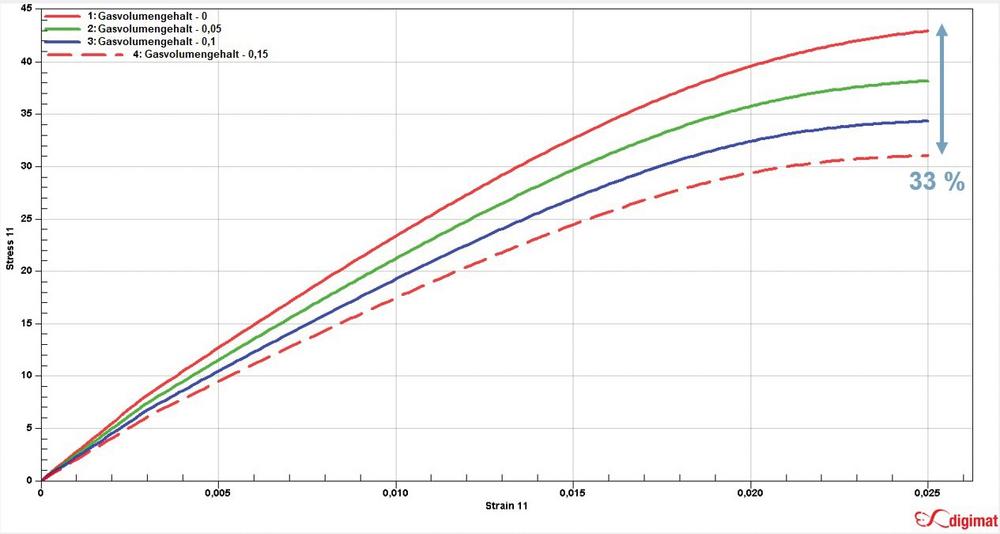
Ganzheitliche virtuelle Produktentwicklung
Treibende Kräfte und Weiterentwicklungspotential zeigen sich in den letzten Jahren verstärkt vor allem im Bereich Leichtbau. Dies nicht zuletzt, da sich hauptsächlich auch aus der Automobilindustrie Handlungszwänge hinsichtlich Reduktion der CO2 Emissionen ergeben. Neben Herstellungsverfahren der Faserverbundtechnologie geraten dabei zunehmend auch Prozesse und Verfahren der Spritzgussverarbeitung in den Fokus einer notwendigen Veränderung, eines erforderlichen progressiven Fortschritts. Einerseits steigt die Komplexität der Produkte, andererseits stehen Faktoren, wie die notwendige Reduktion der Produktionsschritte, anspruchsvolle Designanforderungen sowie auch höchste Erwartungen an die mechanischen Eigenschaften des finalen Produktes, als Schwerpunkte des Herstellungsprozesses im Raum.
Ein Verfahren, das aufgrund seines Potenzials immer mehr in den Fokus rückt, ist unter anderem das Schäumen von Kunststoffen, gemeint ist sowohl das chemische als auch das physikalische Schäumen. Notwendigerweise stehen bei Einführung dieser innovativen Technologie Investitionen an, neben den offensichtlich monetären, zusätzlich auch Investitionen in die Infrastruktur, die Produktentwicklung, die Ausbildung des Personals, die Aufrüstung der technischen Ausstattung und resultierende Umstrukturierungen der Arbeitsabläufe. So musste anfangs ein, ursprünglich für den Kompaktspritzguss ausgelegtes Werkzeug, rein verfahrenstechnisch angepasst werden. Die Anpassungen verliefen mit teils sehr unterschiedlichen Erfolgen, waren entsprechend breit gefächert und oft schwer kalkulierbar. Im positiven Fall konnten tatsächlich Gewichtsreduktionen erzielt werden. Aber es gab auch die negativen Fälle, bei denen die Resultate nicht den Erwartungen entsprachen. Das Für und Wieder zum Herstellungsverfahren „Schäumen“ gestaltet sich dementsprechend durchaus zwiespältig. Es ist nach wie vor eine Technologie mit Potential, aber auch eins, in das noch einiges an Entwicklungs- und Forschungsaufwand eingebracht werden muss.
Doch wie sieht es nun tatsächlich auf der Seite der Entwicklung geschäumter Bauteile aus? Bis heute werden Aufgaben und Schritte meist getrennt voneinander betrachtet, analysiert und angegangen. So erfolgt einerseits die Entwicklung des Produktes direkt vom Designer zum Werkzeugkonstrukteur. Zusätzlich führt ein Produktentwicklungsweg zu einer weiteren Abteilung, welche unabhängig von der Analyse und Betrachtung des Prozesses, Berechnungen im Rahmen der mechanischen Simulation durchführt. So erfolgt, die Simulation des Herstellungsprozesses in der Regel im Produktdesign und/oder in der Werkzeugkonstruktion. Dort gilt es die grundsätzliche Herausforderung zu meistern, erforderliche Anpassungen des Prozesses in den passenden, effektiven Arbeitsschritten und -abläufen zu realisieren, ganz selbstverständlich zu integrieren. Im Rahmen des Produktdesigns müssen beispielsweise Wandstärkenverhältnisse von Grundkörpern und Rippen überdacht werden. Auch in der Werkzeugkonstruktion werden Anpassungen notwendig, zum Beispiel hinsichtlich der Anbindungen.
Interessant für die Produktentwicklung ist aber auch, wie sich geschäumte Produkte unter mechanischer Last verhalten und wie deren Auslegung erfolgen sollte. Traditionell werden diese Betrachtungsschritte bisher in separaten Abteilungen vollzogen, eine Folge des unterschiedlichen Fokus des jeweiligen Aufgabenfeldes.
Seit einigen Jahren stehen hinsichtlich des Herstellungsverfahrens „Schäumen“ zunehmend auch Fragestellungen, wie die der Verarbeitung von faserverstärkten Kunststoffen im Fokus. Ein Verfahren mit enormen Entwicklungspotential vor allem in Blickrichtung „Leichtbau“. Die „üblichen“, bereits dargestellten, unabhängigen Produktentwicklungsschritte finden sich auch hier. Doch wird damit das Potential der Technologie vollständig und effektiv ausgenutzt? Ist ein Umdenken erforderlich, da zielführender? Und falls ja, welche technologischen und vor allem welche zeitlichen und finanziellen Auswirkungen haben diese Anpassungen?
Zur Beantwortung dieser Fragestellungen gilt es zunächst, den aktuellen Status zu bilanzieren. So stellt man fest, dass die zu einer Verbesserung notwendigen Werkzeuge häufig bereits existieren. Ebenfalls stellt sich nicht die Frage, wie mit diesen Werkzeugen umgegangen wird. Sondern vielmehr, wie gewonnene Resultate bewertet, eingesetzt und wie sie bzw. an wen sie kommuniziert werden.
Ein elementarer Aspekt liegt in der üblichen Herangehensweise bei der mechanischen Auslegung von Produkten, egal ob aus faserverstärkten Kunststoffen, mittels physikalischen oder chemischen Schäumens oder ähnlichen Verfahren hergestellt. Denn diese Betrachtungsmethode erfolgt meist unter der Annahme der gleichen mechanischen Eigenschaften für das gesamte Bauteil. Doch genau hier, liegt der Knackpunkt, durch diese Vorgehensweise werden die Möglichkeiten dieser Technologien deutlich reduziert und unvollständig ausgeschöpft, da nur einseitig betrachtet.
Welches Potential liegt in der Verknüpfung dieser Arbeitsschritte – die der Betrachtung des Prozesses und die der mechanischen Eigenschaften – zu einem Kreislauf verborgen?!! – In der Vereinigung zweier bisher unabhängiger Komponenten in einem Kreislauf, um die Substanz der virtuellen Produktentwicklung maßgeblich zu ergänzen, exponentiell zu verbessern.
So trivial es auch heute noch klingen mag, eine gute Basis aller Schritte liegt in der Durchgängigkeit der Konstruktionsdaten. Der Einsatz verschiedener CAD-Programme ist bis heute eine Quelle möglicher resultierender Herausforderungen. So sind die Details jedes CAD-Kernels (nicht CAD-Programmes) nicht einheitlich und es kann durch Datenimport und -export zu unerwünschten Überlappungen von Flächen oder anderen Fehlern kommen. Da zur Erzeugung von Produktdesign und Werkzeugkonstruktion oft zweierlei CAD-Programme eingesetzt werden, tritt dieses Phänomen meist häufig auf. Zur notwendigen Nacharbeit bzw. Aufbereitung der Daten für die Simulation stehen sowohl CAD-Programme als auch darauf spezialisierte Softwaretools zur Verfügung.
Die Prozesssimulation liefert die Basis für die Bewältigung möglicher, zu erwartender, zu bewältigender Herausforderungen aufgrund des Herstellungsprozess, des Produktdesign, der Werkzeugkonstruktion und/oder des Werkstoffs geschäumter Bauteile. Berechnet, analysiert, bewertet und optimiert wird der gesamte Prozess von Füllung über Abkühlung bis hin zur Simulation der Deformation. Zu den geläufigen Simulationsergebnissen des Schäumens zählen vor allem zwei, welche die einen teils erheblichen Einfluss auf weiteren Entwicklungsschritte haben. Zum einen die Zellgrößen- und zum anderen die Zelldichteverteilung. Diese beiden Resultate erlauben nicht nur einen Rückschluss bezüglich „kosmetischer“ Fragenstellungen. Vielmehr widerspiegeln sie, wie stark die lokale Randschicht ausgeprägt, ob mit mehr oder weniger Schlieren auf der Oberfläche zu rechnen und wie hoch die zu erwartende Deformation des finalen Bauteils ist. Weiterhin klären sie auch verfahrensrelevante Fragestellungen, ob möglicherweise der Einsatz einer variothermen Temperierung empfehlenswert ist.
Der entscheidende Aspekt für die erfolgreiche Kopplung zweier bisher unabhängiger Komponenten – der Prozesssimulation und der Strukturmechanik – in einem Produktentwicklungskreislauf liegt nun im folgenden Schritt. Lange Zeit wurden, wie bereits dargelegt, diese beiden Methoden zur Herstellung sicherheitsrelevanter Produkte außen vorgelassen, da eine durchgängige simulative Prozess- wie auch mechanische Simulation nicht möglich sein sollte. Doch bei Berücksichtigung einiger wichtiger Aspekte gelingt genau das und darüber hinaus ergibt sich sogar ein maximal nutzbarer positiver Effekt. Die Beschreibung der entstandenen Zellen kann über Porositätsergebnisse von Moldex3D (für die Prozesssimulation eingesetztes Simulationsprogramm) an das Softwaretool Digimat zwecks Materialmodellierung übergeben werden. Die daraus resultierenden lokal unterschiedlichen Materialkennwerte werden dann an die strukturmechanische Simulation weitergegeben. Die Relevanz dieser Vorgehensweise wird in der Abbildung 1 verdeutlicht. Hier ist ein Spannungs-Dehnungsdiagramm in Abhängigkeit von der Mikrostruktur abgebildet.
Auf diesem Weg wird sichergestellt, dass die lokalen unterschiedlichen Zustände des Materials entsprechend berücksichtigt werden und somit anschließend gezielte Korrekturen des Bauteils in Bezug auf die mechanischen Eigenschaften realisiert werden können. Die anschließende Überprüfung der geometrischen Anpassungen erfolgt wieder mittels Prozesssimulation. Resultierende, optimierte Prozesssimulationsergebnisse werden wiederholt zum Export in die Mechanik vorbereitet. Der Kreislauf schließt sich. Dieser Vorgang kann manuell durchgeführt werden. Allerdings bietet sich hier auch die Möglichkeit eines weitestgehend automatischen Optimierungsablaufes. Ein Vorteil der Optimierung liegt darin, dass neben dem klassischen DoE-Ansatz auch geometrische Anpassungen ermöglicht werden, bis hin zur automatischen Topologieoptimierung.
Letztendlich stellt sich die Frage, wie sehr lohnt sich dieser Aufwand? Anhand eines konkreten Bauteils, einer Blende (siehe Abbildung 2) sollen die Vorteile näher dargestellt werden.
Im Rahmen der Prozesssimulation wurde neben dem Bauteil zusätzlich das gesamte Temperier- und Verteilersystem dargestellt, berechnet und analysiert, hier in Abbildung 3 ersichtlich.
In Abbildung 4 wird die simulierte Zellstruktur (links) mit einer CT Aufnahme verglichen. Ersichtlich ist eine komplette Übereinstimmung der berechneten Werte und der Realität. Die relevanten Resultate der Porosität aus dem Schäumprozess wurden anschließend an Digimat übertragen. Mit den dort erzeugten Materialkarten wurde anschließend innerhalb der FEA ein Drei-Punkt-Biegeversuch berechnet. Parallel dazu wurde dieser Versuch ebenfalls mit dem realen Bauteil durchgeführt.
Das resultierende Kraft/Weg Diagramm ist in der Abbildung 5 abgebildet. Es ist hier deutlich zu erkennen, wie sehr die isotropen Ansätze von der realen Messung (hier in pink) abweichen. Dies gilt mitunter nicht nur für den quantitativen Verlauf, sondern auch vor allem dem qualitativen Aspekt des Versagens. In diesem Diagramm sind ferner die ersten Resultate (in blau) der durchgängigen Berechnung dargestellt, welche sowohl im qualitativen wie auch quantitativen eine sehr gute Übereinstimmung zur Realität darstellt.
Zusätzlich wurden mit dem gleichen Produkt (der Blende) auch Optimierungsläufe durchgeführt. Der Vergleich begann mit der Betrachtung des Verfahrens des Kompaktspritzguss gegenüber dem des Schäumens. Damit konnte das Bauteilgewicht bereits um 10.1% reduziert werden. In einem weiteren Schritt wurde das Produktdesign optimiert. So wurde die Rippenstruktur auf der Unterseite der Blende mittels des sogenannten Sizeing‘ optimal an die geforderten Randbedingungen angepasst. Ein Anpassungsschritt gemäß der Optimierung aufgrund mechanischer Eigenschaften. Erzielt wurde eine weitere Reduktion des Gewichtes um 5%. Zudem wurde die Optimierung des Fertigungsprozesses in den Produktentwicklungsprozess eingebunden. So konnte letztlich dank der ganzheitlichen Betrachtungsweise und des fortschrittlichen Optimierungsansatzes eine Gewichtsreduktion von 25% bei gleichzeitiger Verringerung der fertigungsrelevanten Deformationen von gut 50% und einer Verkürzung der Zykluszeit bei der Herstellung von 10% erzielt werden.
Die ganzheitliche virtuelle Entwicklung eines Produktes (siehe Abbildung 6) verdeutlicht zwei wesentliche Aspekte – zum einen ist mit Zuhilfenahme der dargestellten Methodik eine ganzheitliche simulative Betrachtung geschäumter Bauteile real und erfolgreich möglich. Und zum zweiten wird es ganz offensichtlich, auch in Hinblick des Bereiches Leichtbau, in dieser Herangehensweise verbirgt sich ein Potential, das nur darauf wartet, ausgereizt zu werden!
Danksagung:
Wir bedanken uns bei:
- dem Institut für Werkstofftechnik der Universität Kassel für die Unterstützung im Rahmen der Materialcharakterisierung und Durchführung der praktischen mechanischen Versuche,
- der Ineos Styrolution Europe GmbH für das bereitgestellt Material,
- der Firma F. & G. Hachtel GmbH & Co. KG für die Unterstützung bei den CT Aufnahmen sowie
- der Firma Volume Graphics für die Analyse der CT Aufnahmen.
Das resultierende Kraft/Weg Diagramm ist in der Abbildung 5 abgebildet. Es ist hier deutlich zu erkennen, wie sehr die isotropen Ansätze von der realen Messung (hier in pink) abweichen. Dies gilt mitunter nicht nur für den quantitativen Verlauf, sondern auch vor allem dem qualitativen Aspekt des Versagens. In diesem Diagramm sind ferner die ersten Resultate (in blau) der durchgängigen Berechnung dargestellt, welche sowohl im qualitativen wie auch quantitativen eine sehr gute Übereinstimmung zur Realität darstellt.
Zusätzlich wurden mit dem gleichen Produkt (der Blende) auch Optimierungsläufe durchgeführt. Der Vergleich begann mit der Betrachtung des Verfahrens des Kompaktspritzguss gegenüber dem des Schäumens. Damit konnte das Bauteilgewicht bereits um 10.1% reduziert werden. In einem weiteren Schritt wurde das Produktdesign optimiert. So wurde die Rippenstruktur auf der Unterseite der Blende mittels des sogenannten Sizeing‘ optimal an die geforderten Randbedingungen angepasst. Ein Anpassungsschritt gemäß der Optimierung aufgrund mechanischer Eigenschaften. Erzielt wurde eine weitere Reduktion des Gewichtes um 5%. Zudem wurde die Optimierung des Fertigungsprozesses in den Produktentwicklungsprozess eingebunden. So konnte letztlich dank der ganzheitlichen Betrachtungsweise und des fortschrittlichen Optimierungsansatzes eine Gewichtsreduktion von 25% bei gleichzeitiger Verringerung der fertigungsrelevanten Deformationen von gut 50% und einer Verkürzung der Zykluszeit bei der Herstellung von 10% erzielt werden.
Die ganzheitliche virtuelle Entwicklung eines Produktes (siehe Abbildung 6) verdeutlicht zwei wesentliche Aspekte – zum einen ist mit Zuhilfenahme der dargestellten Methodik eine ganzheitliche simulative Betrachtung geschäumter Bauteile real und erfolgreich möglich. Und zum zweiten wird es ganz offensichtlich, auch in Hinblick des Bereiches Leichtbau, in dieser Herangehensweise verbirgt sich ein Potential, das nur darauf wartet, ausgereizt zu werden!
Danksagung:
Wir bedanken uns bei:
dem Institut für Werkstofftechnik der Universität Kassel für die Unterstützung im Rahmen der Materialcharakterisierung und Durchführung der praktischen mechanischen Versuche,
der Ineos Styrolution Europe GmbH für das bereitgestellt Material,
der Firma F. & G. Hachtel GmbH & Co. KG für die Unterstützung bei den CT Aufnahmen sowie
der Firma Volume Graphics für die Analyse der CT Aufnahmen.
SimpaTec Simulation & Technology Consulting GmbH
Wurmbenden 15
52070 Aachen
Telefon: +49 (241) 565276-0
Telefax: +49 (241) 565276-99
http://www.simpatec.com
Manager PR & Social Media
Telefon: +49 (241) 565276-0
Fax: +49 (241) 565282-89
E-Mail: n.baxter@simpatec.com