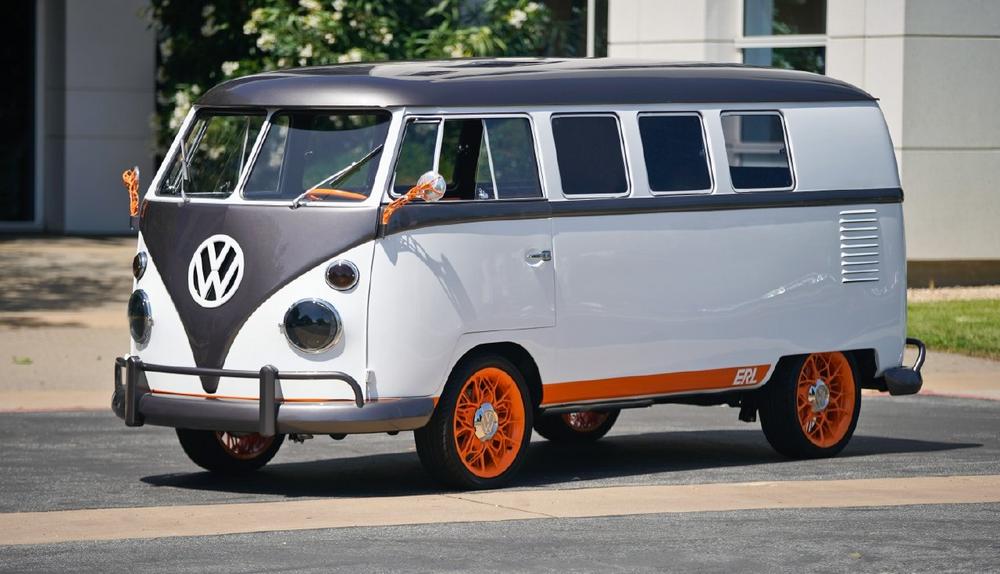
E-Variante des beliebten VW Bulli wird mit dem Generativem Design-Ansatz von Autodesk neugestaltet
- Felgen, Lenkrad und weitere Elemente mit Fusion 360 überarbeitet
- Autodesks Generativer Design-Ansatz ermöglicht Gewichtseinsparung bei Elektrofahrzeugen
Der Volkswagen Konzern hat einen überarbeiteten und mit Elektromotor ausgestatteten Oldtimer-VW-Bus präsentiert. Mehrere Komponenten des beliebten VW Bulli Typ 2 wurden dazu mit Autodesks Generativem Design-Ansatz optimiert. Der innovative Ansatz reduziert den Materialverbrauch und ermöglicht signifikante Gewichtseinsparungen – und damit einen besseren Energieverbrauch und mehr Reichweite.
„Je weniger ein Automobil wiegt, desto weniger Energie wird benötigt, um es auf der Straße zu bewegen“, erklärt Karl Osti, Industry Manager Manufacturing bei Autodesk. „Genau hier kann Generatives Design einen erheblichen Vorteil leisten. Unter Einhaltung der technischen Anforderungen, bietet es die Möglichkeit, bei gleichbleibender Stabilität den Materialverbrauch zu minimieren und somit leichtere Teile herzustellen.“
Traditionsdesign kombiniert mit neuster Technik
Ein sparsamerer Energieverbrauch eines Autos ist gleichbedeutend mit größerer Reichweite pro Akkuladung – einer der wichtigsten Aspekte für Verbraucher bei der Bewertung von Elektrofahrzeugen. Daher kooperierte das kürzlich umbenannte Innovation and Engineering Center California (IECC) von VW mit Autodesk. „Wir kombinieren ein klassisches Volkswagen-Design mit neuen Ideen und innovativen Technologien von Kooperationspartnern wie Autodesk”, sagt Nikolai Reimer, Executive Director vom IECC.
Das IECC-Team hat die Felgen des 1962er 11-Fenster-Mikrobus vom Typ 2 mit Fusion 360 generativ gestaltet und die Struktur dabei völlig neu überdacht. Die neuen Räder sind 18 Prozent leichter als die ursprünglichen und reduzieren so nicht nur das Gesamtgewicht des Fahrzeugs, sondern verringern auch den Rollwiderstand der Reifen. Außerdem wurde die gesamte Entwicklungszeit von der Konstruktion bis zur Fertigung von anderthalb Jahren auf wenige Monate reduziert.
„Mit Generativem Design ist es möglich, Strukturen zu schaffen, die wir als menschliche Designer und Ingenieure sonst nie hätten realisieren können“, sagt Andrew Morandi, Senior Product Designer des Volkswagen Konzerns. „Eine der größten Überraschungen für mich war die Erkenntnis, wie viel Material man von einer herkömmlichen Radstruktur entfernen kann.“
Im Rahmen des Bulli-Projekts wurde auch das Lenkrad sowie die Trägerstruktur für die Rücksitzbank und die Außenspiegelhalterungen neugestaltet. Ein Lenkrad ist nicht besonders schwer, aber es ist der entscheidende Berührungspunkt für den Fahrer. Durch den direkten Kontakt wird nun nicht nur der ästhetische Aspekt, sondern auch die Stabilität der neu gestalteten Teile vermittelt.
Generatives Design ist ein relativ neuer Designansatz, um schnell eine breite Palette von Designlösungen zu generieren. Mit der Leistungsfähigkeit und Geschwindigkeit der Cloud spielt die generative Designsoftware jede geometrisch mögliche Option durch und zeigt – basierend auf Werkstoffen, Herstellungsverfahren und Anforderungen an die Leistungsfähigkeit des Objekts – schließlich Hunderte (wenn nicht gar Tausende) von Optionen an. Sobald sich der Designer, Konstrukteur oder Ingenieur einen Überblick über die vielen verschiedenen Lösungsmöglichkeiten für ein bestimmtes Konstruktionsproblem verschafft hat, kann er diejenigen auswählen, die am besten zu seinem Projekt passt. Dieser Prozess spart nicht nur Zeit und Geld, sondern auch Ressourcen. Dieser innovative Ansatz steht für Anwender von Autodesk Fusion 360 zur Verfügung, die Produktentwicklungsplattform, die Design, Engineering und Fertigung in einer einzigen Software vereint.
Autodesk entwickelt Software für Menschen, die Dinge erschaffen. Wenn Sie jemals einen Sportwagen gefahren sind, einen Wolkenkratzer bewundert, ein Smartphone benutzt oder einen guten Film gesehen haben, haben Sie wahrscheinlich ein Ergebnis davon gesehen, was Millionen Kunden von Autodesk mit unserer Software erschaffen. Autodesk gibt Anwendern die Möglichkeit, alles zu entwickeln. Weitere Informationen erhalten Sie auf autodesk.de oder auf Twitter unter @autodesk_de.
Autodesk GmbH
Aidenbachstr. 56
81379 München
Telefon: +49 (89) 54769-0
Telefax: +49 (89) 54769-400
http://www.autodesk.de
Edelman GmbH
Telefon: +49 (221) 828281-32
E-Mail: Autodesk_Germany@edelman.com
Communications Manager Germany
Telefon: +49 (89) 54769-347
E-Mail: autodesk_Germany@edelman.com
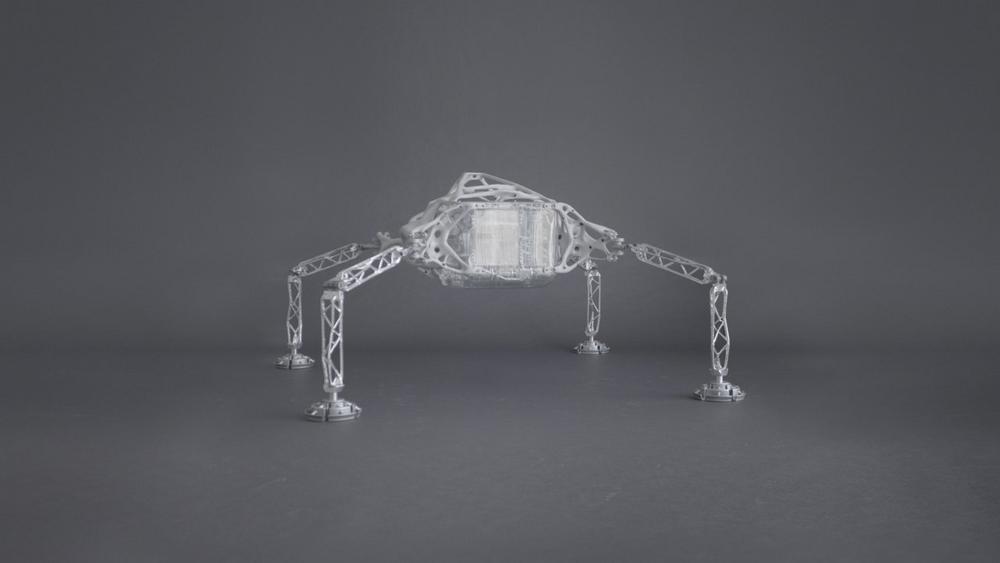
Autodesk arbeitet mit dem Jet Propulsion Laboratory (JPL) der NASA zusammen, um ferne Planeten und Monde zu erkundigen
- Autodesk und JPL kooperieren bei dem Bau eines Raumfahrt-Landers
- Autodesks Generatives Design ermöglicht Gewichtseinsparungen beim Lander
Um den Herausforderungen an einen Raumfahrt-Lander – also eine Art Fahrzeug zur Erkundung von Planeten – gerecht zu werden, haben Autodesk und das Jet Propulsion Laboratory der NASA ein gemeinsames Forschungsprojekt gestartet: Mithilfe von Generativem Design konnten sie die Masse der äußeren Struktur des Landers um 35 Prozent reduzieren. In der Vergangenheit hatte die NASA rollende Fahrzeuge eingesetzt, der Entwurf des laufenden Landers auf vier Beinen ist eine der kompliziertesten Konstruktionen, die jemals mit Generativem Design erstellt wurde.
Generatives Design ermöglicht Masseneinsparungen
Im Jahr 2012 beobachtete die Welt, wie der Curiosity-Rover per Fallschirm auf dem Mars landete und damit begann, Proben zu sammeln. Die zurückgesandten Daten und Bilder halfen dabei, mehr über den roten Planeten und die Möglichkeiten des Lebens dort zu erfahren, und er ist auch heute noch im Einsatz. Die Mission war ein wichtiger Erfolg für die Entwickler und Ingenieure des Jet Propulsion Laboratory (JPL) der NASA. Aber bisher wurden nur wenige Beweise für das Leben auf dem Mars gefunden. Wissenschaftler gehen nun davon aus, dass die wahrscheinlichsten Orte, an denen in unserem Sonnensystem Lebenszeichen gefunden werden können, auf den Monden von Saturn und Jupiter liegen. Diese Gasriesen liegen jedoch viel weiter entfernt als der 56 Millionen Kilometer entfernte, vergleichsweise nahe, Mars.
Einen Raumfahrt-Lander in diese entfernten Gebiete zu bringen, stellt daher eine weitaus größere Herausforderung dar: Um eine so weite Reise zu überstehen, muss ein Raumfahrt-Lander komplizierte Betriebsfunktionen bei Temperaturen weit unter null Grad Celsius erfüllen und den Strahlungen standhalten, die tausende Male größer sind als auf der Erde. Zusätzlich muss er genügend Treibstoff an Bord haben. Gleichzeitig ist in der Weltraumforschung allerdings das Gewicht beim Start einer der wichtigsten Faktoren. Jedes reduzierte Kilogramm Masse ermöglicht mehr Raum für Sensoren und Instrumente, die nach Leben jenseits der Erde suchen können.
Um diesen Anforderungen gerecht zu werden, haben JPL und Autodesk ein mehrjähriges gemeinsames Forschungsprojekt gestartet, um neue Ansätze für Design- und Herstellungsverfahren für die Weltraumforschung zu entwickeln – und der Generative Design-Ansatz von Autodesk spielte hierbei eine ganz besondere Rolle.
Mit Generativem Design in kürzester Zeit unzählige Designentwürfe generieren
Generatives Design ist ein relativ neuer Designansatz, der maschinelle Intelligenz und Cloud Computing nutzt, um schnell eine breite Palette von Designlösungen zu generieren, die den spezifischen Anforderungen der Ingenieure entsprechen. Der Ansatz ermöglicht es Designteams, einen viel größeren Designraum zu erforschen, während sie gleichzeitig an Fertigungs- und Leistungsanforderungen geknüpft sind, die vom Team oder der Umgebung vorgegeben sind.
Eine marktreife Form der Generativen Design-Technologie ist heute in Autodesk Fusion 360 verfügbar, der Cloud-basierten Produktentwicklungsplattform von Autodesk. Autodesk entwickelt die Software kontinuierlich für den Einsatz in neuen Anwendungsgebieten weiter, beispielsweise mit JPL.
Für das Lander-Projekt untersuchte das JPL-Team den Einsatz experimenteller Generativer Design-Technologie für mehrere Strukturkomponenten, einschließlich der internen Struktur, die die wissenschaftlichen Instrumente hält, und der externen Struktur, die die Landerbeine mit der Hauptnutzlastbox verbindet. Es wurden drei verschiedene Herstellungsverfahren für die verschiedenen Teile des Landers eingesetzt: 3D-Druck, CNC-Fräsen und Gießen. Das Team konnte die Masse der externen Struktur um 35 Prozent reduzieren, verglichen mit dem Ausgangsdesign, mit dem es begonnen hat.
Ein wesentlicher Vorteil des Generativen Designs von Autodesk ist, dass es JPL ermöglicht hat, seine Entwürfe schnell zu wiederholen und gegebenenfalls zu bearbeiten. „Wenn ein Design reift und neue Leistungs- oder Umweltdaten einfließen, kann das Generative Design unseren Kunden ermöglichen, schnell neue Designs zu erstellen“, sagt Karl Willis, Technology Lead bei Autodesk. Die meisten Designteams würden in der Regel zwei bis vier Monate benötigen, um ein überarbeitetes Design zu erstellen, betont er. Bei der Arbeit mit Generativem Design könne dieser Prozess in zwei bis vier Wochen stattfinden. „Diese Flexibilität und Schnelligkeit, eine bestehende Problemstellung zu aktualisieren, anstatt bei Null anzufangen, kombiniert mit der Fähigkeit für Kunden, Produktionsanforderungen festzulegen, machen es zu einem echten Paradigmenwechsel“, sagt Willis.
Autodesk entwickelt Software für Menschen, die Dinge erschaffen. Wenn Sie jemals einen Sportwagen gefahren sind, einen Wolkenkratzer bewundert, ein Smartphone benutzt oder einen guten Film gesehen haben, haben Sie wahrscheinlich ein Ergebnis davon gesehen, was Millionen Kunden von Autodesk mit unserer Software erschaffen. Autodesk gibt Anwendern die Möglichkeit, alles zu entwickeln. Weitere Informationen erhalten Sie auf autodesk.de oder auf Twitter unter @autodesk_de.
Autodesk GmbH
Aidenbachstr. 56
81379 München
Telefon: +49 (89) 54769-0
Telefax: +49 (89) 54769-400
http://www.autodesk.de
Edelman GmbH
Telefon: +49 (221) 828281-32
E-Mail: Autodesk_Germany@edelman.com
Communications Manager Germany
Telefon: +49 (89) 54769-347
E-Mail: autodesk_Germany@edelman.com
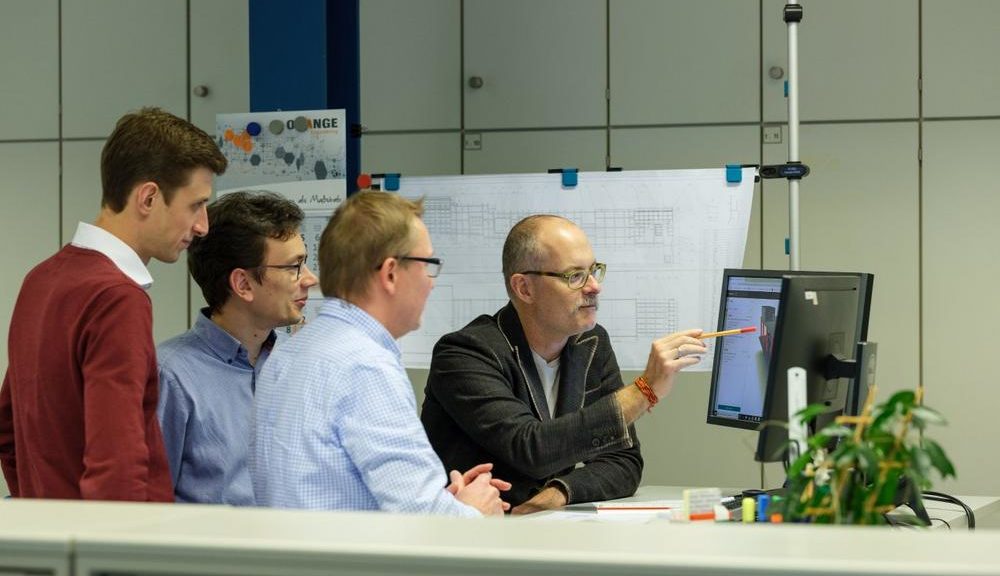
Schwermaschinenhersteller setzt auf Generativen Design-Ansatz von Autodesk
- Neue Produktentwicklungstechnologien machen 100 Jahre altes Unternehmen fit für die Fertigung der Zukunft
- Generatives Design liefert überraschendes Ergebnis und entwirft leichtere Komponente von einem Klinkerkühler
- Generativ konstruierte Teile auch mit traditioneller Fertigung herstellbar
Claudius Peters (CP), ein über hundert Jahre alter Hersteller von Schüttgutverarbeitungsanlagen, macht sich fit für das 21. Jahrhundert. Dabei ist das Generative Design ein entscheidender Faktor für das deutsche Unternehmen und bietet einen völlig neuen Ansatz für Produktdesign und -optimierung. Durch die Anpassung dieser Technologie – die eng mit dem 3D-Druck verknüpft ist – an traditionelle Fertigungsmethoden stellt das Unternehmen kosteneffizientere Produkte für einen preissensiblen Industriemarkt her. In der Schwerindustrie unterstützt Generatives Design dabei, Material- und Energiekosten sowie Durchlaufzeiten zu reduzieren. Claudius Peters stellt sich so wettbewerbsfähiger als zuvor auf.
Eine Traditionsfirma auf Innovationskurs
Thomas Nagel, Chief Digital Officer und Operations Director bei Claudius Peters, wurde 2017 erstmals auf den Generativen Design-Ansatz von Autodesk aufmerksam und entschied sich, in diesen Bereich zu investieren. Nur ein Jahr später wurde Claudius Peters für seine Leistungen bei der Einführung von Generativem Design als Innovator of the Year von Autodesk ausgezeichnet. Zu den Zielen der Initiative gehören die Steigerung der Kundenzufriedenheit, die Verbesserung der Qualität sowie die Reduzierung von Durchlaufzeiten und Kosten.
Die Generative Design-Software von Autodesk zahlt genau auf diese Ziele ein: Sie berücksichtigt Designziele und -beschränkungen und zeigt in kürzester Zeit Dutzende Umsetzungsmöglichkeiten auf. So optimierte das Team mithilfe des Generativen Design-Ansatzes eine Komponente aus einem der Kernprodukte für die Zementindustrie – einen Klinkerkühler.
Die Klinkerproduktion verbraucht viel Energie und macht die Zementindustrie zu einem der weltweit größten CO₂-Emittenten. Anfang der 2000er-Jahre begann Claudius Peters mit der Entwicklung eines Klinkerkühlers der nächsten Generation. Der sogenannte ETA Cooler ist auf einen möglichst sparsamen Energieverbrauch ausgelegt. „Einer der größten Vorteile unseres ETA Coolers ist der hervorragende thermische Wirkungsgrad“, sagt Nagel. „Diese Energieeinsparungen tragen dazu bei, die Umweltauswirkungen der Zementproduktion zu reduzieren.“ Heute ist das Hauptgeschäft von Claudius Peters der Austausch bestehender Klinkerkühler durch ETA Cooler zur Effizienzsteigerung in Zementwerken.
Generatives Design führt zu Gewichtsreduktion
Claudius Peters entschied sich für Generatives Design, um eine Komponente des ETA Coolers zu optimieren. Dabei handelt es sich um ein Schwermetallteil, das kürzlich neu entwickelt wurde, um überschüssiges Material zu entfernen. Jeder Kühler besteht aus 50 bis 60 dieser Teile. „Diese sind mit Förderbahnen verschraubt, die den geschmolzenen Klinker durch den ETA Cooler transportieren. Dieses Gussteil wurde immer wieder optimiert“, sagt Maximilian Lerch, Konstrukteur bei CP. „Das Ziel war es, das Gewicht und die damit verbundenen Kosten des Metalls zu senken. Schon eine kleine Gewichtsoptimierung hätte einen großen Effekt.”
Nach einer ersten vierstündigen Sitzung zu Generativem Design hatte das Team das erste Ergebnis: „Wir nannten es The Alien Part“, sagt Nagel. Das Ergebnis hat überrascht, denn es unterschied sich stark von dem bereits optimierten Teil und war sogar 30 Prozent bis 40 Prozent leichter.
Kombination von generativ konstruierten Teilen und traditioneller Fertigung
Das Team begann, das Design zu analysieren, um so die beste Produktionsmöglichkeit herauszufinden. „Generative Designs verwenden normalerweise 3D-Druck oder andere additive Herstellungsverfahren, um das Produkt herzustellen“, sagt Nagel. „Unsere Branche verwendet keine 3D-Druckteile – das ist zu teuer. Aber mit Ideen aus dem Generativen Design und der traditionellen Optimierung haben wir nur eine Woche gebraucht, um das Teil zurückzuentwickeln, damit wir es mit traditionellen Fertigungsmethoden herstellen können.“
Mit Inventor- und FEM-Analysen testete das Team verschiedene Fertigungslösungen mit der Gießerei von Claudius Peters. „Wir haben uns entschieden, von einem Gussteil zu einer Lösung mit lasergeschnittenen Platten und Schweißen überzugehen“, sagt Nagel.
Auch das Gewicht des Transportteils ließ sich um etwa 20 Kilogramm reduzieren. Das Unternehmen rechnet dadurch mit Einsparungen von etwa 100 Euro pro Teil, multipliziert mit 60 oder mehr Teilen pro Kühler. Darüber hinaus bedeutet weniger Gewicht auch niedrigere Versandkosten sowie weniger Auswirkungen auf die Umwelt. „Vom ersten entwickelten Prototyp waren wir überzeugt, dass uns Generatives Design helfen wird, niedrigere Kosten für unsere Produkte zu erzielen und unsere Wettbewerbsfähigkeit zu erhöhen“, sagt Nagel. „Ich erwarte, dass die Komponente noch in diesem Jahr eingesetzt wird.“
Die Potenziale des Generativen Designs ausschöpfen
Claudius Peters befindet sich nun an dem Punkt, an dem sich das Generative Design zum Standardprozess für die Optimierung bestehender oder die Konstruktion neuer Teile entwickelt. „Wir werden weitere Teile identifizieren, an denen wir in Zukunft Optimierungen und Materialreduzierungen vornehmen“, so Nagel. „Wenn wir unsere Reise mit Partnern wie Autodesk fortsetzen, bleiben wir auf dem Markt wettbewerbsfähig“.
Weitere Informationen finden Sie unter http://www.autodesk.de/redshift/claudius-peters.
Autodesk entwickelt Software für Menschen, die Dinge erschaffen. Wenn Sie jemals einen Sportwagen gefahren sind, einen Wolkenkratzer bewundert, ein Smartphone benutzt oder einen guten Film gesehen haben, haben Sie wahrscheinlich ein Ergebnis davon gesehen, was Millionen Kunden von Autodesk mit unserer Software erschaffen. Autodesk gibt Anwendern die Möglichkeit, alles zu entwickeln. Weitere Informationen erhalten Sie auf autodesk.de oder auf Twitter unter @autodesk_de.
Autodesk GmbH
Aidenbachstr. 56
81379 München
Telefon: +49 (89) 54769-0
Telefax: +49 (89) 54769-400
http://www.autodesk.de
Edelman GmbH
Telefon: +49 (221) 828281-32
E-Mail: Autodesk_Germany@edelman.com
Communications Manager Germany
Telefon: +49 (89) 54769-347
E-Mail: autodesk_Germany@edelman.com