
Dr. Amrein setzt fort: „Wir haben uns mit mehreren Softwareanbietern befasst und uns anschließend für Critical Manufacturing entschieden, denn ihr System zeichnet sich durch einen modernen, objektorientierten Ansatz aus, passt zu unseren funktionalen und technischen Anforderungen und bietet Flexibilität sowie eine ausgezeichnete Rentabilität.“
Francisco Almada Lobo, Critical Manufacturing CEO, bemerkt: „Unser MES ist besonders darauf ausgerichtet, die benötigte Flexibilität zu bieten, um die Anforderungen anspruchsvoller Fertigungsabläufe, wie etwa bei Vishay’s Passives-Fertigung, zu erfüllen. Sie bietet ein Grundgerüst für Industrie-4.0 in der Fertigung sowie eine Datenplattform zur Steigerung der Effizienz und Anpassungsfähigkeit an veränderliche Geschäftsanforderungen.“
Die hier im Pilotprojekt eingesetzte Critical Manufacturing MES-Lösung umfasst die Materialverfolgung, SAP- und Maschinenintegration sowie die Unterstützung manueller Arbeitsstationen. Das Modul Connect IoT ermöglicht eine einfache Integration von modernem und Legacy-Equipment sowie IoT-Geräten und bietet eine zentrale grafische Ansicht der gesamten Automatisierungsabläufe. So können Ingenieure komplexe Logiken intuitiv erstellen und aktualisieren, ganz ohne zusätzlichen Programmieraufwand. Diese zukunftsweisende Technologie ermöglicht einen Einstieg in eine zunehmend intelligente Produktionsumgebung. Diese Entwicklung erfolgt dabei mit einer Geschwindigkeit, die den Anforderungen und der Strategie des Unternehmens angemessen ist.
Dr. Amrein stellt fest: „Dies ist eine spannende Entwicklung für unser Geschäft im Bereich passive elektronische Bauelemente, die, aus meiner Sicht, weitere Innovationen fördern wird. Das Critical Manufacturing MES bietet uns eine Plattform, mit der das Risiko veralteter Legacy-Systeme verringert und gleichzeitig das Wissen, wie Daten sowie die Best Practices aus unseren internationalen Betrieben zusammengeführt werden. Auf diese Weise werden kontinuierliche Prozessverbesserung und -harmonisierung sichergestellt und so eine verbesserte Effizienz und Qualität erreicht, sodass die Anforderungen unserer Kunden heute und auch in der zunehmend digitalisierten Zukunft erfüllt werden können. Wir werden dadurch noch stärker und flexibler und können so Anpassungen und Veränderungen aufgrund neu entstandener Märkte und Technologien schnell umsetzen.“
„Wir verfügen über langjährige Erfahrung in der Elektronikindustrie und sind erfreut, dass Vishay unsere Lösung gewählt hat. Wir freuen uns darauf, Vishay bei der Steigerung von Leistung und Flexibilität innerhalb ihres weitreichenden globalen Fertigungsnetzwerks zu unterstützen“, fasst Almada Lobo abschließend zusammen.
Über Vishay Intertechnology, Inc.
Vishay verfügt über eines der weltweit größten Portfolios an diskreten Halbleitern und passiven elektronischen Komponenten, die für innovative Designs in den Automobil-, Industrie-, Computer-, Konsumgüter-, Telekommunikations-, Rüstungs-, Luft- und Raumfahrt- sowie Medizinmärkten von grundlegender Bedeutung sind. Die Philosophie The DNA of tech.™ wird bei Vishay Intertechnology, Inc. seit mehreren Jahrzehnten gelebt und macht es zu einem Fortune-1.000-Unternehmen, das an der NYSE (VSH) notiert ist. Mehr über Vishay erfahren Sie unter www.vishay.com.
Über Critical Manufacturing
Critical Manufacturing bietet das modernste, flexibelste und am besten konfigurierbare Manufacturing Execution System (MES), das Unternehmen dabei unterstützt, bei der strikten Rückverfolgbarkeit von Produkten und bei Compliance-Maßnahmen immer einen Schritt voraus zu sein, Qualitätsrisiken durch geschlossene Regelkreise zu verringern, ihre MES-Lösung in die Enterprise Ebene und die Fabrikautomatisierung nahtlos zu integrieren, sowie tiefgreifende Intelligenz und Transparenz über globale Produktionsprozesse zu erreichen.
Somit sind unsere Kunden Industrie 4.0-fähig und können sich dadurch jederzeit und überall an den geänderten Bedarf, neue Chancen oder Anforderungen anpassen. Weitere Informationen finden Sie unter www.criticalmanufacturing.com.
Critical Manufacturing bietet innovative Softwaretechnologie und Dienstleistungen zum Betrieb der modernsten Fertigungen weltweit. Das Manufacturing Execution System (MES) der neuesten Generation steht im Zentrum von Industrie 4.0 durch die weitreichenden Möglichkeiten zur Integration, Mobile Anwendung, Konnektivität sowie logischer Dezentralisation. Das umfassende und durchgängige System erhöht die Performance, Kontrolle und Qualität in komplexen Fertigungsorganisationen.
Das Unternehmen ist Teil der Critical Group, einer 1998 gegründeten private Firmengruppe, die IT-Lösungen für geschäftskritische Anwendungen anbietet.
Für mehr Informationen besuchen Sie unsere Website www.criticalmanufacturing.de oder kontaktieren Sie uns unter kontakt@criticalmanufacturing.de.
Critical Manufacturing Deutschland GmbH
Maria-Reiche-Str. 1
01109 Dresden
Telefon: +49 (351) 4188-0639
Telefax: +49 (35205) 120020
http://www.criticalmanufacturing.de
Managing Director / Geschäftsführer
Telefon: +49 (351) 41880639
E-Mail: Tom.Bednarz@criticalmanufacturing.de
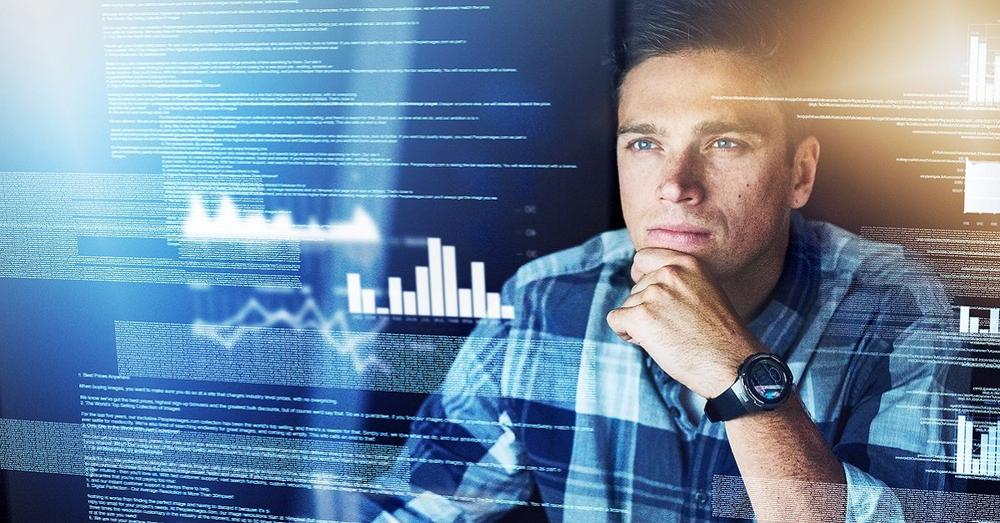
MES und Sicherheit
Dies ist legitim; denn Datensicherheit und -integrität sind für Führungskräfte ein wichtiger Aspekt, selbst wenn ihr ursprüngliches strategisches Ziel darin besteht, die Wertschöpfungskette so auszurichten, dass das Unternehmen auf die neue industrielle Revolution vorbereitet ist.
Warum ist Sicherheit also ein wichtiger Aspekt? Die Industrie 4.0 schafft einen Mehrwert vor allem durch stark vernetzte "intelligente" Systeme, die über Netzwerke miteinander kommunizieren und die Erfassung, Verarbeitung und Übertragung großer Datenmengen zwischen Bereichen und Instanzen ermöglichen. Auf diese Weise werden intelligente Informationen erzeugt, die zu gewünschten automatisierten Abläufen und verbesserter vollautomatischen oder teil-automatischen Entscheidungsfindung beitragen. Dadurch wird über die gesamte Produkt- oder Dienstleistungslieferkette hinweg der erwünschte Nutzen erzielt, indem datenbasiertes Wissen für Entscheidungen herangezogen wird, um so eine verbesserte Effizienz, geringere Kosten und schnellere Geschäftsergebnisse zu erreichen.
Die eigentliche Aufgabe von Industrie 4.0, die auf Hyperkonnektivität aufbaut, ist zugleich auch der Grund dafür, weshalb sie zum Ziel von Angriffen werden kann. Jedes neue Gerät oder jeder neue Nutzer mit Zugang zum System, das als solches vielschichtige Systeme, Geräte und zahlreiche Anwender umfasst, die ständig über das Internet oder lokal über Netzwerke interagieren, kann eine potentielle Bedrohung hervorrufen. Dadurch wird die Herstellung der Gesamtsicherheit des Systems entlang der Wertschöpfungskette zu einer großen Herausforderung und einem immer wichtigeren Bestandteil der Datensicherheit, da der Vernetzungsgrad und die Datenmenge innerhalb der Wertschöpfungskette künftig weiter ansteigen werden.
Hinzu kommt die Tatsache, dass die Konnektivität zwischen IT-Anwendungen, -Equipment und -Geräten heute zwar keine so große Herausforderung darstellt wie noch vor zehn Jahren, die Gewährleistung der Systemsicherheit nach der Anbindung aus der Perspektive eines Datenschutzverstoßes bei der aktuellen technologischen Landschaft jedoch eine völlig neue Dimension bedeutet. So sind die Tools zur Umsetzung von Industrie 4.0 zwar bereits verfügbar, die erforderliche Sicherheitsinfrastruktur, wie z.B. einheitliche und klar definierte Richtlinien, branchenspezifische Sicherheitsprotokolle und grundlegende Sicherheitsmaßnahmen, wie Zugriffskontrolle, sind jedoch noch immer nicht ausgereift. Tatsächlich könnte es sogar einige Jahre dauern, bis das gewünschte Sicherheitsniveau erreicht ist, welches mit dem Niveau der Konnektivität vergleichbar ist.
Der Verlust sensibler Informationen bspw. Rezepturen, urheberrechtlich geschütztes geistiges Eigentum rund um das Design bestehender oder neuer Produkte, der Verlust sensibler Kundendaten oder der Systemkontrolle aufgrund von Malware-Angriffen sowie Datenverlust durch unberechtigten Zugriff – all dies stellt insbesondere für produzierende Unternehmen eine ernste existenzielle Gefährdung dar. Diese Verletzungen können Schäden verursachen, die über die eigentlichen rein finanziellen Verluste des Angriffs selbst weit hinausgehen. So können unter Umständen der Markenname und das Image eines Unternehmens ruiniert werden, was irreparable und unumkehrbare Schäden in seiner gesamten Wertschöpfungskette nach sich zieht. Jedes Unternehmen, das einen öffentlich bekannt gewordenen Cyber-Angriff erlebt hat, wird nur schwer seinen Kundenstamm aufrechterhalten können, vor allem dann, wenn die betroffenen Daten einen besonders sensiblen Charakter aufweisen.
Diese Problematik ist für Unternehmen offensichtlich und umfasst u.a. mögliche Kompromisse in Bezug auf Datensicherheit, welche notwendig sind, um die Umsetzung von Industrie 4.0 zu fördern. Das Risiko für die Datensicherheit und -integrität muss allerdings nicht zwingend hoch sein und die Sicherheit muss nicht geopfert werden, um Industrie 4.0 schnell in der Praxis umzusetzen. Mit der richtigen Vorgehensweise kann ein Industrie-4.0-Implementierungsprojekt gegen mögliche Cyber-Angriffe und andere Sicherheitsverletzungen unempfindlich gemacht werden. Wichtig ist, die Sicherheit bereits vor der geplanten Einrichtung zu berücksichtigen und keine kurzfristigen Erfolge gegenüber langfristiger Sicherheit zu priorisieren; darauf werden wir später noch genauer eingehen.
Lesen Sie den kompletten Blog-Beitrag zu diesem Thema hier.
Critical Manufacturing bietet innovative Softwaretechnologie und Dienstleistungen zum Betrieb der modernsten Fertigungen weltweit. Das Manufacturing Execution System (MES) der neuesten Generation steht im Zentrum von Industrie 4.0 durch die weitreichenden Möglichkeiten zur Integration, Mobile Anwendung, Konnektivität sowie logischer Dezentralisation. Das umfassende und durchgängige System erhöht die Performance, Kontrolle und Qualität in komplexen Fertigungsorganisationen.
Das Unternehmen ist Teil der Critical Group, einer 1998 gegründeten private Firmengruppe, die IT-Lösungen für geschäftskritische Anwendungen anbietet.
Für mehr Informationen besuchen Sie unsere Website www.criticalmanufacturing.de oder kontaktieren Sie uns unter kontakt@criticalmanufacturing.de.
Critical Manufacturing Deutschland GmbH
Maria-Reiche-Str. 1
01109 Dresden
Telefon: +49 (351) 4188-0639
Telefax: +49 (35205) 120020
http://www.criticalmanufacturing.de
Managing Director / Geschäftsführer
Telefon: +49 (351) 41880639
E-Mail: Tom.Bednarz@criticalmanufacturing.de